Company wins gold in retail and services category of Canada's Safest Employers awards
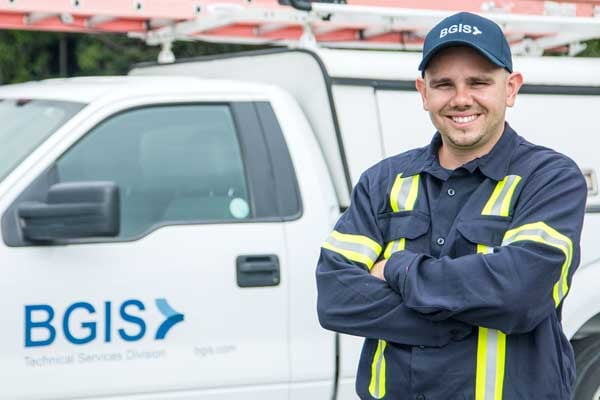
Workers at BGIS are expected to “Take two for safety.” Before they start any job, they must take two minutes to identity hazards, ensure they have all the necessary tools, are familiar with proper procedures and are in the right mindset to do their work safely.
“That’s all it takes is two minutes to stop and think before you perform the work,” says Peter Papagiannis, COO of BGIS, a provider of real estate management services, headquartered in Markham, Ont. “I would suggest that is probably one of the most important parts of our program.”
Whether it’s the first time a worker completes a task or the 100th time, BGIS wants him taking two minutes for safety. To keep this practice top of mind and engage workers, BGIS held a video contest around it during North American Occupational Safety and Health (NAOSH) Week.
BGIS deploys hazard stations within each client site that include details about all known site-specific hazards, safety data sheets, building materials, results of indoor air quality assessments and any other relevant safety information.
“In order to protect anyone that comes into the building, you need to know what’s in the building and the history of what’s happened in that building,” says Mary Lou Sinclair, director of health, safety and environment. “If there’s a new person who is looking after the building, they have at their disposal all the information at those hazard stations.”
A toll-free 24-7 contact number for BGIS health and safety support can also be found at the hazard station, should there be any questions or concerns from any of the work parties present on site.
When a BGIS subcontractor is found at fault of a hazardous occurrence, BGIS’s red flag process puts them under significant scrutiny. The work is temporarily suspended while BGIS reassesses whether or not the subcontractor is adequately qualified to conduct the work. The subcontractor’s policies, procedures, training records, tools and personal protective equipment are examined.
“We have a very serious conversation with them. We bring their leadership in and we ask them what they’re going to do to make sure they correct it,” says Sinclair. “The best solution is not always to say, ‘You can’t work for us anymore.’ The best solution is usually a vendor who has learned from their issue and has raised the bar so it’s not going to happen again.”
All 4,700 workers at BGIS are strongly encouraged to report near misses. They are given a yearly score based on their hours worked and the number of near misses they report — and the more, the better, says Sinclair.
“The lower the score, the worse it is. If you don’t find things, it’s not that they’re not there, maybe we’re not looking hard enough.”
This program has created a culture of reporting.
“We wanted to create an environment where there is a positive reinforcement for an identification of risk,” says Papagiannis. “It supports the habits of watching out for trouble.”
All meetings at BGIS — whether it be finance, sales, operations or client meetings —begin with a safety moment. It’s an experience an individual has had or something to be aware of from a safety perspective. Some examples include watching out for kids on the road during back to school season, using proper lifting procedures, checking smoke alarms and safely shovelling snow. Anybody can put forth an idea and it may be work-related or not.
“The more personal, the better,” says Papagiannis. “That way safety’s not thrust upon you, it’s apart of you.”
This article originally appeared in the October/November 2017 issue of COS.