Cause of explosion still 'uncertain,' says government
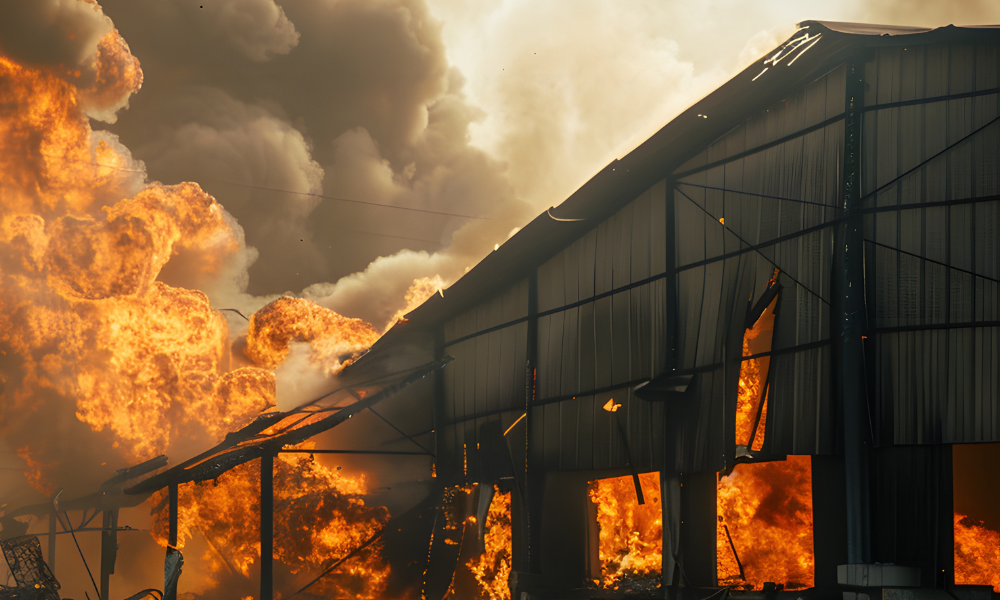
Ontario employer Siltech Corporation has been fined $90,000 after one worker died and another was injured in a workplace explosion.
The incident occurred on Sept. 8, 2021, at the company’s manufacturing facility located at 225 Wicksteed Avenue in Toronto.
Two workers were transferring flammable liquid from a large container into two smaller metal pails. While they were filling the second pail, an explosion occurred, injuring one of the workers and fatally injuring the other.
A Ministry of Labour, Immigration, Training and Skills Development investigation found that the workers had used a plastic hand pump to transfer the liquid. Plastic cannot be bonded or grounded. The investigation found that the metal pails were also not grounded or bonded to the other equipment in the setup.
“Though it remains unproven that the cause of the explosion was static electricity, Siltech Corporation still failed, as an employer, to ensure the pails and pump were bonded and grounded as required by as required by section 22(4)(b) of Ontario regulation 851, contrary to section 25(1)(c) of the Occupational Health and Safety Act,” said the Ontario government.
How can we prevent hazards in the workplace?
According to the Canadian Centre for Occupational Health and Safety (CCOHS), the employer has a duty of due diligence and is responsible for taking all reasonable precautions, under the particular circumstances, to prevent injuries or incidents in the workplace “in all cases”.
“Some hazards and their controls will be specifically outlined in legislation,” it said. “In situations where there is not a clear way to control a hazard, or if legislation does not impose a limit or guideline, you should seek guidance from occupational health professionals such as an occupational hygienist, ergonomist, engineer, or safety professional about what is the ‘best practice’ or ‘standard practice’ when working in that situation.”
The main ways to control a hazard include:
- Elimination: remove the hazard from the workplace.
- Substitution: replace the hazard (e.g., hazardous products, machines, etc.) with a less hazardous one.
- Engineering Controls: includes designs or modifications to plants, equipment, ventilation systems, and processes that reduce the source of exposure.
- Administrative Controls: controls that alter how the work is done, including timing of work, policies and other rules, and work practices such as standards and operating procedures (including training, housekeeping, equipment maintenance, and personal hygiene practices).
- Personal Protective Equipment: equipment worn by individuals to reduce exposure, such as contact with chemicals or exposure to noise.