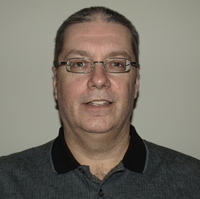
Guy Chenard talks about the importance of identifying hazards and managing risk to prevent accidents from happening in the workplace. Using a four-point plan to conduct risk analysis, he draws on his experience as a senior health and safety advisor to show the way toward establishing a successful safe work plan.
As a senior health and safety advisor, one of my job duties is to investigate accidents at work. The investigation process provides the company with a better understanding of the issues that played a role in the event. Lessons learned from the investigation can then be adopted to prevent further accidents from occurring.
Over the years, I have found that many of the accidents I’ve investigated could have been prevented had the workers and supervisors clearly understood and evaluated the risks involved with their work. This would have enabled them to better plan for the job and address the hazards with appropriate controls.
Many workers have had hazard awareness training and are able to identify the specific hazards in the workplace that could expose them to harm. However, they don’t necessarily understand or evaluate the risk of injury that is involved with the job. They also do not properly address changes in the work that may impact the risk.
The purpose of this article is to explain the basics of risk and to provide a method of evaluating this risk once the workers have identified the hazards in their job tasks.
What is Risk?
Risk is typically defined as “the likelihood of being injured due to exposure to a hazardous condition or event and the severity of injury caused by that exposure.” It is usually represented as:
Risk = frequency of exposure x probability of harm x severity of harm
The frequency is the number of times you perform a task that is exposing you to a hazard in a given time period. Do not get complacent with the work just because you have performed it in the past with no issues. The risk is always present no matter how many times you have performed the job.
The severity of harm is how severe the injury is likely to be if the exposure to the hazard is not controlled. The greater the energy or hazard, the greater is the potential for injury or harm. You’ll need to ensure that the safe work plan includes the necessary provisions for appropriate first aid and emergency response, should an accident occur.
The probability of harm is the likelihood of being injured due to exposure to the hazard. Can you get injured performing the task? This is the critical component of risk that should get the most attention when evaluating the hazard and then determining the essential controls to minimize exposure to it. These controls include following procedures or safe work practices, using the appropriate personal protective equipment or devices, communicating issues or concerns and re-evaluating the safe work plan should changes occur.
So how do we include the risk factor in our safe work plan?
First, we need to perform a risk assessment of the work. This is a process of evaluating the risk that can develop from exposure to a hazard, reviewing any of the existing controls that are in place and then determining if the risk is considered acceptable.
Most health and safety managed system models define an acceptable risk as one that has been reduced to a level that a company can tolerate based on its legal requirements and safety policy. The following information is an example of a risk assessment process.
Identifying the hazards
Workers and supervisors require hazard awareness training to enable them to identify hazards in the workplace. Typically, this consists of energy analysis and job safety analysis techniques. This information allows workers to determine what are the hazards and whether there will be potential exposure.
Risk analysis
To help us with risk analysis, we need to look at four elements in the workplace that may impact the risk.

These four elements need to be considered before selecting an appropriate control or barrier for each hazard indentified for the work activity.
Workers. You need to consider the people doing the work or that may be present around the workplace during work activities. Are the workers: new/young workers; temporary workers;
other work groups (such as contractors). Do the workers have sufficient awareness of the hazards in the workplace? Are they trained? Have they had an orientation or visited the work site? Are there any communication issues?
Documentation. Retrieve all documentation that is available and required to safely perform the work. This includes: lock-out/tag-out, work procedures, job safety analysis worksheets, operating manuals, permits, log sheets, written instructions, approved work practices, etc. Ensure that the workers are familiar with these documents and that they have access to this information.
Equipment. Equipment includes machinery, tools, buildings, structures, devices, guards, vehicles, personal protective equipment, etc. It is important that these particular items are inspected prior to use and maintained in good condition. Ensure that tools are suitable for the intended use and that they have adequate capacity for the work. This includes any equipment from contractors being used on your work site. A visual inspection of the work area prior to engaging in work activities is recommended as a way to evaluate equipment.
