What you need to know to ensure effective usage of SDSs
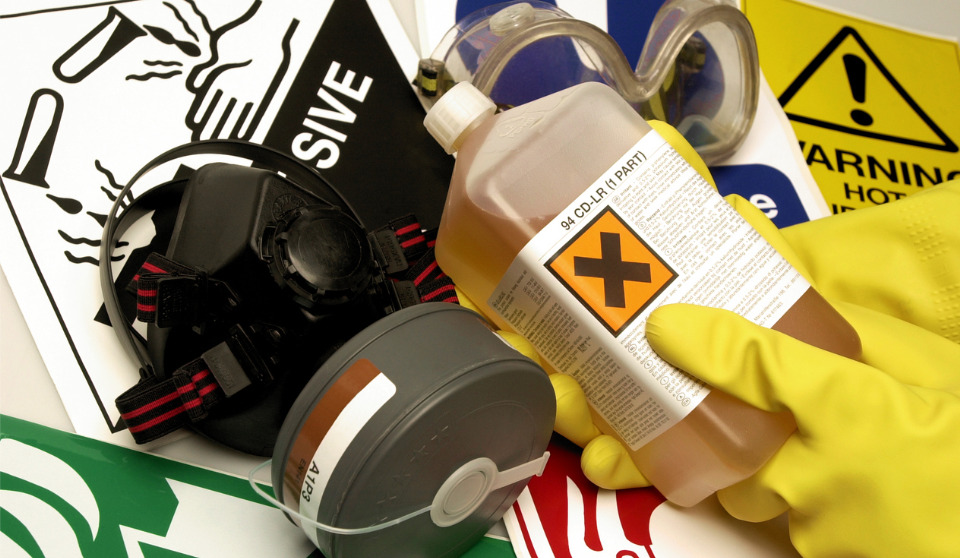
Most workplaces, in some way, have to grapple with chemical safety, from chemical plants that may handle hundreds if not thousands of chemicals a day to less obvious contenders such as beauty salons (e.g., nail technicians are in contact with a host of hazardous substances such as glues and polishes). As such, chemical safety is a concern for most workers. Nevertheless, there is so much data surrounding chemicals that it can be difficult to keep track. This is where Safety Data Sheets come in.
What are Safety Data Sheets (SDS)?
An SDS is a “standardized document that provides detailed information about the hazards of a chemical or mixture, along with instructions on how to mitigate those hazards or respond to an accident,” says Brian McFadden, a technical writer and compliance specialist with Graphic Products.“It’s meant to answer the questions ‘What is this stuff?’ and ‘What do I need to do to stay safe?’”
“From my perspective, the Safety Data Sheet is really the best source of information for anyone who is looking to learn about the chemical product,” says Lisa Hallsworth, CEO of Rillea Technologies.
Hallsworth explains that it is produced to share information with essentially anyone who may come in contact with the chemical product, be it the end user, medical staff, emergency responders, etc. SDSs are compliant with WHMIS 2015 and are built according to very strict criteria for the information shared in the SDS.
“The SDS is a standardized document created by the suppliers that gives you the information that you need … There's lots of technical information in there that the average person is not going to understand, but the real core information, the hazard information is in terms I think every person can understand,” says Rob Hallsworth, COO of Rillea Technologies.
He adds that an SDS does not provide workplace-specific instructions.
“The supplier gives you information, but the employer still has to take that information and understand how to apply it in their workplace based on how they're using the product, what mitigation measures they have available and how they want to protect their employees.”
Some people feel like the SDS should tell you everything that you need to know about the use of a chemical in your workplace, says R. Hallsworth, and it doesn’t. It is up to employers to decide how workers should safely handle that product in their workplace.
“While the SDS is beneficial to all users of chemical products, they are legally required by employers handling hazardous products,” says L. Hallsworth.
Supplier labelling and SDS requirements are set out under the Hazardous Products Act (HPA), which is a federal act. Since occupational health and safety falls under provincial legislation, each Canadian province has adopted WHMIS 2015.
McFadden says the SDS is part of a broader system created by the United Nations (UN) that aims to improve chemical safety. The system, entitled Globally Harmonized System of Classification and Labelling of Chemicals (also known as GHS), is an international project.
As the world becomes more and more interconnected, it became imperative for there to be a unified framework that prevents confusion or miscommunication over chemical safety.
“GHS starts by classifying the hazards of a chemical with objective data and metrics, so that users can agree on exactly what the hazards are,” says McFadden. “Then, the chemical is described with a standardized document (the SDS) to provide an accessible record with detailed information. Finally, each container of the chemical is labelled with standardized elements to ensure that the critical details will always be available to workers who handle that chemical.”
In Canada, the Workplace Hazardous Materials Information System (WHMIS) is aligned with GHS. The GHS is part of national legislation in more than 70 countries. WHMIS is Canada’s national hazard communication standard. The new WHMIS, entitled WHMIS 2015, integrates the GHS. The previous system is known as WHMIS 1988.
Each worksite needs an SDS for each hazardous material present at that site – they need to be easily accessible when needed.
An SDS contains 16 sections: material identification; hazard(s) identification; composition information; first aid measures; firefighting measures; accidental release measures; handling and storage; exposure controls and personal protection; physical and chemical properties; stability and reactivity; toxicological information; ecological information; disposal considerations; transport information; regulatory information; and other information. Ecological information, disposal considerations and transport information are non-mandatory.
What is the purpose of an SDS and who needs it?
An SDS provides “enough information so employers can take the necessary measures to protect workers,” says R. Hallsworth.
