CEO tells COS that most organizations collect so much information they don't know what to do with it, while 68 per cent of business data remains unused
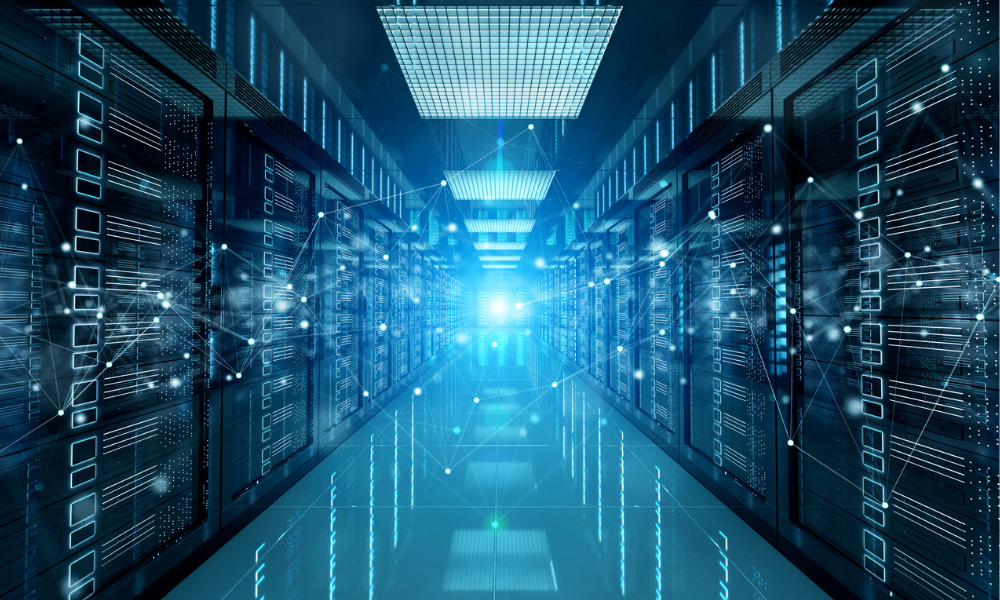
Data, and analysing data, are a key way for organizations to keep track of employee health and safety.
But 68 per cent of business data remains unused, and businesses that do use their data perform 65 per cent better than their peers (McKinsey, 2021).
So where are organizations going wrong?
“I don't think organizations are doing anything particularly wrong when it comes to tracking data. I think the challenge that most organizations have is they collect so much data, they just don't know what to do with it,” says Tyler Davey, CEO – North America, Alcumus.
Alcumus is a provider of technology-led risk management solutions and has recently launched its enhanced version of their Safety Intelligence tool, which allows businesses and organizations to utilize their data to improve their safety program.
Collecting data
Companies are spending a lot of time collecting data, but the data is not necessarily being adequately stored. It is scattered throughout various Excel files or documents on work computers or personal laptops. This means that the data is not easily accessible, preventing organizations from getting real time access to their data, says Davey.
This is a problem, because it also increases the amount of work an employee has to do trying to uncover that data to the tune of around 230 hours per employee per year, says Davey.
“It’s less about collecting more data and more about using the right systems, the right tools, the right process, to be able to get at that data and store it centrally,” he says. “And also to define outcomes on what they want to use that data for.”
Optimizing outcomes
Organizations need to know what to look for. For example, companies may want to track lagging indicators, leading indicators, safety adoption, tracking compliance from a safety perspective, hazard identification being recorded, etc.
“It all starts with what outcomes you want to garner,” says Davey. “Learn how to filter based on what's most important to your business.”
Part of learning how to better use data is pinpointing which information is actually important for the business and using that to help improve safety concerns within the organization.
Improving safety
Being able to properly use and read data can help improve a company’s safety program.
“A common scenario that we often find is companies making an assumption about what is [a safety hazard] based on one experience that they saw two or three months ago […] this gets burned into their memory, even though it may be one case out of 10,000 where that happened. Whereas something else that happens every day is so common that they ignore it,” says Davey.
Data driven safety can help identify these common issues, solve them and get better results. And it also allows for continual, traceable, improvement.
Nevertheless, safety isn’t a catch-all solution, and this is the same for data – especially for high-risk industries.
“There are a lot of leading indicators that are one-size-fits-all, but it’s important to understand the specific ones that fall under your industry. There is an onus on safety leaders to do the legwork,” says Davey. “Everyone thinks that it’s the same across every single high-risk industry when in fact it may not be.”