Workplace. The workplace encompasses the physical layout of the work site and also the outdoor environment. This would include: housekeeping; lighting; atmosphere (confined spaces); weather; and, spill control (drainage). You need to ensure that these items are considered when dealing with the energy source or hazard associated with the work.
Evaluate all four elements for each energy or hazard identified in your work plan. This will prompt you to consider the impact that each element may have on the hazard and give you a better sense of the work conditions specific to the safe work plan.
Selecting controls
Prior to selecting appropriate controls or barriers to minimize the hazard (based on the risk analysis), you need to consider two important issues: barrier reliability and the potential for human error.
When considering the barrier, you need to determine that it will be adequate, that it will be functional and that it will be implemented to control the hazard. The worker must ensure that the barrier is designed for the intended use, that it is working (inspection/testing) and that it will be used to protect them from exposure on the job.
The potential for human error will always exist in any risk-based activity at work. Typically, human error can be present as a skill-, rule- or knowledge-based potential. You’ll need to determine if the workers are properly trained to perform the work, that they understand all of the applicable rules and that they have sufficient experience with the work and its associated hazards.
Once these items have been reviewed, you are now ready to select the appropriate control barriers.
Safe work plan
The safe work plan may now be completed with all of the risks having been evaluated and appropriate controls identified to reduce or minimize the worker’s exposure to the hazard. Safe work plans often include a written job safety analysis to clearly identify the hazards and controls required to perform the task. These should be reviewed by the supervisor and the crew on a daily basis.
Finally, to assess all probabilities of harm, you need to be aware of any changes in the workplace. Change can come in the form of the four elements: workers, documentation, equipment and workplace. Therefore, identifying change and analyzing its potential impact on the risk must be an on-going consideration before, during and after the job has been completed.
Do not get complacent and ignore changes in the safe work plan. This is where many small issues can develop into bigger problems. Should changes occur, you’ll need to stop the job, re-assess and re-plan the work.
The bottom-line
We all have the tools and equipment required to control risks at work and to minimize the probability of being injured on the job. By utilizing our knowledge, training and experience, we can evaluate risks and manage them to an acceptable level.
----------------
Guy Chenard is a senior health and safety advisor for Ontario Power Generation. Guy is a frequent contributor to Canadian Occupational Safety magazine.
As a senior health and safety advisor, one of my job duties is to investigate accidents at work. The investigation process provides the company with a better understanding of the issues that played a role in the event. Lessons learned from the investigation can then be adopted to prevent further accidents from occurring.
Over the years, I have found that many of the accidents I’ve investigated could have been prevented had the workers and supervisors clearly understood and evaluated the risks involved with their work. This would have enabled them to better plan for the job and address the hazards with appropriate controls.
Many workers have had hazard awareness training and are able to identify the specific hazards in the workplace that could expose them to harm. However, they don’t necessarily understand or evaluate the risk of injury that is involved with the job. They also do not properly address changes in the work that may impact the risk.
The purpose of this article is to explain the basics of risk and to provide a method of evaluating this risk once the workers have identified the hazards in their job tasks.
What is Risk?
Risk is typically defined as “the likelihood of being injured due to exposure to a hazardous condition or event and the severity of injury caused by that exposure.” It is usually represented as:
Risk = frequency of exposure x probability of harm x severity of harm
The frequency is the number of times you perform a task that is exposing you to a hazard in a given time period. Do not get complacent with the work just because you have performed it in the past with no issues. The risk is always present no matter how many times you have performed the job.
The severity of harm is how severe the injury is likely to be if the exposure to the hazard is not controlled. The greater the energy or hazard, the greater is the potential for injury or harm. You’ll need to ensure that the safe work plan includes the necessary provisions for appropriate first aid and emergency response, should an accident occur.
The probability of harm is the likelihood of being injured due to exposure to the hazard. Can you get injured performing the task? This is the critical component of risk that should get the most attention when evaluating the hazard and then determining the essential controls to minimize exposure to it. These controls include following procedures or safe work practices, using the appropriate personal protective equipment or devices, communicating issues or concerns and re-evaluating the safe work plan should changes occur.
