How managers can address hazards and maintain safety on construction sites
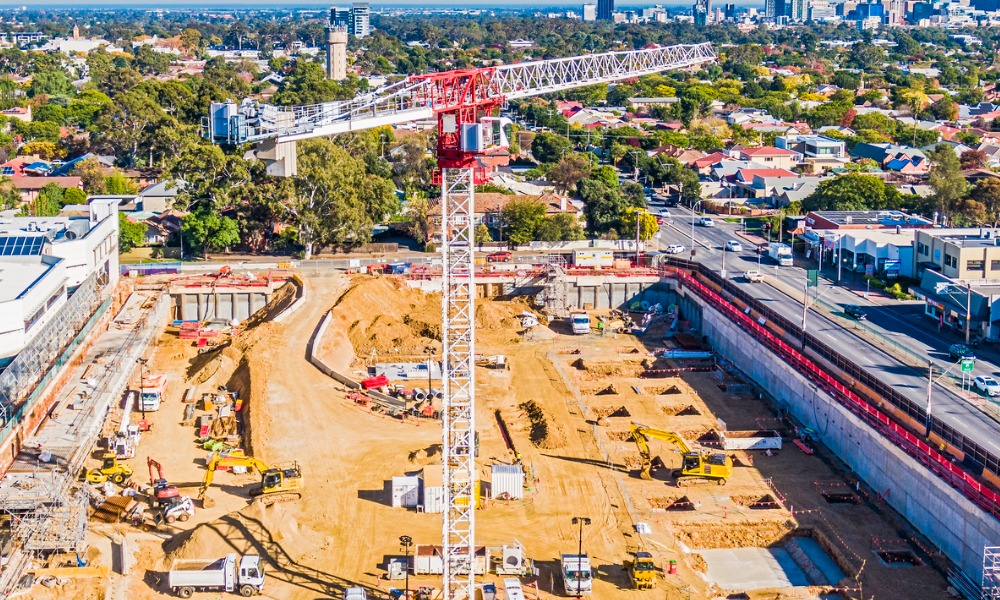
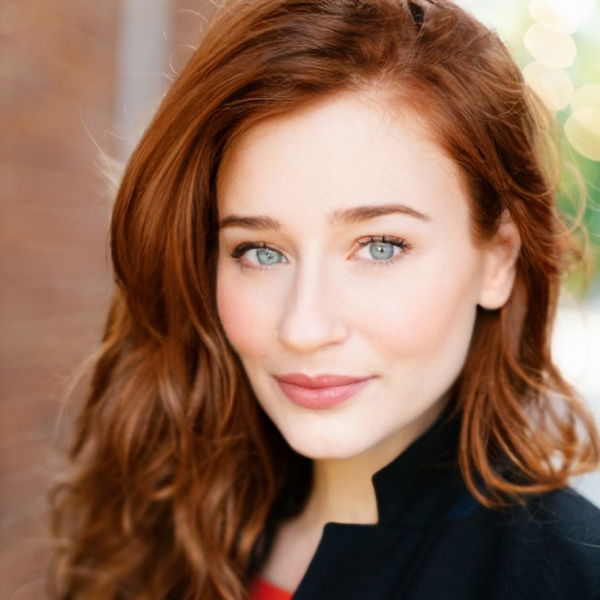
Construction managers have countless responsibilities during any given project, but safety is always the most important one. Everything else is secondary. Protecting your employees from various worksite hazards is a constant task that requires strict protocols, which is easier said than done.
Here’s how construction managers can take effective measures to address the construction industry’s greatest hazards and maintain a safe working environment.
Biggest safety hazards in construction
Understanding your workplace’s hazards is always the first step in creating successful safety protocols. These are the most common causes of occupational illnesses, injuries, and fatalities in Canada’s construction industry:
- Falls from heights: More than 40,000 workers get hurt each year from fall accidents, with construction and warehouse workers being the most likely victims.
- Exposure to harmful substances: Illnesses from chemical and biological substances have caused more workplace deaths in the last ten years than traumatic injuries. Most of these deaths were due to asbestos exposure.
- Struck-by incidents: Construction workers face the constant risk of getting struck by moving equipment, falling objects or unsecured loads.
- Heavy equipment malfunctions: Heavy equipment operators are at risk experiencing mechanical failures and other malfunctions that cause deadly accidents.
- Ergonomics: Common construction movements such as bending, reaching and twisting can cause numerous repetitive stress injuries or musculoskeletal disorders.
- Noise pollution: The noise on a construction site can cause permanent hearing loss and increase worker stress levels, which in turn can lead to an accident.
It’s also worth noting that occupational injuries and deaths are often vastly underreported. Ontario’s Workplace Safety Insurance Board recorded 242 workplace fatalities in 2022, but the Workers Health and Safety Centre estimates that the actual figure is at least ten times higher.
Aside from the life-threatening effects on your employees, these incidents often lead to costly project delays. The entire site must shut down until you properly address the hazard, setting back construction and taking money out of everyone’s pockets.
What can construction managers do?
Construction managers must take a proactive approach to workplace safety rather than waiting for an accident to happen. Here are five key steps to help you develop comprehensive safety procedures and implement them in a timely manner.
-
Conduct thorough risk assessments
First, you need to conduct thorough risk assessments for each worksite. Every construction project has a particular set of hazards, some of which aren’t obvious at first glance. There could be a higher chance of chemical inhalation, electrocution, scaffolding collapse, and many other unique accidents. You must identify all of these risks, no matter how small and insignificant.
Once you identify all the risks, evaluate their level of danger and prioritize them accordingly. Remember to record all your observations during this evaluation process and relay the information to your subordinates. You will likely have to adjust your safety protocols from site to site, so everyone needs to be on the same page.
-
Update your training program
Speaking of being on the same page, you have a responsibility to update employee training programs and keep everyone informed about workplace hazards. The program should include print and video materials demonstrating safe workplace behaviors, first aid instructions and regular emergency response drills.
You will periodically have to revisit your training program when you work in different weather conditions, buy new equipment, or use different materials for a specific project. Frequent updates will ensure that your program addresses avoidable errors, prevents accidents, minimizes equipment downtime, and increases overall productivity.
-
Invest in new analytics tools
As the construction industry goes paperless and becomes fully digital, data analytics software will be the key to monitoring worksite hazards. It can collect massive amounts of data and help you identify all potential hazards on a given worksite. The more data that’s available, the more you can optimize your safety procedures and promote the well-being of your employees.
Other analytics tools such as field tracking and project management software will also help you monitor employee activity. This level of visibility holds them accountable and ensures that they’re following the latest safety protocols.
-
Establish clear lines of communication
Clear communication between managers, supervisors and entry-level employees is crucial for upholding safety standards. You need to implement a mobile incident reporting system so workers can alert you to hazards as soon as possible. You should also hold frequent safety meetings and toolbox talks so everyone can voice their questions and concerns.
Another great way to promote quick communication is by rewarding employees for compliance. Give them incentives to enforce safety regulations such as performance-related bonuses, extra PTO or extra benefits on their health insurance. These rewards will ensure complete buy-in from your workforce and keep everyone in a safety-first state of mind.
Workplace safety never stops
If there’s one lesson you can take from this guide, it’s that workplace safety never stops. It’s an ongoing process that requires constant vigilance and refinement. Your main responsibility as a construction manager is to set an example for your employees and address every hazard with attention to detail.