Standard occupational exposure limits must be reduced for workers on extended work schedules
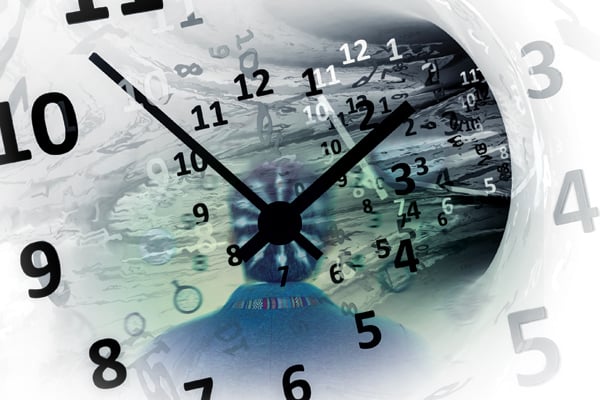
One main characteristic of the workplace today is the steady decline of the 9-to-5 day. In Canada, about 30 per cent of all employees now work non-standard work schedules. These new schedules may entail work at night or on weekends, shifts, split-shifts or on-call work. Increasingly, they require people to work longer days.
For safety managers, the move to extended shifts raises the possibility of increased exposure to chemical hazards among workers exposed to hazardous substances over a longer day. Occupational exposure limits are based on the standard work schedule, and managers need to adjust these established limits for work shifts longer than eight hours. By understanding how to use the different adjustment models available, safety professionals can keep the chemical exposure of workers on irregular shifts within reasonably safe levels.
Non-standard shifts are used in many industries, such as construction, manufacturing, health care and security. They are also becoming more common in industries that involve continuous process operations, such as chemical manufacturing, oil refineries, steel mills, drilling rigs and paper mills, which require two or three shifts in a 24-hour period.
The trend to specialized production is also driving a need for extended shifts, says Simon Aubin, chemist and industrial hygienist at the Institut de recherche Robert-Sauvé en santé et en sécurité du travail (IRSST) in Montreal.
“Many manufacturing industries have been moving their production to foreign countries. What’s left here is more specialized work, done by highly skilled, qualified workers, so the mandates are more specialized. They have shorter deadlines, so it often implies longer, irregular shifts to be able to deliver the job on time.”
In remote areas, too, many industries have adopted a fly-in, fly-out routine. Workers will eat and sleep at the work site. Because they are there only for a certain length of time and they want to get as much done as possible during that time, shifts will be much longer than normal. A similar situation prevails at many underground mines.
“It may take you, say, 45 minutes to get down to the work site, so you won’t end your day after seven or eight hours; you will stay in the mine for at least 10 or 12 hours. It’s also the complexity of the work. To get it going at first, it could take longer than usual, so once you get started, you better do it for a longer time if you want to maximize your presence there,” Aubin says.
LONGER DAYS, SHORTER NIGHTS
An occupational exposure limit (OEL) is the concentration of a chemical in the workplace air to which most people can be exposed without experiencing harmful effects, according to the Canadian Centre for Occupational Health and Safety (CCOHS), based in Hamilton, Ont. The amount is often expressed in milligrams per cubic metre (mg/m3).
In Canada, provincial OELs are largely based on the maximum exposure limits for chemical substances established by the American Conference of Governmental Industrial Hygienists (ACGIH), which refers to the limits as threshold limit values (TLVs). These OELs vary among provinces, so safety managers in different provinces will be adjusting different OELs.
There are three types of exposure limits:
• The time-weighted average exposure value (TWAEV) is based on the average concentration of a chemical in the air in a worker’s breathing zone for a normal eight-hour workday and 40-hour workweek. It is calculated by averaging the level of samples taken during a specific time period.
• The short-term exposure value (STEV) is the average concentration to which workers can be exposed for a short period (usually 15 minutes) without experiencing irritation, long-term or irreversible tissue damage or reduced alertness.
• The ceiling value (CV) exposure limit is the maximum allowable limit regardless of exposure time.
Employers must ensure that no worker is exposed to a substance that exceeds the OEL, the short-term exposure limit or the ceiling limit. To establish compliance with this requirement, an employer is required to have an acceptable workplace monitoring program in place.