So how do we include the risk factor in our safe work plan?
First, we need to perform a risk assessment of the work. This is a process of evaluating the risk that can develop from exposure to a hazard, reviewing any of the existing controls that are in place and then determining if the risk is considered acceptable.
Most health and safety managed system models define an acceptable risk as one that has been reduced to a level that a company can tolerate based on its legal requirements and safety policy. The following information is an example of a risk assessment process.
Identifying the hazards
Workers and supervisors require hazard awareness training to enable them to identify hazards in the workplace. Typically, this consists of energy analysis and job safety analysis techniques. This information allows workers to determine what are the hazards and whether there will be potential exposure.
Risk analysis
To help us with risk analysis, we need to look at four elements in the workplace that may impact the risk.

These four elements need to be considered before selecting an appropriate control or barrier for each hazard indentified for the work activity.
Workers. You need to consider the people doing the work or that may be present around the workplace during work activities. Are the workers: new/young workers; temporary workers;
other work groups (such as contractors). Do the workers have sufficient awareness of the hazards in the workplace? Are they trained? Have they had an orientation or visited the work site? Are there any communication issues?
Documentation. Retrieve all documentation that is available and required to safely perform the work. This includes: lock-out/tag-out, work procedures, job safety analysis worksheets, operating manuals, permits, log sheets, written instructions, approved work practices, etc. Ensure that the workers are familiar with these documents and that they have access to this information.
Equipment. Equipment includes machinery, tools, buildings, structures, devices, guards, vehicles, personal protective equipment, etc. It is important that these particular items are inspected prior to use and maintained in good condition. Ensure that tools are suitable for the intended use and that they have adequate capacity for the work. This includes any equipment from contractors being used on your work site. A visual inspection of the work area prior to engaging in work activities is recommended as a way to evaluate equipment.
Workplace. The workplace encompasses the physical layout of the work site and also the outdoor environment. This would include: housekeeping; lighting; atmosphere (confined spaces); weather; and, spill control (drainage). You need to ensure that these items are considered when dealing with the energy source or hazard associated with the work.
Evaluate all four elements for each energy or hazard identified in your work plan. This will prompt you to consider the impact that each element may have on the hazard and give you a better sense of the work conditions specific to the safe work plan.
Selecting controls
Prior to selecting appropriate controls or barriers to minimize the hazard (based on the risk analysis), you need to consider two important issues: barrier reliability and the potential for human error.
When considering the barrier, you need to determine that it will be adequate, that it will be functional and that it will be implemented to control the hazard. The worker must ensure that the barrier is designed for the intended use, that it is working (inspection/testing) and that it will be used to protect them from exposure on the job.
The potential for human error will always exist in any risk-based activity at work. Typically, human error can be present as a skill-, rule- or knowledge-based potential. You’ll need to determine if the workers are properly trained to perform the work, that they understand all of the applicable rules and that they have sufficient experience with the work and its associated hazards.
Once these items have been reviewed, you are now ready to select the appropriate control barriers.
Safe work plan
The safe work plan may now be completed with all of the risks having been evaluated and appropriate controls identified to reduce or minimize the worker’s exposure to the hazard. Safe work plans often include a written job safety analysis to clearly identify the hazards and controls required to perform the task. These should be reviewed by the supervisor and the crew on a daily basis.
Finally, to assess all probabilities of harm, you need to be aware of any changes in the workplace. Change can come in the form of the four elements: workers, documentation, equipment and workplace. Therefore, identifying change and analyzing its potential impact on the risk must be an on-going consideration before, during and after the job has been completed.
Do not get complacent and ignore changes in the safe work plan. This is where many small issues can develop into bigger problems. Should changes occur, you’ll need to stop the job, re-assess and re-plan the work.
The bottom-line
We all have the tools and equipment required to control risks at work and to minimize the probability of being injured on the job. By utilizing our knowledge, training and experience, we can evaluate risks and manage them to an acceptable level.
----------------
Guy Chenard is a senior health and safety advisor for Ontario Power Generation. Guy is a frequent contributor to Canadian Occupational Safety magazine.