Compliance is an issue 'safety professionals struggle with regularly'
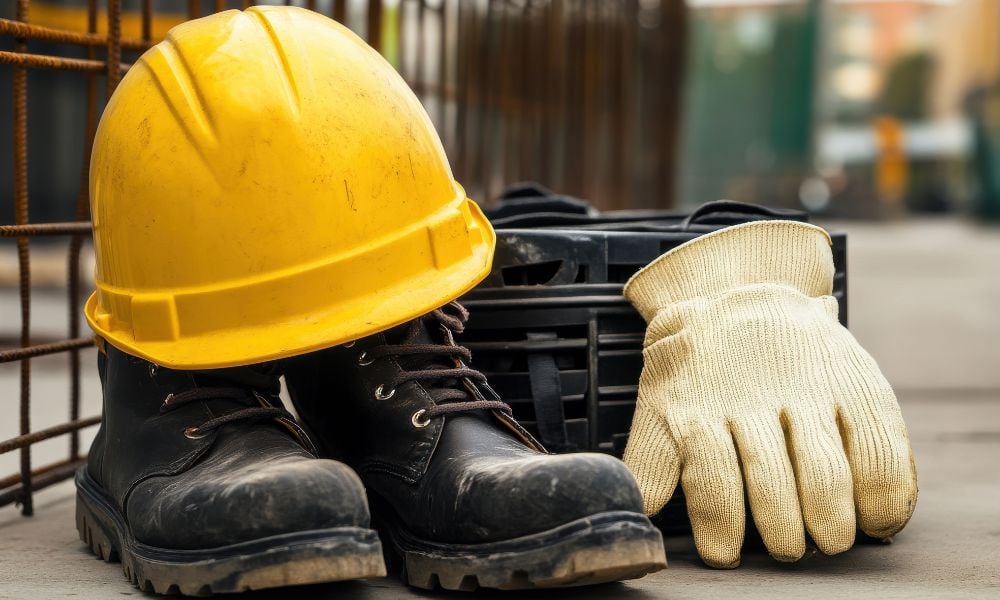
Health and safety professionals across industries continue to struggle with a critical challenge—getting workers to wear personal protective equipment (PPE) consistently and correctly. According to the newly released 2025 PPE Pain Points Study: Top Trends and Challenges, conducted by J. J. Keller & Associates, Inc. and the International Safety Equipment Association (ISEA), compliance remains one of the biggest hurdles in workplace safety, even as PPE program management shows signs of improvement.
Nicole Randall, senior director of marketing and communications at ISEA, emphasizes the importance of worker protection. “One thing that we found that’s a positive is that PPE management is strong,” she says. “We’re happy to see that folks have the time and resources they need to assess their PPE needs. That’s wonderful. Of course, there’s always room for improvement until we see 100% compliance.”
Persistent compliance struggle
Despite progress in PPE management, more than 75% of survey respondents report having difficulty getting employees to wear PPE at least some of the time. Workers cite discomfort, inconvenience, or even aesthetic concerns as reasons for not wearing required gear.
“Safety professionals struggle with this regularly,” Randall explains. “Some workers just don’t think they need it, they don’t like how it feels, they don’t like how it fits, or even how it looks. In some cases, there are cultural issues—workers don’t want to feel like a rookie on the job, so they avoid trying a new type of PPE that might be more protective.”
Employers also grapple with PPE training. Nearly half of respondents struggle to train workers on when PPE is necessary, how to wear it correctly, and its limitations. “There’s no sense in wearing it if you’re not going to wear it correctly,” Randall warns. “If it’s too big, it could fall off. If it’s too small, it won’t provide the protection it’s meant to. Training workers to use PPE properly is still a major challenge.”
Sizing and weather considerations
The study highlights that while PPE sizing issues persist, the industry is making progress—especially for women’s PPE. Nearly one-third of safety professionals still struggle to find properly fitting options, but Randall notes a growing awareness.
“It’s not as much of a challenge as it used to be,” she says. “We’re seeing more education, more reporting, and more industry focus on making sure all body types have PPE that fits—whether someone is shorter, taller, thinner, or has religious or cultural considerations.”
Weather conditions are another evolving factor in PPE selection. While 84% of safety professionals consider weather when purchasing PPE, Randall sees an opportunity for further education. “With record-setting temperatures becoming more common, it’s crucial to ensure PPE is optimized for extreme heat and cold,” she says.
Moving from reactive to proactive safety
One of the most concerning findings in the study is that many companies still rely on injury data to evaluate their PPE programs. Randall urges safety professionals to take a more proactive approach.
“The data shows that analysis often doesn’t occur until after injuries happen,” she explains. “That’s very reactive, and we need safety professionals to be proactive. They need to monitor workers to ensure they’re wearing PPE correctly and educate them on why it’s so important.”
The bottom line, Randall stresses, is that education and awareness must remain a top priority. “We must continue to express to workers how critical PPE is. There are real-life examples of injuries and fatalities due to non-compliance, and we need to ensure workers understand that PPE is there to keep them safe and get them home at the end of the day.”