The difficulty for employers who have workers with irregular shifts is that because OELs are based on a normal work schedule, using an established OEL for workers with extended shifts creates the risk of increased exposure. During work, the body accumulates the contaminant to a particular level (the “body burden”) and then eliminates the contaminant in the hours away from work.
“The (OELs) are based on a regular work schedule, which means eight hours a day, 40 hours a week. If you work eight hours while you’re exposed to a contaminant, in theory you have a period of 16 hours for your body to recover. If you start working a 12-hour shift and have only 12 hours to recover, then you’ve had a higher dose during the time you worked and less time for recovery. That could increase the burden,” says Marc-André Lavoie, registered occupational hygienist and president of Dartmouth, N.S.-based Risk Marcker.
“So, in circumstances where there is a different schedule, you need to put some thought into how to maintain the same level of safety for these unusual work shifts.”
ADJUSTING THE OEL
Where people are working non-traditional shifts, the safety manager must adjust the established OELs. Often, the way of adjusting for irregular work shifts has been to reduce the exposure limit based on the increased work time. For example, British Columbia’s OHS regulation specifies that if the length of a workday is between eight and 10 hours, the employer will multiply the OEL by a factor of 0.7; if between 10 and 12, by a factor of 0.5; if between 12 and 16, by a factor of 0.25; and if more than 16 hours, by a factor of 0.1.
However, other methods, or models, have been developed to modify the standard OELs so that they apply to non-standard work schedules. These models, three of which are commonly used today, take into consideration exposure and recovery times and require different types and complexity of information, such as the toxicity of the individual substance. The OELs and adjustment calculations must be interpreted and applied by professional occupational hygienists.
The Quebec Model, which followed a method devised in 1979 by the Occupational Safety and Health Administration (OSHA) in Washington, D.C., was developed in the late 1990s by experts at the University of Montréal and the IRSST. It classifies chemicals into four categories.
“The advantage of our approach is that it’s adapted to the toxicological characteristics of the chemicals involved,” Aubin says. “Our group of experts, based on current scientific knowledge, can say that a given substance will be eliminated throughout 24 hours, or it may need a week or even more to be eliminated. This will determine what category the substance is put into. The longer the elimination time, the longer period [days or weeks] you have to adjust the OEL.”
Category I comprises substances regulated by a ceiling value, irritants with short-term effects and substances whose maximum exposure limits are based on technological limitations. Substances that fall in this category need no adjustment.
Category II contains acute toxicants. These have short-term effects, do not accumulate and have an adjustment factor derived from hours of work per day.
Category III contains chronic toxicants. These have long-term effects, can accumulate and have an adjustment factor derived from hours worked per week (according to the “repetitive work cycle,” the calendar period during which the work schedule is exactly repeated).
Category IV contains substances that are both acute and chronic. These have both short- and long-term effects, and the adjustment factor selected will be based on either hours worked per day or per week, whichever is more conservative.
To calculate the OEL to be used for an extended work shift, a safety manager follows an equation using the standard work schedule. In the case of a Category II chemical, the manager will divide the standard shift per day by the actual number of hours worked. Thus, if a worker works 12 hours a day, the reduction factor will be equal to 8/12. The OEL (according to the province or territory) is then multiplied by a factor of 0.67 to get the adjusted exposure limit.
In the case of a Category III chemical, the manager divides the standard number of hours worked per week by the average number of hours actually worked per week based on the repetitive work cycle. Thus, for a worker working 84 hours during a two-week work cycle, the reduction factor will equal 40/42. The OEL is then multiplied by a factor of 0.95 to get the adjusted exposure limit.
Although it’s important for safety managers to understand how the equation is reached, they can simply consult tables of factors on the IRSST website. Each table corresponds to one of the three categories of chemicals that require adjustment.
For safety managers, the procedure is fairly straightforward. After identifying the chemical substance, they should check to see into which adjustment category the chemical falls. They then check the relevant table to find the adjustment factor. If Category III, they will also need to establish the repetitive work cycle to calculate hours worked per week.
The Quebec model is also in Australia, and it is referenced by the ACGIH and other health and safety organizations, Aubin says. In 2018, the Ontario MOL recommended the model’s exposure adjustment calculations be used to adjust OELs. A list of chemicals and their corresponding category is available on the IRSST website.
