The safety manager of Exterran Canada has worked in safety for two decades
This year's search for the 2008 COS Safety Leader of the Year took us to Calgary, where one safety manager is making a huge difference in workers' safety.
Peter Hollett's people approach has won the support of Exterran Canada workers - and their vote.
He may be a Harley Davidson Fat Boy-riding dude, but Peter Hollett never lets his style interfere with safety.
Hollett is this year’s recipient of the COS Safety Leader of the Year Award. As safety manager for Calgary-based Exterran Canada, maker of gas compression and total solutions for the oil and gas industry, Hollett oversees the OHS program for the firm’s manufacturing group.
Hollett has been with Exterran for the last four years, but his work in the occupational health and safety field spans over two decades, starting out as a safety committee member at a steel company in Calgary in 1981. Hollett still recalls his first involvement in safety. “My boss asked me if I would get involved because…I was in the yard in a crane and they needed some representation for the first-aid group.”
A journeyman crane operator then, Hollett saw everything that went on in the yard from his glass box. “That was really a motivating factor,” he says. “I’ve seen a lot of injuries up from the crane…that I thought I should become involved in the solution to try to make workplaces safer.”
When the steel company he was working for closed in 1994, Hollett decided to expand his safety training. Four years later, he received his occupational health and safety certificate from the University of Alberta, marking the start of a fulfilling career as a safety professional.
From underground
Colleagues attest to Hollett’s successful role in positively transforming the safety culture at Exterran, as shown by the number of nominations COS received on his behalf. Hollett does not see himself as a management figure, but rather a change agent who facilitates the creation of a safe and open workplace.
The journey towards that goal, however, has not been easy. From day one at Exterran, Hollett knew the company needed an overhaul of its safety culture, which was then driven “underground” as employees were generally afraid to speak up about their safety for fear of repercussion.
“One of the things that was made clear to me was that one of my jobs as a change agent was to bring safety up on the table — above board,” he says.
Getting employees to trust the newcomer wasn’t easy and Hollett understood why the workers were hesitant — the previous management focused too much on punishment and discipline, creating an atmosphere of fear rather than honest and open communications.
“It really took a lot of hard effort and work to get them to trust somebody when it comes to safety…so I had to build a whole new level of trust and bring that safety program out from underground,” says Hollett.
It took Hollett a few months to get employees to finally start opening up and talking about safety issues. Hollett says the key to gaining their trust is communication.
“During safety meetings I communicated to them that...I am a change agent and I’m going to change management and I am going to change the workforce. I made it clear to them that my goal was to work for them and for them to have success.”
(Next: Celebrating successes)
One of Hollett’s objectives was to get employees to actively participate in shaping the company’s safety culture. And sometimes a nod of approval or recognition of a safe act goes a long way with workers.
Hollett established a rewarding scheme that acknowledges workers for working safely. Recognition is based on peer recommendations: one worker witnessing another’s safe deed and telling everyone about it.
“Someone will come to me and say, ‘I’ve seen this guy doing something safe.’ That’s good enough for me. I’d bring that guy in my office, shake his hand and give him a reward,” says Hollett. The reward ranges from $50 to $70 prizes.
Safety meetings at Exterran are also marked with recognition of employees who care enough to step up and point out a safety issue that needs to be addressed. That’s something employees weren’t used to doing in the past, Hollett says.
“It was really difficult to get them to report near-miss incidents, but I would reward them for reporting near-miss incidents no matter how severe it was,” Hollett says.
Recognition is only one part of getting employees’ involvement in safety. Hollett believes the company needs to show employees that workplace safety is a top priority that equals productivity.
He relates a previous near-miss incident that led to one expensive but worthwhile plant shutdown. “We shut the whole shop down and brought everybody into a meeting.” That meeting became a discussion of the incident and exchange of ideas on how to resolve the issue to prevent a recurrence.
The cost to the company of that shutdown was later calculated at $7,700 per hour. The employees were impressed, says Hollett, acknowledging that management support was essential.
