Know the benefits and limitations of light curtains, mats, new technologies
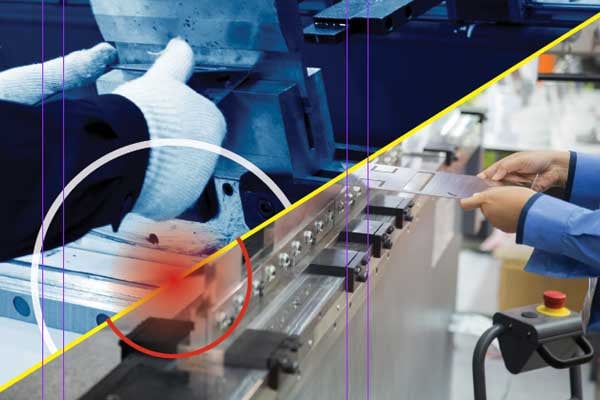
An operator was bending metal parts using a 32-tonne, part-revolution power press brake. The machine, which was operated by foot control, was protected with a light curtain. However, about 3 to 4 inches of the light curtain had been “blanked out,” or bypassed, during an earlier part run. Pausing work to adjust a part at the point of operation, the operator inadvertently activated the foot pedal, starting the machine and cutting off three finger tips.
Presence-sensing safety devices are often chosen over physical guards because they allow easier access for loading parts or for routine maintenance, thus offering increased productivity. Yet, because they do not provide a physical, fixed barrier, safety managers should always remember presence-sensing devices may create a false sense of security and actually increase the possibility of injury. Managers and workers need to know how the various technologies work and, equally important, what their limitations are.
“There are two types of controls,” says Mike Gordon, co-founder of Winnipeg-based Workplace Engineering Solutions. “There are controls, like fences and gates, that prevent access to hazards and there are ones that stop hazardous motion when you enter the danger area. Those are presence-sensing devices. They’re meant both to detect a worker, a part of that worker and to stop hazardous motion when that worker encounters them.”
In general, presence-sensing devices are used to prevent access to equipment in three ways: at the point of operation; around the perimeter of machine; or across an area.
LIGHT SOURCES
Light curtains, perhaps the most common type of presence-sensing device, consist of a transmitter and receiver. The transmitter unit contains light emitting diodes (LEDs), which send out parallel infrared light beams to a photoelectric receiver. When an opaque object breaks one or more of these beams, the device controller sends a stop signal to the machine.
The set of beams are spaced according to what they need to detect.
“If they are supposed to see a finger, like a finger reaching in, they need to be closer together. If they need to see a person, they can be a little farther apart,” Gordon says.
Light curtains can be used to control access at the point of operation of a machine, such as a brake press. They may also be used to protect the perimeter around a hazardous machine or access to a specified area, such as the doorway into an enclosed area protecting a robotic cell.
Programmable features such as “muting” and “blanking” provide a means of adapting the light curtain to production needs. Muting refers to the temporary, complete disabling of a light curtain’s sensing field or stop signal to the machine during the non-hazardous portion of a cycle. This is often done, for example, during the entry or exit of pallets on a palletizing machine. Blanking occurs when one or more sections of the light curtain’s sensing field are disabled. The rest of the light curtain remains active. In one common use, a small gap in a light curtain is blanked to allow the feeding of material through it to a punch press.
Another safety device that uses a light source is the laser scanner, generally used to detect presence across larger areas. A scanner sends a laser beam across a floor area and when the beam is broken, it realizes something is in the area and can shut down a machine. Scanners can be customized and can have two programmable zones (warning and safety).
“Light curtains are like an electronic fence,” says Dan Plant, senior technologist at Cornwall, Ont.-based EFI, an engineering consulting firm. “Crossing that fence will trigger something. The laser, however, puts out a blanket across a whole area. If you jump anywhere onto the floor, it will still detect that you’re standing in the area.”
Laser scanners are more expensive than light curtains but are more accurate and travel farther than infrared, says Owen Tucker, technical support manager at Barrie, Ont.-based Pilz Automation Safety Canada. Because laser and infrared devices are mounted at floor level or on machinery, they are prone to such problems as forklifts backing into them or machinery vibration.
“Light curtain beams have to be aligned between two sensing devices, so if they go out of alignment, they will turn the equipment off. Being mounted at floor level, they are prone to maintenance. You have to be careful you don’t knock them out of alignment,” Tucker says.
PRESSURE-SENSITIVE
Safety mats are placed in an area where it is unsafe to operate a piece of equipment, such as a stamping machine. The mat detects when someone steps on it in a hazard zone and shuts down the machine.
Some people use mats to detect that an operator is standing in the spot where they are supposed to be — for example, at the operator’s console — and moving off the mat causes the machine to stop. But this is an improper way to use them, Gordon says.
One disadvantage of safety mats is that a person can deceive them into thinking an operator is standing on the mat by putting a heavy weight, such as a tool box, on the pressure sensor. Moreover, due to cost, they are not a realistic solution where the goal is to protect a large area.
Gordon says mats can also present difficulties in manufacturing companies.
“My industry is manufacturing and the struggle people have with safety mats is that there are a lot of forklifts and traffic and people run over them and wreck them. Or there’s a lot of dust and debris, like welding or wood dust, and it gets into them. They need to be installed correctly to make sure there’s a tight seal.”
Pressure-sensitive safety edges are touch-sensitive strips attached to crushing and shearing edges of moving parts, such as machine tables or powered doors. When the edge comes into contact with an object, it senses a change in pressure and sends a signal to stop, start or reverse a motor. Edges are commonly located at automatic gates, machine doors and tables, conveyors and facility doors. There are also pressure-sensitive bars: An operator leans into the bar, the sensor detects the person is too close to a hazard and shuts down the machine.