The Brief and Scala method, considered the simplest and most conservative of the three models, uses equations that take into account both the longer exposure time and corresponding shorter recovery time caused by an extended shift. The method is used for all chemicals regardless of their half-lives (the amount of time it takes for half an initial amount of a substance to disintegrate), with the exception of substances whose OEL is based on concentration and may not be affected by hours of exposure. The user calculates both a daily and weekly adjusted exposure limit, and the more conservative of the two cases should be used.
Finally, the pharmacokinetic model is founded on the idea that the toxic effect of chemicals is related more to the concentration of chemicals in the body than in the air. It uses a mathematical model that requires the input of information such as the biological half-life of a chemical to predict peak body burden. Like the Brief and Scala model, the pharmacokinetic model takes into account both the exposure and recovery time. This model is more difficult to use because biological half-lives are not available for many chemicals. It is the least conservative of the models.
Of these commonly used ways to adjust OELs, no one model is generally accepted more or less than the others, says Jan Chappel, senior technical specialist at CCOHS.
“There’s no one way to make those adjustments. You need someone with the knowledge, like an industrial hygienist, to make that assessment. You need someone who knows what chemicals you’re working with, how people are exposed, whether it’s inhaled or dermal. And then they take the model that best matches what’s happening in the workplace,” she says.
In regard to provincial occupational health and safety law, the Brief and Scala model is required in some cases unless, as the Alberta code says, the employer has received approval from a director of occupational hygiene to use another method. In other jurisdictions, Lavoie says, employers are not required to use a specific model.
“Nova Scotia is not much different than many other jurisdictions where the legislation is not set in stone,” he says. “Nova Scotia would most likely be comfortable if you apply any established model and are able to support it with a reasonable explanation.”
When employers do not have an industrial hygienist on staff and do not want to consult one, they should just use the Brief and Scala model to adjust exposure limits, Lavoie says.
“That’s because it’s the most restrictive one. The philosophy here is the more you know about your product [for example, knowing the toxicological half-life], the more options you have. The less you know about your product, the more restrictive the model you have to apply because of the uncertainty,” he says.
Moreover, he adds, employers who are not completely sure their chosen adjustment method will limit exposure to a safe level should introduce some medical surveillance of workers at the same time they implement an extended shift.
MULTIPLE CHEMICAL EXPOSURE
Often, workers are exposed to more than one chemical at a time. In this situation, the safety professional must first analyze the individual chemicals to determine what kind of effect the combination will produce. Some chemicals, due to similarity of toxicity, will simply produce an increase in concentration. Others will interact in different ways to produce completely different effects.
The combined effects of chemicals are classified as independent, additive, antagonistic, potentiating and synergistic. Independent materials are evaluated individually and, along with their concentrations, are used in a formula to determine the adjusted OEL. There is no model for adjustment of the exposure limit where chemicals are thought to have synergistic or potentiating effects. It is important to note, too, that the biological effect of exposure to several chemicals is often unknown. The safety manager should try to find a substitute for one of the chemicals to avoid the potential effect.
In adjusting an OEL, the resulting figure should always be lower, Chappel adds. An exposure limit should never be adjusted upwards for shorter shifts.
“We assume a non-traditional work schedule is a longer workday. But there are people who work shorter workdays. However, they caution never to use the equations to raise the exposure limits. You can’t skew the numbers to allow someone to be exposed to more than the OEL,” she says. “That would not be considered good practice at all.”
Safety managers should also keep in mind that some workers at their site may be working at another job that the employer doesn’t know about, Chappel says. For this reason alone, it is a good idea to reduce exposures as much as possible.
“In all cases, the better approach is to keep your exposures as low as possible regardless of the OELs. You should try and minimize or eliminate your exposures as much as you can. OELs are good guidelines, but they don’t guarantee a person won’t become ill in the long term,” she says.
“The general term is called the precautionary principle: Take action when you don’t have all the information. But in this case, take action to keep exposures as low as possible.”
Linda Johnson is a Toronto-based freelance journalist who has been writing for COS for eight years.
This article originally appeared in the August/September 2019 issue of COS.