Company wins gold in utilities and electrical category of Canada's Safest Employers awards
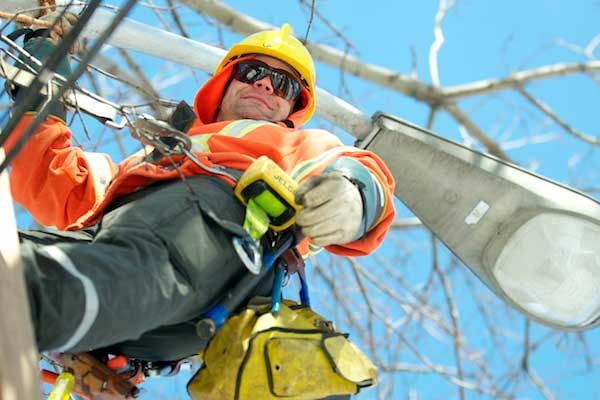
Every year, Toronto Hydro does a risk assessment of all workplace hazards. At last count, it identified and ranked 70 hazards — including electrical contact, confined space entry, motor vehicle incidents, working at heights and extreme weather.
That’s why the electric company shuts down for one day every year and all operations employees are asked to reflect on the need to work safely. On Safety Reflection Day, these workers participate in interactive exercises and listen to a motivational speaker.
“Typically, it’s someone who’s survived a traumatic event,” says David Johnston, director, environment, health and safety. “It’s to reinforce the message why you want to work safely.”
Toronto Hydro, which has 1,490 employees, provides about 10 days of training per employee per year, most of which is related to safety. Managers recently started using an advanced learning management system to help them keep track of training. To mitigate one of the company’s greatest risks, a driving simulator was introduced to provide effective defensive driving training to large numbers of employees.
Phil Genoway, manager, health and safety, says workers are using a new technology to make their cable-chamber entry procedure safer. While they used to rely solely on what they could see or hear in the underground spaces during pre-inspection, they now use thermography. The technology measures the temperature of cables and splices and thus provides valuable information on the condition of the cables so workers can better assess the hazards in the space before they enter.
Toronto Hydro also recently introduced a proactive equipment replacement program and has replaced a lot of equipment that it identified as being prone to failure.
“We’re trying to be proactive and replace equipment before something happens and puts some of our employees or the public at risk,” says Genoway.
When some pieces of equipment fail, they can release large amounts of energy and cause an explosion. Toronto Hydro’s arc flash project is designed to ensure workers adequately protect themselves before operating hazardous equipment, Genoway says. By mathematically calculating the amount of hazardous energy, safety managers know what level of personal protective equipment a worker needs when operating the equipment. A label on the equipment then tells the worker the precise type and level of personal protective equipment required.
Johnston says the safety team uses many means to communicate, including sending out safety alerts to employees, producing a large package of safety meeting materials every month for supervisors and conducting a poster program throughout the year. The team also takes advantage of Toronto Hydro TV, which broadcasts safety information across the company.
A serious incident review panel, consisting of all company executives, meets monthly and helps keep managers informed. For some time, safety managers have been using enterprise-wide software to report and track incidents and communicate that information to those who need to know. Supervisors also frequently receive safety information and current company statistics, including recordable injury frequency and number of days worked without lost-time injury.
This article originally appeared in the October/November 2017 issue of COS.