“A lot of companies aren’t willing to stop production when it comes to safety, but I like to teach that safety is equal to production. If you make a safe product — a safe, quality product — then production continues,” he explains. “But if you have bumps and hiccups on the road every time there’s an accident, then it’s going to interfere with production. Safety can interfere with production if you have too many accidents.”
Hollett says safety at Exterran has improved by about 85 percent in the last four years.
“We have developed a culture where employees expect to go home safely everyday. That’s an expectation now,” he says.
Most companies have “safety first” as the centrepiece for their safety initiatives, but Hollett prefers a different slogan: Prevention is cure — and education and training are keys to prevention. “The more they know, the more they’re going to understand the process.”
Workers’ involvement in designing safety programs is also an important facet of Exterran’s workplace environment, says Hollett.
Today, Exterran workers are proactive about working safely and following safety processes and procedures because they feel a sense of ownership of the company’s entire safety program.
“If you allow the workers themselves to help explain what needs to be in the process and procedure, then they own it. They say, ‘I came up with the decision, not my foreman told me to do it this way.’ It’s so easy then to sell it to another worker,” he says.
Looking to the future
Hollett hopes to go back to school and get either a Masters Degree in safety or a Certified Safety Professional certification, which is the U.S. designation for safety practitioners. He wants to expand his contribution to safety by teaching.
Hollet started to dip his toe into international teaching when he was asked by his company early this year to travel to Exterran’s facility in Dubai, where he spent over a month teaching and developing safety programs for its workers.
“I just love teaching and instructing and mentoring. I would like to start going to our other facilities...and teach and develop programs and come up with ideas to get people on board,” says Hollett.
At 50, Hollett still wants to continue to make a difference in the world in the way he knows how — keeping workers safe.
Despite the seriousness of many workplace safety issues, Hollett believes people learn more effectively with a dash of humour. So don’t be surprised when your next safety trainer knocks on your door wearing a bee costume chanting “Bee safe!”
That’s just Hollett, buzzing around with his safety message.
Peter Hollett's people approach has won the support of Exterran Canada workers - and their vote.
He may be a Harley Davidson Fat Boy-riding dude, but Peter Hollett never lets his style interfere with safety.
Hollett is this year’s recipient of the COS Safety Leader of the Year Award. As safety manager for Calgary-based Exterran Canada, maker of gas compression and total solutions for the oil and gas industry, Hollett oversees the OHS program for the firm’s manufacturing group.
Hollett has been with Exterran for the last four years, but his work in the occupational health and safety field spans over two decades, starting out as a safety committee member at a steel company in Calgary in 1981. Hollett still recalls his first involvement in safety. “My boss asked me if I would get involved because…I was in the yard in a crane and they needed some representation for the first-aid group.”
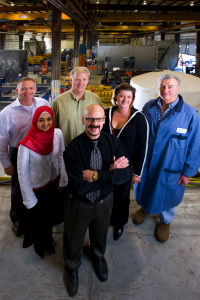
When the steel company he was working for closed in 1994, Hollett decided to expand his safety training. Four years later, he received his occupational health and safety certificate from the University of Alberta, marking the start of a fulfilling career as a safety professional.
From underground
Colleagues attest to Hollett’s successful role in positively transforming the safety culture at Exterran, as shown by the number of nominations COS received on his behalf. Hollett does not see himself as a management figure, but rather a change agent who facilitates the creation of a safe and open workplace.
The journey towards that goal, however, has not been easy. From day one at Exterran, Hollett knew the company needed an overhaul of its safety culture, which was then driven “underground” as employees were generally afraid to speak up about their safety for fear of repercussion.
“One of the things that was made clear to me was that one of my jobs as a change agent was to bring safety up on the table — above board,” he says.
Getting employees to trust the newcomer wasn’t easy and Hollett understood why the workers were hesitant — the previous management focused too much on punishment and discipline, creating an atmosphere of fear rather than honest and open communications.
