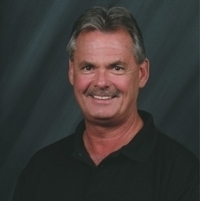
In the second installment of a three-part series aimed at redefining approaches to corporate health and safety, Dennis Ryan discusses the shortcomings of many basic health and safety initiatives and stresses the importance of human factors when striving for safety excellence.
[Click here to read part one of the series.]
You can slice a pie anyway you want, but it doesn’t change anything but the size and the number of pieces.
What does this have to do with safety? Bear with me.
If fatality statistics suggest that health and safety conditions are not showing signs of improvement, then what needs to be done differently? The first step is accepting that current health and safety doctrines don’t always work. For over 50 years, the health and safety profession has had one common message: implement the basic safety elements and safety excellence will be the result.
Many organizations have followed this advice to the letter. Others have taken the basic elements — such as incident/accident reporting and investigations, inspections and hazard identification and assessment — and divided them further into six, eight, 12 or more basic safety elements.
Therein lies the problem. However you slice this safety pie, it doesn’t change anything but the size and number of pieces. The reality is that nothing really changes unless a change is made to the ingredients.
If safety excellence were really contingent upon merely assembling the prescribed safety pieces, many more companies would have achieved the goal of safety excellence by now. Since this is not the case, more and more organizations are starting to question the huge expenditures and tremendous attention the basic safety elements receive.
Those whose livelihood depends on the safety basics binder defend the focus and expenditure of resources, believing this method to be the only way to safety salvation. Stick to the status quo, they encourage, as it is tried and true. The statistical evidence, however, suggests otherwise.
The truth is that there is a great deal more to achieving safety excellence than the basic elements found in the tabulated binder assembled by safety professionals some 50 years ago. Today, the essential content of the binder remains practically unchanged from its original incarnation half a century ago. And therein lies one of the biggest problems. For too long, too many organizations have focused all of their energy and resources on the basic safety elements, only to be disappointed by the lack of safety success.
It’s time to add some important new pages to the basic safety program binder that has guided so many organizations to legislative compliance — and safety mediocrity.
All safety excellence models are similar
Ask the companies that have achieved safety excellence and it’s likely they’ll suggest that the basic safety element guide has omitted, or intentionally excluded, some critical sections.
These additions are not cloaked in secrecy. There are many excellent models that identify additional key determinants of safety excellence. What’s common to these models is that they emphasize human factors as a key element of safety success.
It’s remarkable that these additional factors have been missed in the basics binder, as they really are prerequisites. The truth is, it’s the human factors that determine whether or not the basic safety elements will be successfully implemented and accepted into an organization. If an organization lacks good, strong leadership; if management is not deemed credible; if employee perceptions suggest that management cannot be trusted; or if employees feel the organization doesn’t really care about them, all basic safety element initiatives will be significantly impacted in a negative way.
The importance of human factors in safety excellence is not a new revelation. Many studies have recognized their importance in establishing and maintaining excellent performance. That the safety profession has not more widely recognized and applied these findings to managing health and safety is remarkable.
Companies that have recognized the importance of the relationship between human factors and improved safety performance have been rewarded with safety-excellent programs. Organizational behaviour research seems to suggest that the safety profession has been putting the cart before the horse. The basic safety elements have been placed higher on safety professionals’ priority lists than the framework of human factors that they actually function within.
Safety is simply good business
Is it possible for an organization to achieve safety excellence without even having a health and safety program? At the risk of a public flogging and lynching, I’m going to make a very risky admission. As a health and safety professional who has been in this business for 36 years and has assessed hundreds of company health and safety programs, one of the safest companies I’ve ever worked with did not subscribe to a formal health and safety program – not one basic element.
The company had procedures that incorporated safety, but it did not have safety procedures. It had staff meetings in which safety was discussed, but it did not have safety meetings. Before starting to work, the employees didn’t conduct pre-job safety assessments – they assessed their work from an operational and safety perspective. They conducted inspections on equipment and machinery, but not only for safety.
For this company, safety was simply incorporated into the day-to-day activities of doing business — and excellent, safe service and products are what they provided. Ask the management of any safety-excellent company about their safety success, and they will explain that their success is based more on key human and organizational factors than on basic safety elements.
Safety-excellent companies have determined that the building blocks for safety are not contained in the basic safety element binder as it currently exists. They have come to understand that success in all areas — safety, productivity, service and quality — is dependent on human and cultural factors such as employee satisfaction, positive employee perceptions and attitudes, management credibility, and trust.
It’s no secret that safety-excellent companies also demonstrate excellence in all other aspects of their business. Anything that a safety professional can do to improve on the softer human and cultural factors should be viewed positively by the leadership, because the improvement will affect the entire business. This is why some companies use their safety initiatives as a springboard to improving overall corporate performance.
Viewed in this light, safety activities should be perceived as adding value to an organization as opposed to a drain on resources. If an organization’s goal is only to meet basic safety requirements, it would be wise to implement a safety program comprised of traditional basic safety elements. If the goal is to achieve safety excellence, it should work on the human and/or cultural factors that are the foundation of any successful business.
Part 1: Are we putting the cart before the horse?
Part 3: What needs to be done to change safety culture?
———————
Interested in learning more about what Dennis has to say? Stop by next week to read part three of the feature, where he'll discuss ways that companies can emphasize human factors in their health and safety initiatives and achieve safety excellence.
