Totten Mine rescue has brought safety concerns to the fore, says former mine worker
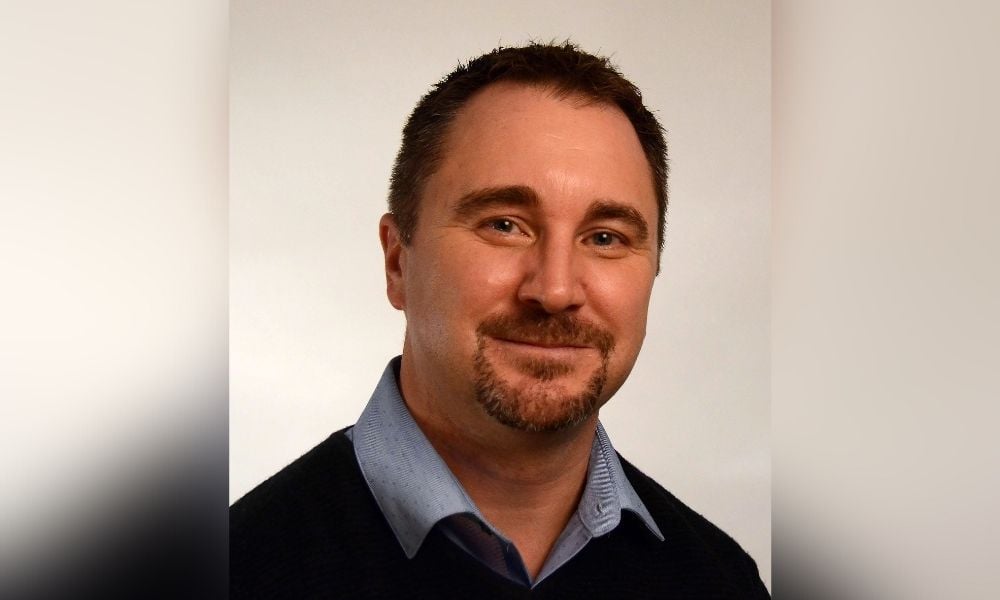
The Totten Mine rescue – which is currently under investigation by the Ontario Ministry of Labour, Training and Skills Development (MLTSD) – has brought mining safety to the fore.
While there are a number of key aspects to mining safety, one of those is an effective rescue plan. “Unlike a home that has many windows and doors you can leave from, a mine usually only has two or three means of egress,” says Mike Parent, VP of Prevention Services at Workplace Safety North (WSN), the Ontario health and safety association serving the mining sector,
Parent, who previously worked as an underground miner, says that there are a number of things that can go wrong in a mine.
In the case of the Vale mine last week, it was the main access shaft that got blocked. But there are a number of other hazards. For example, they may be diesel powered mobile equipment that can catch on fire or unstable sections of rock that fall unexpectedly.
Mining has historically been perceived as one of the more dangerous occupations in Canada, not due to employer negligence but because the environment itself can be a hazardous one. As such, mining has been at the forefront of occupational health and safety advances for decades.
This is why risk assessment is a big deal, and mines are usually well prepared for emergency planning and hazardous scenarios.
Parent is a strong proponent of “bow tie” risk assessment, a process which allows to identify and analyse causal relationships in risk scenarios, and identify where new or updated controls may be implement.
“I can’t think of a more powerful tool in emergency planning,” says Parent.
And while it would certainly be useful, there is no one-size-fits-all rescue plan because each mine has its own inherent set of hazards. The plan will depend on the nature of the emergency, and the activities that the mine is engaging in and even the geography of the mine itself.
Furthermore, mines in more remote locations entail additional risks which need to be included in emergency planning.
Employee engagement
Workplaces that have a strong safety culture, and a culture where workers are engaged and consulted with on risk assessment and controls management, will have an effective rescue plan.
“Foundationally,” says Parent, “employers should be compliant to the laws of the land.”
Ensuring worker health and safety goes through a strong push in risk assessment as well as implementing controls and ensuring that they are effective.
Continuous assessment is always a must – gaps occur when there is a change in process or in equipment. Hazards can arise if those gaps are not considered and dealt with.
And Parent also highlights how important it is to engage the workforce in a proactive way rather than a prescriptive way – prefer talking about ‘controls’ rather than ‘rules’ for example.
Safety is only enhanced when employers engage with their workers about why certain processes are essential.
And while training employees is essential, training itself is not a control.
“The control is the effectiveness of that training,” says Parent.
It all boils down to risk assessment, and employee engagement.
COVID-19 has certainly had a huge impact, not just on mining health and safety but OHS in general.
The pandemic “put the ‘health’ in health and safety,” says Parent – a silver lining that many safety professionals have pointed out.
On the flipside, he says, it has been cause for concern for a number of reasons.
Organizations only have a finite number of resources dedicated to supporting health and safety issues.
Safety officers have had to dedicate some of these resources toward focus, but the shift in focus has created potential risks in that fewer resources can distract from other health and safety concerns.
“We have to keep all of the plates spinning,” says Parent.
Occupational dangers
In 2014, Ontario went through a mine review. The province worked with labour groups, industry groups and some governmental agencies to review health and safety in mines.
They conducted a risk assessment (an essential, as we have seen) to determine all the known risks in underground hard rock mining.
In underground mining (far more prevalent in Canada than open pit mining), the process came up with a top ten of most pressing risks in the sector: ground control, mobile equipment and pedestrians, occupational disease, fatigue, training (or lack thereof), ventilation, locking and guarding, mine services installation, water management and hoisting (i.e. using conveyance to bring persons and equipment up and down the mine).
Since the review, there has been a lot of work done on a number of fronts to reduce the risk in a number of these hazards.
Nevertheless, miners still face risks, most notably musculoskeletal disorders (MSDs) due to the nature of the work (e.g. uneven surfaces, using heavy equipment, etc.), hearing loss and occupational disease such as cancers due to exposure to asbestos, silica or diesel emissions. These can be harder to treat as occupational diseases are often latent, and are diagnosed years down the line.