Occupational exposure series: Once-thriving industry leaves hundreds of workers ill, battling for compensation
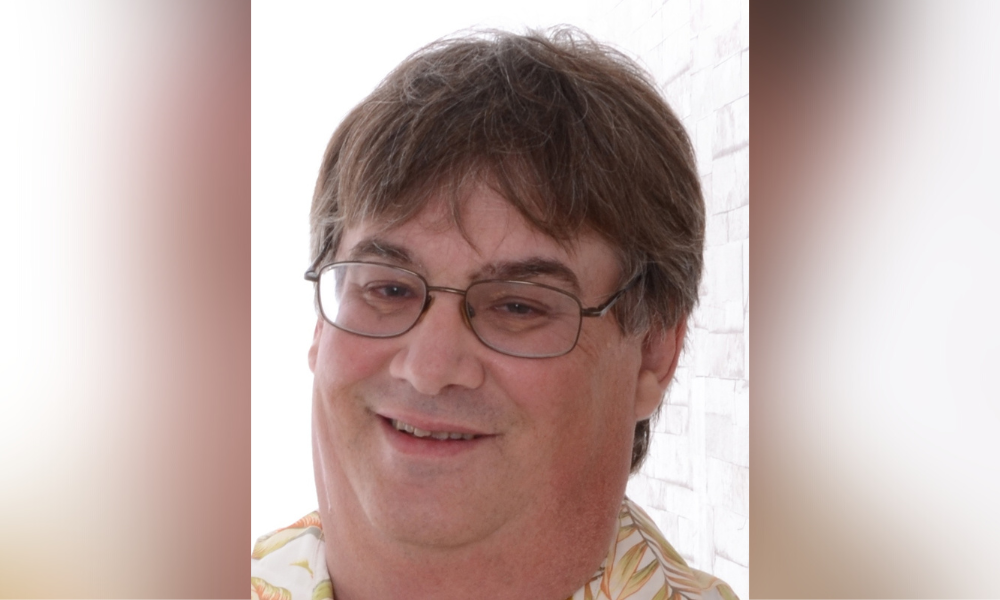
Once upon a time, Kitchener was nicknamed “Rubber Town” on account of the number of rubber factories in the city.
Thousands of employees worked at companies like Dominion Tire, Uniroyal, Canadian Consolidated Rubber and BFGoodrich. Now, few remain.
Gord Assman worked BFGoodrich from 1979 until the plant was shut down in 2006. He became part of the company’s health and safety committee in the mid 90s.
Around six years ago, Assman became chapter president of the Steelworkers Organization of Active Retirees (SOAR) – though he had been involved with the organization before then.
It was during his time on the committee that Assman became acquainted with what eventually transpired to be an issue, not only at BFGoodrich but other rubber companies too: occupational exposures.
“We noticed that there were a lot of cancer deaths,” says Assman. Calls for donations were being frequently posted on the plant’s obituary board.
They thought that there might be something to it, and decided to do further investigate. Eventually, the committee decided to run an intake clinic for rubber workers potentially suffering from workplace exposures. It took a year for the intake clinic to be organized and it was finally held in 2002.
“We realized that there were workers from other plants that could be affected in the region,” says Assman. “We decided to include everybody. It was a two-day clinic originally, but we kept on taking more claims as they came in.”
He estimates that more than 600 people showed up in the first two days, and overall they received around 800 claims.
“Everything from hearing loss to various cancers, and some repetitive strain injuries – but there was a significant amount of cancer claims.”
Many workers decided to start WSIB claim processes. “We had a very good WSIB committee at our plant […] Four guys adjudicating the claims to the best of their ability. I’m not sure how many claims were accepted but expect that it wasn’t a very high percentage,” says Assman.
Even after the plant shut down in 2006, the WSIB committee spend months closing the claims. But after the plant closed, many of the claims eventually went dormant.
Renewed attention
Years later, after he had joined SOAR, Assman was contacted by a worker advisor who had been looking into some of the claims and taking some forward that had new evidence.
