Putting a positive spin on inspections can strengthen an organization's safety culture
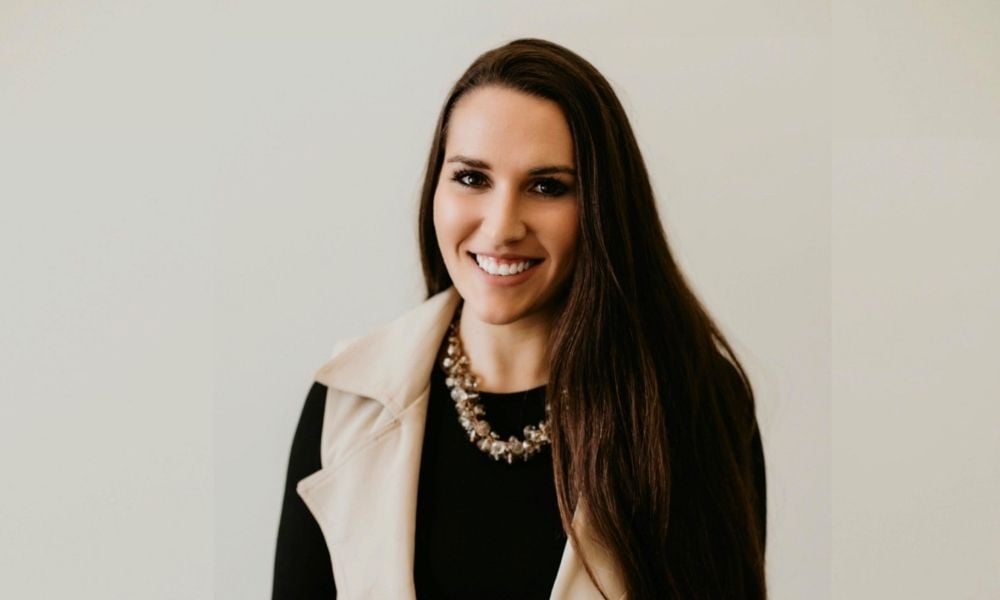
One of the most important questions safety leaders can ask themselves is: “As a leader, am I consistently demonstrating the behaviours that I expect of my employees?” Says Sheri Benson.
Benson got her start in safety in the energy sector at oilfield services company Tesco Corporation (since acquired by oil and gas drilling contractor Nabors Industries) where she eventually became HSE Manager. Based in Calgary, Benson founded Thrive Safety Consulting in 2019. The organization offers health and safety consulting services including training and safety program development.
Thrive is also a Certified Auditor with Energy Safety Canada, one of The Best Work Safety Training in Canada awardee.
Benson says that there are a number of unsafe acts or at-risk behaviours such as rushed work, complacency, negative attitudes or housekeeping issues.
She explains that to counter dangerous workplace behaviours, health and safety officers need to consistently lead by example and need to ask themselves, “am I consistent in my messaging to employees?”
In addition, how are employees perceiving the messages that might be relayed, asks Benson:
“That is a critical point […] our words are very important, I think we need to be very intentional with the words that we use sometimes when we’re giving direction.”
Key elements of a company’s safety program can be great stepping stones to strengthen organizational health and safety.
For example, when creating a workplace hazard checklist, “we want to make sure that when we have an inspection checklist that it’s relevant and that it’s specific to the operation, to the facility or to the organization,” says Benson.
There are a lot of great resources and tools out there which are great starting points, but ultimately she says that health and safety professionals need to put in efforts to make something that is tailored and relevant to what is being inspected.
And key elements of a safety program, such as inspections, can be a productive way to improve communication with employees.
“I really look at inspections as opportunities,” says Benson. Firstly, an opportunity to have a conversation:
Inspections can easily become a “check the box” exercise instead of something that is interactive, she says.
Asks Benson: “Are we using our inspection time to have conversations with workers and ask them questions on what could we be doing better? How are [the workers] doing? What do they need?”
Secondly, inspections “can also become something very negative or that employees perceive as very negative,” she says.
“One of the things that organizations can do is also build in an element of looking for safe behaviours or positive observations during the inspection process.”
This way, inspections are not only a tool for compliance but also a way to look out for positive things as well.
Intentionally and purposefully looking out for positive and safe behaviours is an opportunity to “instill that into the [organization’s] culture that inspections aren’t a bad thing – they can be positive as well,” says Benson.
“And we can use those opportunities,” she says, “to also identify and […] promote and drive those safe behaviours. So if we take that time during the inspection process to also identify the safe behaviours and drive those, I think that it’s a very powerful tool.”