Breaking down the factors to consider when choosing the right PPE
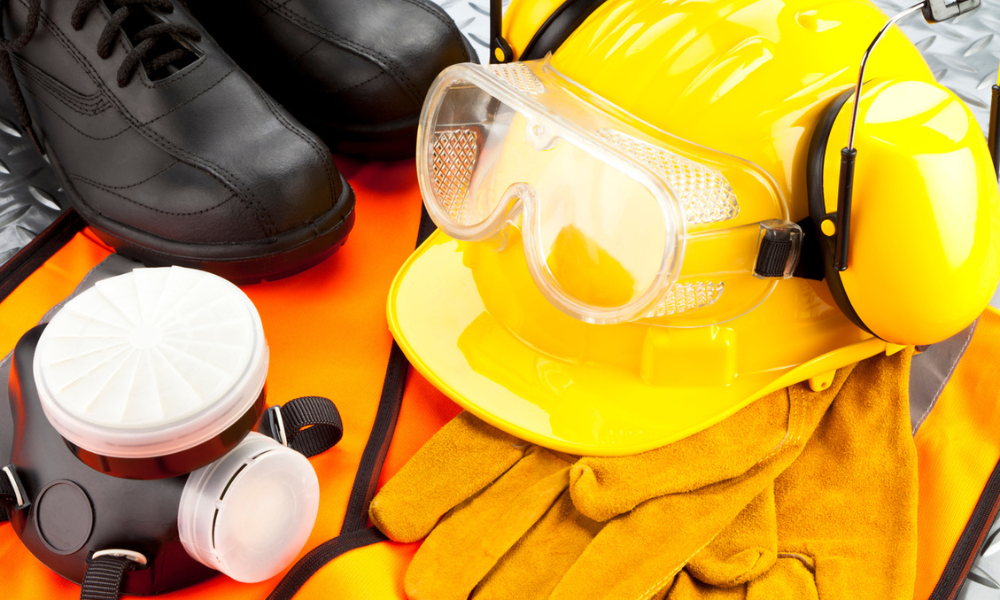
Choosing the right safety equipment is essential to ensuring the safety of workers, especially those who are engaged in dangerous jobs.
“Personal protective equipment must be selected to protect against any hazard that is likely to occur or has a serious injury impact if it does occur,” according to SafetyFirst.
Accidents can happen in any workplace. If a worker is not wearing the appropriate PPE, any untoward incident can be even more harmful to them.
Read more: 3M facing another trial over allegedly defective earplugs
Understanding the importance of the right safety equipment
A construction worker typically wears protective gloves; full face shields when cutting, grinding, or chipping; and chemical splash goggles in their line of work.
If a firefighter responds to a fire incident with this equipment on, they will not be protected from the hazard that they will face.
Similarly, if a construction worker wears the safety gloves, boots, safety goggles and eyewear and respiratory masks typically used by firefighters, they might not be able to perform their job at an optimum level.
Read more: High sulphur content in PPE poses danger for firefighters
Factors to consider when selecting protective equipment
“Not all personal protective equipment (PPE) is created equal. Choosing the right kind of PPE for the job is just as important for work safety as wearing a PPE,” Ann McGlone, formerly market development manager for specialty plastics at Eastman Chemical Company, previously noted in a write-up for COS. “Knowing the different types of PPE materials, their features and limitations can help you make an informed decision about PPE selection.”
So how do you choose the right PPE? Here are factors to consider to find the PPE for the right purpose:
Threat. When choosing the right safety equipment for your workers, the number one consideration must be the threat or hazard that they are facing in their line of work. A PPE, after all, PPE is worn to minimize and mitigate the risks and hazards associated with a wide variety of working conditions.
Read more: Get it right: Tips for choosing the right PPE for the job
“Without proper PPE, workers are left exposed to significant risks of injury or illness,” according to Advanced Consulting and Training Ltd. “These injuries or illnesses may not present themselves immediately either. PPE protects you and your employees from the long-term effects of the nature of your work.”
Comfort. Employers should also take the fit and comfort of PPE into consideration when selecting appropriate items for each employee.
“PPE that fits well and is comfortable to wear will encourage employee use of PPE,” according to Princeton University.
Logically, if workers do not find the PPE comfortable to put on, they will refuse to wear it.
Most protective devices are available in multiple sizes and care should be taken when selecting the proper size for each employee, according to Princeton.
Also, if any employee is refusing to wear PPE due to a sizing problem or comfort reasons, address it with them by acknowledging that you recognize this is a cause of frustration, according to Liz Burton-Hughes in a previous writeup for the Hub.
Read more: Ten essential tips on warehouse safety
“Let them know that you would like their input to solve the problem and get adequate PPE sorted. They’ll appreciate that you respect them and be more inclined to help choose and wear their PPE,” she said.
Material. Employers must also consider the material makeup of PPEs. A recent report noted that a high-performance fabric commonly used in firefighting and other protective garments weakens prematurely when it’s exposed to moisture.
The fabric weakens because of the high sulphur content in some of the fibres, which leads to an accelerated loss in fabric strength when exposed to moisture, it noted.
“As the garment weakens over time, there’s no way to know whether the wearer is still protected or not,” said Saiful Hoque, a researcher in the Faculty of Agricultural, Life & Environmental Sciences at the University of Alberta.
Cost of PPE. Cost is always an issue whenever an employer spends money for the use of workers.
To set upper limits on spending, and to avoid unauthorized purchases, employers can do the following, according to Contego Safety Solutions:
- Set spending budgets per user.
- Choose to trigger email approvals on spends over a specified amount, so that a manager authorizes the spend.
- Opt for a dual-layer approval where two management approvals are needed, when an order exceeds a predetermined budget, or a particular safety item is requested.
- Request further information from the purchaser, so that an order cannot be placed without inputting information such as the employee’s name, or the reason for re-ordering.
Types of PPE
Here are the basic types of PPE out in the market:
- Face and eye protection, like general safety glasses, laser safety glasses, chemical splash goggles and impact goggles.
- Respiratory protection, like dust masks, chemical cartridge respirators, PAPR (powered air purifying respirators) and SCBA (self-contained breathing apparatus).
- Skin and body protection, like laboratory coats, coveralls, vests, jackets, aprons, surgical gowns and full body suits.
- Hearing protection, like foam ear plugs, earmuffs and semi-aural devices.
Ensuring the proper usage of PPEs in the workplace
To ensure that workers properly use PPEs in the workplace, employers must have a PPE program in place.
“A PPE program must be comprehensive,” according to the Canadian Centre for Occupational Health and Safety (CCOHS). “It requires commitment and active participation at the planning, development, and implementation stages from all levels: senior management, supervisors, and workers.”
It added that a good PPE program consists of these essential elements:
- hazard identification and risk assessment
- selection of appropriate controls
- selection of appropriate PPE
- fitting
- education and training
- management support
- maintenance
- auditing of the program
Read next: What personal protective equipment must an employer pay for?