As we enter the next wave of COVID, how will manufacturers and purchasers know that their PPE meets safety standards
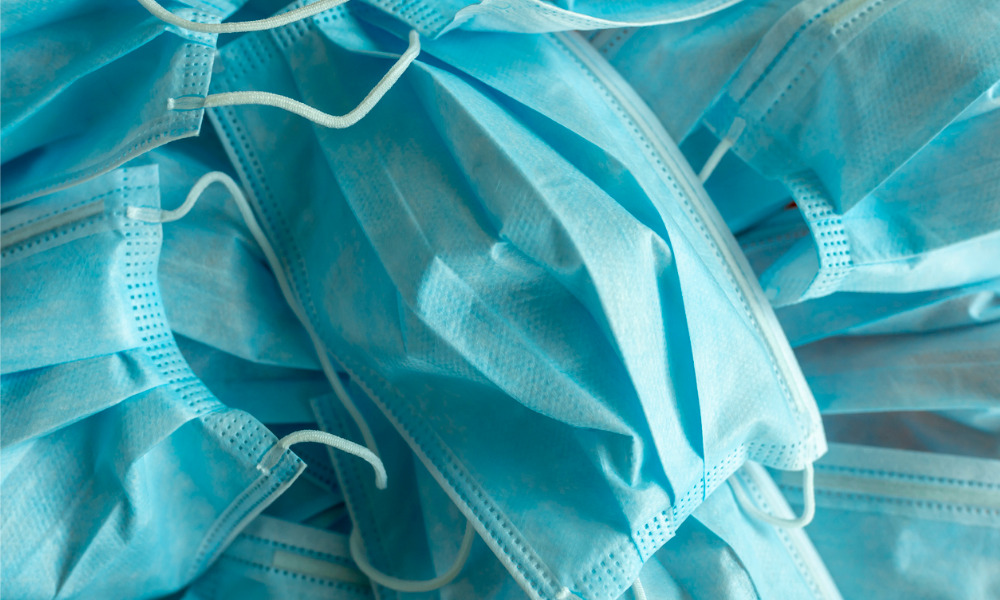
The COVID-19 pandemic has caused a dramatic surge in PPE demand by the healthcare industry worldwide, resulting in persistent global uncertainty about supplies and inventories. Two months into the first wave of the coronavirus pandemic, federal and provincial governments started using extraordinary measures to supply healthcare workers with PPE, including letting them use expired masks just to cope with demand. In March, Ottawa passed an Interim Order that allows masks, face shields and gowns to be imported and sold in Canada even if they do not meet Health Canada's pre-COVID-19 standards.
As of April, Health Canada had ordered over 1.8 billion units of PPE, ranging from masks to gloves to gowns, with much of the supply coming from China lacking any clear means of determining if the product met performance or safety standards. This uncertainty created confusion in the marketplace.1 Also, in April, China's own government revealed it had seized 89 million pieces of poor-quality product, and Canada acknowledged that it received at least one million masks from China that didn't meet its standards since the pandemic began.
Health Canada's Interim Order was prompted by what the agency's website calls an “unprecedented and urgent need for medical devices during the COVID-19 crisis.” That demand has caused critical shortages, it says.
According to Public Services and Procurement Canada’s website, as of September, there are still massive gaps between the quantity of PPE ordered versus the quantities received.2 That means hospital personnel and frontline workers are still operating with shortages of PPE, which puts them at risk of contracting the virus.
As we still have a long way to go before COVID-19 transmission is controlled and eliminated entirely, sourcing of PPE has never been more important. It is needed for frontline workers to continue testing people for the virus, for healthcare providers to continue caring for COVID-19 patients, to keep essential businesses open, protecting first responders and enabling an environment where people can safely return to their normal daily activities.
Domestic need for PPE manufacturing and testing
We now clearly see the need for a domestic PPE industry to develop in Canada and the government has enacted these measures to make this happen:
- ordering in bulk on behalf of provinces and territories;
- supplementing those orders by purchasing everything immediately available that meets requirements;
- ramping up domestic manufacturing capacity, through the Plan to Mobilize Industry to fight COVID-19, being led by Innovation, Science and Economic Development Canada;
- an Interim Order (IO) by Health Canada to fast track medical PPE products getting into Canada; and
- In Ontario, Premier Doug Ford announced a $50-million fund to help businesses retool their operations to produce medical equipment and personal protective gear for front-line workers.3
As a result of all the uncertainty in the market with unknown suppliers, the Ontario government also announced in June of this year that it would provide a grant to locally-based CSA Group Testing & Certification Inc., a subsidiary of the Canadian Standards Association (CSA Group), to increase capacity for testing and certifying personal protective equipment (PPE) that are imported into or manufactured in Canada.
CSA Group has opened a lab in Canada with capacity to both test and certify a range of medical-grade PPE, including masks, surgical gowns, and gloves.
Building confidence in the Canadian supply chain is essential, according to CSA Group President & CEO David Weinstein. “This will build tremendous confidence and trust in the supply chain, making buyer decisions quicker and easier, to shorten the procurement process, and help alleviate medical PPE shortages,” says Weinstein.
While testing has previously been available in limited capacity, the recently introduced certification of PPE offers a visible mark on the product or packaging, indicating the product has been tested and meets the rigorous performance and safety requirements. This certification mark is also augmented by ongoing inspection services to ensure the product continues to be manufactured in alignment with the certification.
Back in March, Canada was buying around 0.2 percent of its PPE from Canadian sources. In September, Innovation Minister Navdeep Bains reported that Canada is now buying almost half of its personal protective equipment from domestic companies, just as the coronavirus’ second wave is hitting much of the country.
As global PPE demand grows, so too will testing & certification
The global healthcare PPE market size was valued at USD 4.7 billion in 2019. Since the outbreak of COVID-19, global demand is now expected to register a GAGR of 8.5% from 2020 to 20274. As new PPE manufacturers enter the market, testing of PPE has never been more important.
What to look for when sourcing medical PPE
Hospital procurement teams, who normally call their pre-vetted and long-time distributors when they need a stock of supplies, are still needing to find new sources.
There are three key things to look for when sourcing reputable medical PPE:
1. Look for a certification mark – A certification mark on the product or packing can help identify a product has been tested and meets the relevant standards. Products with certification marks may be verified on the certified products listing section of the mark’s issuing agency’s website.
2. Get the manufacturer’s name – Without this information, you may not be able to verify that the products you are trying to purchase are indeed real and correctly classified.
3. Request product test reports – All claims from manufacturers should be verified prior to purchase such as bacterial, viral, or particle filtration. (ASTM II certification, CE certification test report, BFE, PFE tests).
4. Ask for photos of the product, the packaging, and shipping boxes – You must be able to see the product and packaging.
CSA Group has over 70 years of experience in certifying PPE products. We provide testing, inspection, and certification services that help PPE manufacturers demonstrate that their products are in compliance with applicable safety, environmental, and operating performance standards. To learn more about CSA Group’s testing and certification services for PPE products, visit here.
Sources:
1 https://www.cbc.ca/news/canada/saskatchewan/ppe-import-china-shortage-1.5552426
2https://www.tpsgc-pwgsc.gc.ca/comm/aic-scr/provisions-supplies-eng.html
3 https://www.cbc.ca/news/politics/trudeau-premiers-call-covid19-supplies-1.5518715
4 https://www.grandviewresearch.com/industry-analysis/healthcare-personal-protective-equipment-ppe-market