Protect workers' hands from toxic chemicals that can cause burns, illness or death
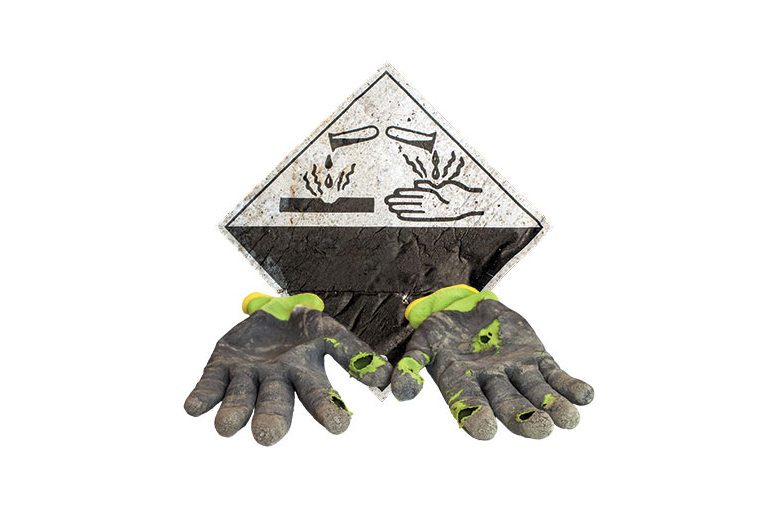
A laboratory worker in the United States was working with trifluoroacetic acid. As she picked up a container of acid to move it, she touched a small amount of residue on the outside of the container. She was not wearing gloves.
Several hours later, the palm of her hand and the inside of her thumb were extremely painful. She had suffered a serious burn and had to undergo skin grafting.
Hazardous chemicals pose serious risk to the skin. They may cause immediate injuries — from irritation to caustic burns — or they can be absorbed through the skin and affect the entire body, causing potentially fatal damage. Selecting the most suitable and effective gloves is a crucial but complex process. While the material used in the manufacture of a glove is perhaps the most important decision, other critical factors must also be considered when selecting chemical resistant gloves.
As with any personal protective equipment (PPE), it is important to start by analyzing the tasks involved, says Tallar Chouljian, occupational health and safety specialist with Hamilton, Ont.-based Canadian Centre for Occupational Health and Safety (CCOHS). Describe the task and identify the chemical types, at the same time noting their concentration, composition (it might be a mixed chemical), temperature and pH and toxicity levels.
One critical factor to identify before selecting gloves is how the chemical is to be handled, she says. Will the worker need protection against only occasional contact with the chemical, against splashes or against total immersion? This will help determine the right length of the glove: should it stop at the wrist or go all the way to the elbow?
The contact period, how long the worker is exposed to the chemical, will also help determine how thick the gloves should be as well as how often they need to be replaced.
The analysis should also identify other requirements that need to be considered during the selection of the gloves, Chouljian says. For example, if the job requires flexibility or touch sensitivity, it’s important to select a material and thickness designed to provide dexterity.
“If the worker has to use fine motor movements with their fingers to do some sort of task and the glove impedes performing the task, it might cause the worker to not want to wear the gloves and avoid that type of PPE. You need to find gloves that not only help protect the worker from the chemical hazard but also allow them to do the task involved,” Chouljian says.
Skin exposure to the glove itself may cause a problem. Workers who are to wear the gloves should be allowed to try on potential selections. For example, someone might be allergic to the type of material that the glove is made of. Latex is much less commonly used in the manufacture of chemical protective gloves today than it once was due to the frequency of latex allergies.
Jeremy Slater, regional sales manager at Thornhill, Ont.-based Acklands-Grainger, says glove selection must include consideration of other, task-specific factors. The gloves, for instance, may also have to provide cut and abrasion protection.
“As soon as the glove is cut or punctured, you’re not protected anymore,” he says.
Material selection may also depend on whether workers are lifting heavy objects or whether the tools and equipment being used require workers to have gloves with a better grip.
In some workplaces, workers are handling equipment that is extremely hot or cold and may need thermal, as well as chemical, protection.
“You could be protecting a worker in the food manufacturing industry, where typically their plants are quite cold. Employees are almost working in a refrigerator. Their hands would freeze if you didn’t keep them warm,” Slater says. “At the same time, you might need a glove for a worker going into an oven to pull out a hot metal rack or who is cleaning with extremely hot water and chemicals.”
When other hazards are present, it may not be possible to select the glove material based on chemical protection alone. Alternatively, the worker may have to wear one kind of glove on top of another. If the hazard is both corrosive and toxic, give priority to protecting against toxicity. While a chemical burn can be treated, the injury cannot be treated once the chemical has been absorbed through the skin into the body.
Finally, make sure the gloves fit properly. Gloves that are too big or small may cause problems. They should be long enough to cover all potentially exposed skin on the wrist and forearm.
Once you have done the job analysis and identified the chemicals, locate each chemical’s chemical abstracts service (CAS) number and safety data sheet (SDS). The SDSs will indicate the potential health effects of each chemical and the type of glove best suited to it.