“It really took a lot of hard effort and work to get them to trust somebody when it comes to safety…so I had to build a whole new level of trust and bring that safety program out from underground,” says Hollett.
It took Hollett a few months to get employees to finally start opening up and talking about safety issues. Hollett says the key to gaining their trust is communication.
“During safety meetings I communicated to them that...I am a change agent and I’m going to change management and I am going to change the workforce. I made it clear to them that my goal was to work for them and for them to have success.”
(Next: Celebrating successes)
Celebrate successes
One of Hollett’s objectives was to get employees to actively participate in shaping the company’s safety culture. And sometimes a nod of approval or recognition of a safe act goes a long way with workers.
Hollett established a rewarding scheme that acknowledges workers for working safely. Recognition is based on peer recommendations: one worker witnessing another’s safe deed and telling everyone about it.
“Someone will come to me and say, ‘I’ve seen this guy doing something safe.’ That’s good enough for me. I’d bring that guy in my office, shake his hand and give him a reward,” says Hollett. The reward ranges from $50 to $70 prizes.
Safety meetings at Exterran are also marked with recognition of employees who care enough to step up and point out a safety issue that needs to be addressed. That’s something employees weren’t used to doing in the past, Hollett says.
“It was really difficult to get them to report near-miss incidents, but I would reward them for reporting near-miss incidents no matter how severe it was,” Hollett says.
Recognition is only one part of getting employees’ involvement in safety. Hollett believes the company needs to show employees that workplace safety is a top priority that equals productivity.
He relates a previous near-miss incident that led to one expensive but worthwhile plant shutdown. “We shut the whole shop down and brought everybody into a meeting.” That meeting became a discussion of the incident and exchange of ideas on how to resolve the issue to prevent a recurrence.
The cost to the company of that shutdown was later calculated at $7,700 per hour. The employees were impressed, says Hollett, acknowledging that management support was essential.
“A lot of companies aren’t willing to stop production when it comes to safety, but I like to teach that safety is equal to production. If you make a safe product — a safe, quality product — then production continues,” he explains. “But if you have bumps and hiccups on the road every time there’s an accident, then it’s going to interfere with production. Safety can interfere with production if you have too many accidents.”
Hollett says safety at Exterran has improved by about 85 percent in the last four years.
“We have developed a culture where employees expect to go home safely everyday. That’s an expectation now,” he says.
Most companies have “safety first” as the centrepiece for their safety initiatives, but Hollett prefers a different slogan: Prevention is cure — and education and training are keys to prevention. “The more they know, the more they’re going to understand the process.”
Workers’ involvement in designing safety programs is also an important facet of Exterran’s workplace environment, says Hollett.
Today, Exterran workers are proactive about working safely and following safety processes and procedures because they feel a sense of ownership of the company’s entire safety program.
“If you allow the workers themselves to help explain what needs to be in the process and procedure, then they own it. They say, ‘I came up with the decision, not my foreman told me to do it this way.’ It’s so easy then to sell it to another worker,” he says.
Looking to the future
Hollett hopes to go back to school and get either a Masters Degree in safety or a Certified Safety Professional certification, which is the U.S. designation for safety practitioners. He wants to expand his contribution to safety by teaching.
Hollet started to dip his toe into international teaching when he was asked by his company early this year to travel to Exterran’s facility in Dubai, where he spent over a month teaching and developing safety programs for its workers.
“I just love teaching and instructing and mentoring. I would like to start going to our other facilities...and teach and develop programs and come up with ideas to get people on board,” says Hollett.
At 50, Hollett still wants to continue to make a difference in the world in the way he knows how — keeping workers safe.
Despite the seriousness of many workplace safety issues, Hollett believes people learn more effectively with a dash of humour. So don’t be surprised when your next safety trainer knocks on your door wearing a bee costume chanting “Bee safe!”
That’s just Hollett, buzzing around with his safety message.