In 2018, some of the former workers’ stories were shared in the Waterloo Region Record. The media attention brought to the cluster by the articles reinvigorate advocates, workers and their families:
“That kind of propelled our cause to the forefront again,” says Assman. In 2019, another intake clinic was organized. 300 new claims got filed and reopened in about two years; Assman estimates that around 10 per cent of those claims have been allowed so far.
In one of his articles for The Record, journalist Greg Mercer says that of the 404 WSIB claims initially filed between 2002 and 2017 by many of Kitchener’s former rubber workers, only 15 per cent were accepted.
Bladder cancers
Similarly to many of the other clusters that we have reported on, workers were exposed to a range of potential and confirmed toxic substances.
Assman points out that when he worked at the company, some of the solvents the workers used contained benzene, “for a good period of time when I first started.”
The International Agency for Research on Cancer (IARC) classifies benzene as a carcinogen to humans. The organization notes that benzene exposure has been linked to illnesses such as acute lymphocytic leukemia (ALL), chronic lymphocytic leukemia (CLL), non-Hodgkin lymphoma, and multiple myeloma.
Workers were also exposed to fumes which emanated from mixing the rubber.
“And even though we had a fairly decent air makeup exchange units at the end, they definitely were not there at the beginning,” says Assman. “The fumes in the air affect people differently.”
Workers in different departments were exposed to different chemicals – the rubber mixing areas was an especially hazardous area, chemicals were milled to make different rubbers for various tire components.
Though many occupational diseases develop over time, workers may still feel the immediate effects of working with hazardous substances. Assman says that many workers experienced dermatitis or rashes from being in contact with the materials.
“There was one rubber that had some kind of odor in it. We never did find out why. All rubber stinks, but this was just real strong, and a lot of people complained about getting headaches from it.”
During the original intake clinic in 2002, some progress was made regarding disease recognition. “We got the WSIB to recognize that bladder cancer was prevalent in the rubber industry,” says Assman.
But bladder cancer is far from being the only disease affecting former workers. Over time, workers also developed respiratory issues.
Assman notes that there seem to be a lot of oral cancers that just aren’t on the radar yet. “The trouble is not everybody that gets cancer puts in a WSIB claim. That’s a huge problem, doctors just don’t think of it I guess.”
Better conditions
Working conditions at BFGoodrich evolved over time as more and more Canadian companies integrated safer work practices.
Conditions for rubber workers in the early days were gruelling.
When he was 18, Assman worked at a King Street plant – the original BFGoodrich tire plant before it moved to a new facility in 1962.
Assman says that when he was working at the King Street plant, he wasn’t given a locker to change into work clothes. He would wear the same clothes in and out of work, covered in whatever kind of dust came from the rubber.
Thankfully, the new plant was modern and had better exhaust. But, he says, “when I started in ’79, there weren’t any air makeup units. I can’t remember exactly when they came in, probably seven or eight years after I started there.”
And workers were provided protective gear. “When I first started, there we had hearing protection that was available but not mandatory,” he says. “But as time went on, hearing protection was offered and mandatory – there were some areas that didn’t exceed the noise threshold.”
Respirators were provided as necessary.
“Working conditions, I think, improved as time went on. I think we had a first-rate health and safety committee that would push for improvements continuously,” says Assman. But “most of the time, there was a lot of pushback from the company – they definitely wanted to use the easiest, quickest, cheapest way of addressing things. It wasn’t always the best.”
This is the ninth part of our series on occupational exposures. Over the coming weeks, COS will continue to shine a spotlight on the issue and speak with occupational disease advocates about the dangers of workplace exposures.
Here are the first (miners exposed to aluminium dust), second (exposures at GE plant in Peterborough), third (exposures at Neelon Casting), fourth (Pebra/Ventra Plastics exposures), fifth (interview with Dr. Paul Demers), sixth (WSIB criticism), seventh (WSIB response), and eighth (mill worker exposures) parts of the series.