“There are now over 150 million different chemicals in existence. There is no way anyone can understand the properties and hazards of each one,” he says.
So, who needs it? “If you have hazardous products, you need Safety Data Sheets,” says R. Hallsworth.
He mentions that some workplaces will have 50 sheets, while others will have more than 50,000!
Generally speaking, says McFadden, you need an SDS for any chemical mixture that is present in the workplace, classified as “hazardous” under applicable regulations and not specifically exempt from the requirements.
“Let’s say you’ve found a chemical that meets those criteria, and you need to find or create an SDS for it. How do you begin? There’s an easy answer here: You can get the document you need from the same place you got the chemical itself,” says McFadden.
He says chemical suppliers are legally obligated to provide a complete and accurate SDS for each hazardous chemical they produce or import and, in fact, many suppliers make their SDSs available online. On the other hand, if it is your organization producing the chemical materials, then it is your organization’s responsibility to produce an SDS that describes it.
“Chemical products are very much integrated with and really critical to our lives as we know it today,” says L. Hallsworth. “For the most part, chemicals developed by the chemical industry are tools used to make things possible, easier, cheaper, last longer, perform better, etc. Examples are glues, coatings, plastic and aluminum coated packaging, cement, insulation, disinfectants, cleaners, pesticides, herbicides, drugs, etc.
“And yet,” she says, “they present hazards and, like COVID-19, the hazards can often be undetected by the human body. So, the only way to know about them is to get educated about those hazards. To me, that is the purpose of the SDS.”
Why are SDSs so important?
“Without the SDS, GHS doesn’t have a reliable way to make sure information about a chemical is available to the recipients of that chemical. The details need to be written down, or they’ll be lost,” says McFadden.
He says there are so many details to manage that they’ll never fit on a singer container label — which is why a longer document is necessary. Furthermore, McFadden says, “to make that document useful, it has to have a logical and consistent format. That’s why the SDS is such a key component of the GHS system: It bridges the gap between suppliers and recipients, as well as the gap between classification and labelling.”
L. Hallsworth says they're really very important because it's the only way for people to understand the potential hazards to workers and the planet.
“Nobody can look at a chemical and identify the hazards,” says R. Hallsworth. “There's too many chemicals. Our senses are not reliable indicators of the hazards. Some things you can smell. But they're not dangerous. Some things you can't smell and they are dangerous. Sometimes, the hazard only appears under certain conditions.”
Furthermore, R. Hallsworth says, the hazard may not appear until many years later; for example, occupational diseases. So, one won’t know until decades later that they’ve been exposed. This is why you have to identify the hazards, he says.
“With the new version [WHMIS 2015], the terminology is really clear. So, if I said to you ‘this product may cause cancer,’ you understand what that means. You don't need a doctor or somebody to interpret it for you,” says R. Hallsworth. “So, it's not just that they identify hazards, but they do it in a way that the average person can understand.”
He also points out that SDSs will also tell you when products aren’t hazardous.
“We have heard many times people say ‘SDSs are a waste of time, we have them for white out, plant food, markers, etc.’ There is a catch-22 with SDSs,” says R. Hallsworth. “The only way to confirm a product is not hazardous is to read the SDS. If it is not hazardous, it still makes sense to keep the SDS in case a question comes up in the future. In an average organization, 1/3 of the SDSs are not hazardous. The challenge is to get people to see the hazards identified in the other products and focus on them.”
What are the challenges created by SDSs?
L. Hallsworth points out the “‘information Tsunami’ — a supplier must update an SDS within 90 days of becoming aware of relevant information that may affect the way a chemical should be handled. Managing the changing SDSs, regulations, worker turnover, worker health is a challenge.”
“The volume of information found in a collection of SDSs is overwhelming. A typical workplace has in excess of 100 SDSs. To give an idea of the volume, consider that an SDS averages 12 pages in length. So, 100 SDSs is 1,200 pages of documentation. That is a lot of reading,” says R. Hallsworth.
L. Hallsworth says employers may often not connect hazards identified in WHMIS with the requirements of the provincial occupational health and safety acts. Furthermore, employers may suffer from a “bystander effect” as a result of the lack of clarity about the role of the SDS.
“Many employers believe that suppliers have included all information needed for workers to use the product safety and that workers will read the SDS,” says L. Hallsworth, but “it is impossible for suppliers to give specific guidance about how a chemical product is to be used because every workplace has different engineering controls such as ventilation and available PPE for workers.”
Furthermore, she says that “reading SDSs is time consuming and even with WHMIS education, the average worker does not feel competent to take on the task. They just expect the employer to tell them how the hazards can affect them and how to use the product safely (i.e., chemical-specific training).”
In addition, R. Hallsworth says that too many products are not covered by the HPA or WHMIS regulations. This can include products such as pesticides, explosives, drugs, etc. The result of this, he says, is that the information provided by these suppliers is not in the same format or may lack the clarity of an SDS.
“The two big challenges that we’ve seen in the adoption of the SDS format are SDS collection and training,” says McFadden. “The keystone in the arch of GHS implementation is training. All your classification and documentation efforts don’t mean much if your people don’t understand what they’re reading or why it matters.”
McFadden says workers and employers need to be trained to understand both chemical hazards and the GHS approach to classifying and documenting these hazards.
Ultimately, McFadden says, “the system doesn’t rely on people memorizing all the details — but it does rely on people knowing where to look to find the answers to their questions.”
This article originally appeared in the Nov/Dec 2020 issue of COS.