The main advantage of presence-sensing over physical guards is efficiency, Plant says. For example, an operator loading pieces into a stamping machine and punching out 10 parts per hour can use a light curtain to access one particular spot in the machine. This is much more efficient than having to remove the guard each time a piece has to go into the machine.
“Or if a forklift has to come in and remove a full pallet and put in an empty one,” Plant adds, “you can have a presence-sensing device shut down just the zone where the fork truck is and let the rest of the machine keep running. That’s a definite advantage to not having to remove guarding.”
Moreover, Plant says, while it is hard to deceive most presence-sensing devices, a worker can remove a physical guard and leave it off permanently. There is also less need to deceive a presence-sensing device. If there’s a guard in the way, the worker may want to remove it. But if the light curtain can be programmed to meet production needs, there’s no need to shut the machine off, so there’s less likelihood anyone will want to deceive the safety device.
The main downside of presence-sensing devices, Plant says, is that they do not protect a worker from something coming out of a machine. If a hose breaks and sprays someone or a part is ejected out of the machine, a light curtain will not stop it flying through the beam. If you have a machine that’s stamping out parts and that part could be ejected at the worker, then a light curtain is not feasible because the worker could get hurt.
Another disadvantage is that presence-detecting devices don’t actually prevent a person accessing the hazardous zone. They rely on there being enough time for the device to shut down the machine before a worker reaches it. A worker who puts a hand through a light curtain or walks into an area covered by a laser scanner and who reaches the hazardous part faster than the machine can shut down may be injured.
“But when you have a physical guard on a machine, the worker can’t get through it until they take the guard off. And if the guard is installed properly, the worker can’t get it off without specialty tools. There’s a lot more involved in getting into a machine,” Plant says.
NEW TECHNOLOGIES
One new technology is the hand detection sensor, installed at the point of operation. A sensor is mounted in the corner of an opening and reflective tape is mounted along the inside frame, creating a safety window. The device, which can sometimes be used instead of light curtains, is designed for smaller areas. Unlike light curtains, it aligns automatically and can be used in openings of various shapes.
Another new presence-sensing technology is the camera vision system. Cameras are installed at roof or ceiling height, looking down on the work space. Sensors detect any intrusion, whether it’s a person walking into an area or a hand or arm reaching into a danger zone. They can be programmed according to zones, providing the intruding worker with warning before the machine shuts down completely.
“There are two zones on a camera system. If anyone comes into the first zone, the machinery would slow down, but not stop. That sends a warning to the person that they’re encroaching too close to the dangerous area. If they go further, then it would emergency-stop the equipment or stop it all together. That’s what the cameras are looking for,” Tucker says.
Cameras systems, which are more expensive than other presence-sensing devices, replace other structural guarding systems. The safety manager programs exactly which areas are danger zones and which are safe. That ability to define hazardous areas more specifically can increase usable area and reduce production stoppages.
“You can program the cameras according to how fast the movement of the machinery is and how fast a person could approach that area. That defines the danger zones,” says Andreas Sobotta, CEO and general manager at Pilz Automation Safety Canada. “You have more freedom to program the safety area. You can have a forklift go in and out without stopping the process. That can all be programmed.”
The installation of presence-sensing devices should start with a risk assessment, Gordon says. “That way you have a clear understanding of the process, how close the operators need to get and what stopping time you need to have. If someone breaks a zone, how quickly will the machine stop? Where does the device need to be placed so that a person can’t receive a residual hazard?”
Safety managers should refer to CSA Z432-16 Safeguarding of Machinery and, if applicable, CSA Z142-10 Code for Power Press Operation. CSA Z432-16 outlines a comprehensive risk analysis procedure, as well as design and operation requirements. Engineers use a formula to calculate minimum allowable safe distances.
Plant says it’s very important for workers to be trained by their employer on the limitations of presence-sensing devices. Workers should know how the sensors work, when the device is not functioning properly and what to do if a malfunction occurs.
“A worker needs to be trained by the employer on: What is the sensor for? What are we trying to prevent? And how do I work safely around it?”
With presence-sensing devices, workers must follow certain work practices. For example, where a light curtain is muted or blanked for a production run, operators should be trained to check the device to ensure it has been properly adjusted before starting a new task. This was not done in the case of the operator who was injured using a power press brake.
Most critically, Gordon says, workers must be fully aware of the hazards the devices are protecting them from. They may have a false sense of security if, during training, they are told the light curtain will stop if they reach their hand in.
“So I start reaching closer and closer and the machine is stopping every time. But I’m counting on it being designed correctly: If I reach into an area the machine is going to stop,” Gordon says. “Workers need to be told, ‘This thing is protecting you from something that can cut your fingers off.’ Not to be scared of it, but to have a clear understanding not only of the safeguard but also of what it is protecting them from.”
Linda Johnson is a freelance journalist based in Toronto. She can be reached at [email protected].
SIDEBAR
4 limitations when selecting presence-sensing devices
1. Presence-sensing devices alone may not provide sufficient safeguarding. Additional barrier guarding may be required to protect workers other than the operator.
2. Presence-sensing devices must never be used to safeguard a machine with a full-revolution clutch.
3. No attempt should be made to install a presence-sensing device until the requirements of the relevant standards have been reviewed.
4. Presence-sensing devices are to be used during normal production only. They are not a substitute for lockout.
Source: WorkSafeBC