A strong safety culture starts at the top of any organization, says Lisa Hallsworth
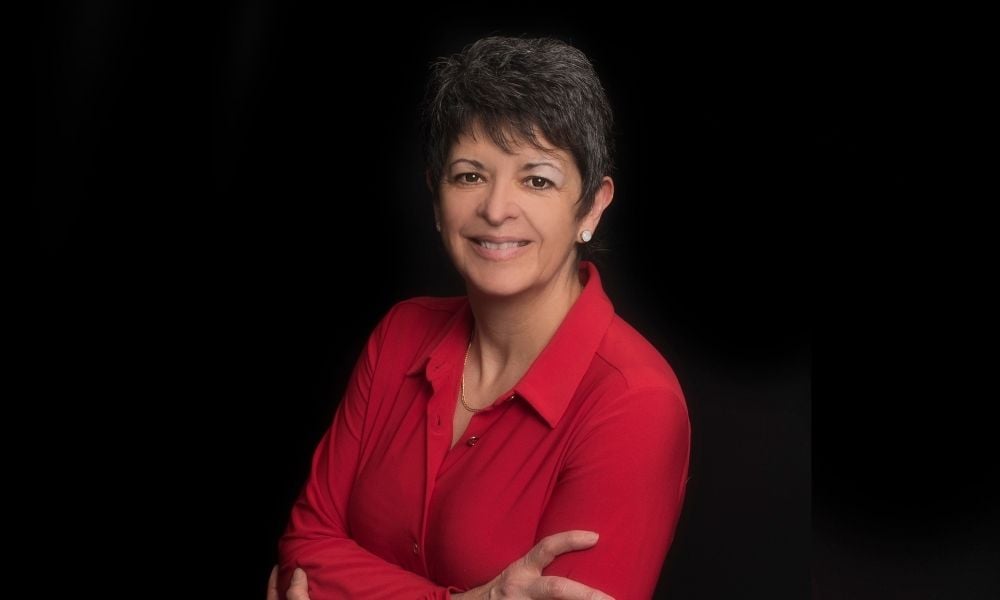
Information for this article was provided by Rillea Technologies.
From effective leadership to entrepreneurial spirit, Lisa Hallsworth exhibits all the characteristics one could hope for at the helm of Safety Data Sheets (SDS) management company Rillea Technologies[MF1] . Having a knack for physics in school, Hallsworth pursued a degree in engineering from the University of Waterloo, opening the door for her entry into the chemical engineering field. Now, with 32 years of industry experience, she explains the motivations behind her vision for improved chemical safety, which led to the creation of cutting-edge safety software, SDS RiskAssist.
“A lot of my time working with chemical safety was spent … looking at the chemicals that were being used and then looking at what various regulations within Canada and around the world had to say about those chemicals,” says Hallsworth. “And that takes a huge amount of time. [For] every different project that I worked on, I’d ask — ‘How is it safe to proceed with this project? What are we required to do by regulations? What do we know about it from research, and how do we handle the chemicals?’ And really, what I came to realize was there is a lot to chemical safety, [which] is super challenging.”
Pondering this conundrum, Hallsworth found herself thinking how there had to be an easier way of approaching such varied requirements across the sheer range of chemical engineering projects in Canada alone. Building software to automatically connect all such regulations with their corresponding chemical products seemed the only logical solution to her. With prompts such as: ’Do you know how this ingredient can harm the environment or people?’ and, ‘Here is what the UK, the EU, the US or the Canadian regulations say’ — workers could then make the best decisions with all critical information at their fingertips, particularly if it could be accessed quickly.
“I wondered how other organisations, [like] a municipality or a hospital, would manage some of these chemicals, because they don't have the expertise that a company like DuPont would have. So, I started asking around — to really understand — ‘How do people manage hazardous chemicals?’ And what I found was: they don't. Very few organisations can afford the resources to properly manage hazardous chemicals,” says Hallsworth. “At best, they manage the WHMIS documents, which is what we're all required to [do]. But lots of those documents are very technical and, in some cases, you need a chemistry degree — and even that doesn't qualify you to really understand what they're trying to tell you. So really, our challenge was to build software that could pull information out from those documents and … organize it in a way that is easy to understand and deliver information back to employees and employers in a way [they can] safely manage the products.”
There are over 200 million chemical ingredients registered with the Chemical Abstracts Service. Many ingredients get combined to create products that we use every day. By way of example, Hallsworth explains how Lowe’s and Home Depot both offer the same types of house-brand paint, but that these products will never exhibit identical chemical compositions. Some chemical companies, such as Sigma Aldrich, can even have up to 25 million data sheets alone. Given the seemingly infinite number of products on the market, SDS RiskAssist shines by custom-tailoring client databases to the hazards that each company is required to handle. This approach enables clients to compare chemicals that are used for a similar function, by hazard, such as comparing different brands of brake cleaner or bathroom cleaner.
“The information that [workers today] are being asked to process — and the pace at which they're being asked to process it — are changing fast; our society is changing fast,” says Hallsworth. “Technology is just making things change faster and faster, and … people are trying to do more with less. We have more people, more expertise, more of those really knowledgeable people retiring from the workplace, and so … workers are being asked to do more with less knowledge — and I think that creates a huge amount of mental stress. Whenever there is mental stress, people are not at their best, and that's when you run the risk of safety being an issue.”
Hallsworth holds that strong safety culture starts at the top of any organization. Leaders just need to ask questions, she says. By showing a genuine interest in worker safety, this concern builds a culture of such values that permeates down through the company. Once employees feel supported in this regard, it becomes easier for them to turn over rocks and expose any shortcomings in safety, regardless of inconvenience or cost.
“A good safety leader is curious. They are willing to go out and talk to the people who are actually working with the products or doing the work,” says Hallsworth. “They try maybe to look at things with fresh eyes, and then realize that sometimes their paradigm is different from the workers’ paradigm, so they're really open to having that conversation between the person who's working with (or in) a certain area, and then bringing their expertise to what they're hearing.”
To learn more about Lisa’s work with Rillea Technologies, or to get a free demo of their next generation Safety Data Sheets management software SDS RiskAssist, please visit their website here.