Dennis Ryan is the president of Compass Health and Safety, an Edmonton-based OHS consulting company. You may contact Dennis via e-mail at [email protected]
[Click here to read part one of the series.]
You can slice a pie anyway you want, but it doesn’t change anything but the size and the number of pieces.
What does this have to do with safety? Bear with me.
If fatality statistics suggest that health and safety conditions are not showing signs of improvement, then what needs to be done differently? The first step is accepting that current health and safety doctrines don’t always work. For over 50 years, the health and safety profession has had one common message: implement the basic safety elements and safety excellence will be the result.
Many organizations have followed this advice to the letter. Others have taken the basic elements — such as incident/accident reporting and investigations, inspections and hazard identification and assessment — and divided them further into six, eight, 12 or more basic safety elements.
Therein lies the problem. However you slice this safety pie, it doesn’t change anything but the size and number of pieces. The reality is that nothing really changes unless a change is made to the ingredients.
If safety excellence were really contingent upon merely assembling the prescribed safety pieces, many more companies would have achieved the goal of safety excellence by now. Since this is not the case, more and more organizations are starting to question the huge expenditures and tremendous attention the basic safety elements receive.
Those whose livelihood depends on the safety basics binder defend the focus and expenditure of resources, believing this method to be the only way to safety salvation. Stick to the status quo, they encourage, as it is tried and true. The statistical evidence, however, suggests otherwise.
The truth is that there is a great deal more to achieving safety excellence than the basic elements found in the tabulated binder assembled by safety professionals some 50 years ago. Today, the essential content of the binder remains practically unchanged from its original incarnation half a century ago. And therein lies one of the biggest problems. For too long, too many organizations have focused all of their energy and resources on the basic safety elements, only to be disappointed by the lack of safety success.
It’s time to add some important new pages to the basic safety program binder that has guided so many organizations to legislative compliance — and safety mediocrity.
All safety excellence models are similar
Ask the companies that have achieved safety excellence and it’s likely they’ll suggest that the basic safety element guide has omitted, or intentionally excluded, some critical sections.
These additions are not cloaked in secrecy. There are many excellent models that identify additional key determinants of safety excellence. What’s common to these models is that they emphasize human factors as a key element of safety success.
It’s remarkable that these additional factors have been missed in the basics binder, as they really are prerequisites. The truth is, it’s the human factors that determine whether or not the basic safety elements will be successfully implemented and accepted into an organization. If an organization lacks good, strong leadership; if management is not deemed credible; if employee perceptions suggest that management cannot be trusted; or if employees feel the organization doesn’t really care about them, all basic safety element initiatives will be significantly impacted in a negative way.
The importance of human factors in safety excellence is not a new revelation. Many studies have recognized their importance in establishing and maintaining excellent performance. That the safety profession has not more widely recognized and applied these findings to managing health and safety is remarkable.
Companies that have recognized the importance of the relationship between human factors and improved safety performance have been rewarded with safety-excellent programs. Organizational behaviour research seems to suggest that the safety profession has been putting the cart before the horse. The basic safety elements have been placed higher on safety professionals’ priority lists than the framework of human factors that they actually function within.
Safety is simply good business
Is it possible for an organization to achieve safety excellence without even having a health and safety program? At the risk of a public flogging and lynching, I’m going to make a very risky admission. As a health and safety professional who has been in this business for 36 years and has assessed hundreds of company health and safety programs, one of the safest companies I’ve ever worked with did not subscribe to a formal health and safety program – not one basic element.
The company had procedures that incorporated safety, but it did not have safety procedures. It had staff meetings in which safety was discussed, but it did not have safety meetings. Before starting to work, the employees didn’t conduct pre-job safety assessments – they assessed their work from an operational and safety perspective. They conducted inspections on equipment and machinery, but not only for safety.
For this company, safety was simply incorporated into the day-to-day activities of doing business — and excellent, safe service and products are what they provided. Ask the management of any safety-excellent company about their safety success, and they will explain that their success is based more on key human and organizational factors than on basic safety elements.
Safety-excellent companies have determined that the building blocks for safety are not contained in the basic safety element binder as it currently exists. They have come to understand that success in all areas — safety, productivity, service and quality — is dependent on human and cultural factors such as employee satisfaction, positive employee perceptions and attitudes, management credibility, and trust.
It’s no secret that safety-excellent companies also demonstrate excellence in all other aspects of their business. Anything that a safety professional can do to improve on the softer human and cultural factors should be viewed positively by the leadership, because the improvement will affect the entire business. This is why some companies use their safety initiatives as a springboard to improving overall corporate performance.
Viewed in this light, safety activities should be perceived as adding value to an organization as opposed to a drain on resources. If an organization’s goal is only to meet basic safety requirements, it would be wise to implement a safety program comprised of traditional basic safety elements. If the goal is to achieve safety excellence, it should work on the human and/or cultural factors that are the foundation of any successful business.
Part 1: Are we putting the cart before the horse?
Part 3: What needs to be done to change safety culture?
———————
Interested in learning more about what Dennis has to say? Stop by next week to read part three of the feature, where he'll discuss ways that companies can emphasize human factors in their health and safety initiatives and achieve safety excellence.
Dennis Ryan is the president of Compass Health and Safety, an Edmonton-based OHS consulting company. You may contact Dennis via e-mail at [email protected]