For more information, a safety manager can refer to the National Institute for Occupational Safety and Health (NIOSH)’s Recommendation for Chemical Protective Clothing database, says Bruce MacKinnon, an instructor in the occupational health and safety certificate program at the University of Western Ontario in London. The chart allows the user to search by chemical and indicates which materials are recommended based on the length of time it takes the chemical to penetrate the material. Individual manufacturers and distributors also publish such glove selection guides.
These charts provide chemical resistance data of various materials that have been tested based on ASTM test standards. Materials are rated on two characteristics: permeation and degradation. Permeation refers to the penetration of the glove by the chemical. For each material tested, there is a “penetration rate” — the rate at which the chemical passes through the material and a “breakthrough” time — the length of time it takes for the chemical to go completely through the glove. Degradation measures the deterioration of the physical properties of the glove, for example, softening or hardening, resulting from contact with the chemical. Charts will usually also provide information on how suited the glove is for the chemical, in a rating ranging from “excellent” to “not used” or “not recommended.”
“If you wear Latex and you’re working with acetone, for example, they will tell you the rate of penetration is about 30 seconds,” MacKinnon says. “Within about 30 seconds of getting acetone on the Latex gloves, you will see them start to expand like a balloon. Within another 30 seconds, the gloves will start to fall apart. Now you’ve reached degradation, where there’s a full breach of the PPE.”
Many materials are used in the manufacture of chemical resistant gloves, including butyl, neoprene, nitrile, linear low-density polyethylene (LLDPE), natural rubber, neoprene mix, polyvinyl alcohol and polyvinyl chloride (PVC). Wool, leather and cotton, however, should never be used for chemical handling. They’re very permeable and will soak in anything that spills on them, so chemicals are easily transferred to the skin, says Terry Thomas, Occupational Safety Standard of Excellence (OSSE) technical advisor at the Chilliwack, B.C.-based Manufacturing Safety Alliance of BC.
It is important to always consult your glove manufacturer or distributor. Different manufacturers make gloves differently — using materials in different quantities and thicknesses, for example, which affects permeation rates — and they can provide specific information about the gloves they sell.
Employer's responsibilities
Provincial regulations generally state it is the duty of the employer to determine the protection required and make sure workers wear appropriate PPE. It is necessary for the employer to have a safety professional or other competent person conduct the risk assessment and select the most suitable gloves.
“There are so many types of gloves out there to meet different types of things — you can have nitrile gloves that are very specific to chemical handling, specific to biological handling or specific to handling delicate electronic components,” MacKinnon says. “It’s important that the person doing the risk assessment understand what are the risks and what do they need to do to mitigate those risks. So the burden is on the employer.”
Whether provincial legislation specifically requires the employer to pay for the gloves varies among jurisdictions. In Alberta, for example, OHS law does not say who pays for safety gloves, while in British Columbia and Quebec, employers are required to pay for chemical resistant gloves, Thomas says.
In the case of an extremely hazardous chemical, provincial OHS regulators expect the employer to try to engineer in a delivery or handling system to minimize the actual worker exposure to the chemical, Thomas adds. For example, instead of pouring hydrochloric acid out of a large container into a working container, you might be able to use a delivery system. Some systems have a pump attached to the container that allows the product to be decanted into a smaller container — or through a series of hoses — and delivered right into the work in progress.
Chemical resistant gloves should come with the manufacturer’s instructions on how to properly decontaminate or clean and maintain them, says Chouljian.
“You should clean the gloves as the supplier or manufacturer recommends, so you’re not causing the material to be degraded or eroded, which causes the glove to not work as it’s supposed to.”
Workers should be aware of the chemicals they are using and what their risks are. They should also know to inspect gloves for damage before putting them on. Damaged gloves should be discarded.
“Any tears or cuts in the gloves could cause the hazardous chemical to leak through, which renders the gloves useless because the hands are being exposed to the hazard. Before putting on the glove, double check to make sure it is in good condition and they’ve been maintained properly,” she says.
Because the selection of gloves is chemical specific, a company that uses a number of chemicals may need several different kinds of gloves for workers, Thomas says. This is why employers should do an inventory of all the chemicals they have in their workplace and try to reduce or standardize the chemicals they use.
“I’ve been in workplaces where they have more than 400 different, controlled products from various manufacturers. But if they start standardizing the type of paint they use, the type of solvent they use for cleaning metals, they can reduce their chemical inventory by 75 or 80 per cent,” he says. “If you can standardize your chemicals, you can also reduce the various types of PPE that you require, especially when it comes to gloves.”
After sustaining the burn, the laboratory worker who was burned by the trifluoroacetic acid said she was not aware that handling that type of chemical could produce such a burn. In fact, trifluoroacetic acid can form hydrofluoric acid when it comes in contact with moisture. Moreover, hydrofluoric acid can cause deep burns that may not become painful for several hours after the worker comes in contact with the chemical.
The lab made several mistakes. First, it should have kept a hydrofluoric acid burn kit nearby, says the American Industrial Hygiene Association (AIHA). It should also have assumed containers are contaminated and made sure workers wore appropriate gloves when handling chemical containers. Finally, it should have made sure workers were aware of the hazards of the chemicals before handling them.
Linda Johnson is a freelance journalist based in Toronto. She can be reached at [email protected].