How to leverage Joint Health and Safety Committees
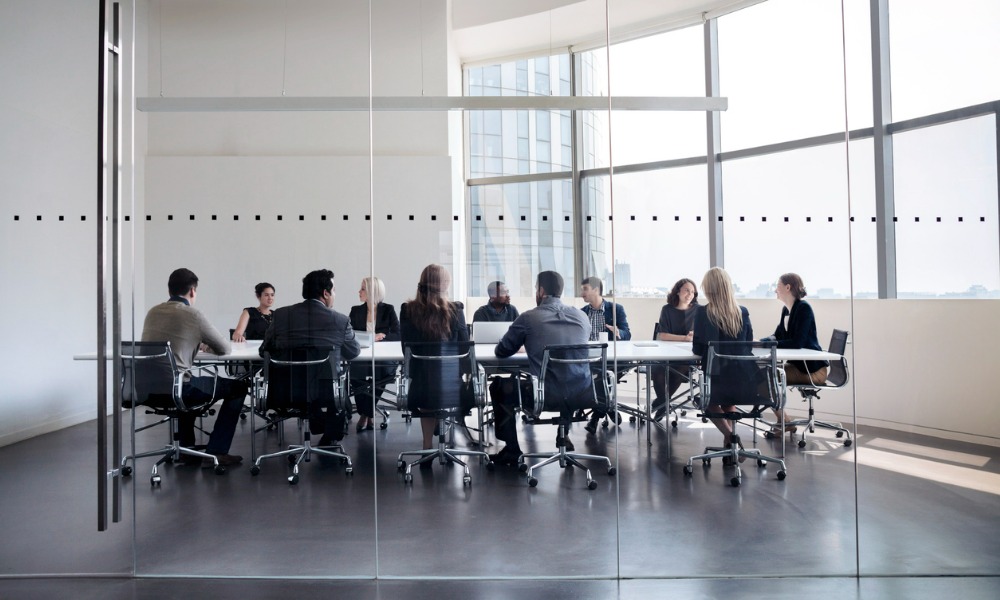
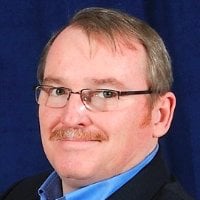
I was at our safety conference recently. Someone talked about an organization’s ability to read weak signals. It is an interesting topic for me. As with all things presented at conferences, the conundrum is operationalizing the idea.
The idea of weak signals in the organization was first discussed by Charles Perrow in his book Normal Accidents. Like most “new” ideas in health and safety, this one was a term for an existing phenomenon. Charles Perrow’s book was groundbreaking, taking the view that having an accident was normal and expected. He saw that system complexities made failures inevitable.
There are many great nuggets in this book. If you haven’t read it, you probably should, particularly if you are a health and safety practitioner.
Perrow talked about weak signals in the organization. This isn’t really a new concept. Anyone who’s ever investigated an incident always runs into people who say they knew something was going to happen or they felt that an incident was inevitable and there were problems—at least in hindsight.
Companies or their management often say we weren’t aware of problems, and so we can’t fix problems that we aren’t aware of. Fair enough. Those doing the work often see or correct things that could lead to an incident. Incidents are complex and have many causal factors, but having someone intervene to correct things before an incident is seductive.
These weak signals can be things like near-miss reports, but that is unlikely. By definition, “weak signals” can be ambiguous and difficult to read. These can be single events or several events that may appear unrelated but are somehow connected. These are the stealth precursors to incidents.
If only we could find a way to read these weak signals, we could predict future incidents and prevent them. That sounds impossible, I know. Particularly when you recognize that failures and incidents are inevitable because of the complex sociotechnical systems in today’s workplace.
That sounds like the Holy Grail of safety. It pulls together various theories and postulations from Human Organizational Performance to High Reliability Organizations.
What if I told you that was actually possible. You could actually read the weak signals, the early precursors to an incident, and intervene. Isn’t that worth something?
The trouble is systems run on data or inputs. You need information so it can be interpreted. How do you collect information on weak signals? It sure isn’t going to happen through near-miss reporting or safety cards of some kind. Like most important data, you have to go out and get it.
The trouble is that you need to separate the wheat from the chaff. Some information isn’t very useful. Some may seem trivial but is actually quite useful. Someone has to be able to judge what information is relevant or a real “weak signal.” Some think that should be the health and safety practitioner. I’m not sure I agree with that.
Wouldn’t the people doing the work every day be able to see those weak signals or small failures that they regularly overcome more readily than anyone else? Sure, they might need some prompting, encouragement, or even a little training, but I’m confident they could do it.
Here’s where it gets a bit weird. What if I told you there’s already a process to do this. What if I told you that you already have this process because it is required?
It’s true. Every company has a mechanism in place that is required by legislation and is, unintentionally, built to read weak signals within the organization and help the organization avoid incidents, particularly serious ones. That’s about as magical as safety gets.
What is this mysterious mechanism that can do these wondrous things? Well, it is the humble Joint Health and Safety Committee. Not convinced? I’ll go on.
First of all, Health and Safety Committees are required in every jurisdiction in Canada. Their purpose is not exactly to read weak signals in the organization, but that’s not much of a stretch. Here you have a group of people doing the work, sitting down with people with decision-making capability and resources (management) to solve health and safety problems. They even review incident investigations and procedural reviews.
So the same employees who display mindfulness and act to overcome errors and problems and poor procedures along with minor failures – these same employees get to talk directly to management. These are the same people who are best qualified to read the weak signals and sound the alarm if we take the time to listen and give them the right training and encouragement.
Imagine an employee working in an environment provided by an employer who sees problems and knows how to fix them. Imagine if that employee could go to a health and safety committee meeting or be on the safety committee and point out these solutions to people with authority and the resources to do something about it. It isn’t much of a stretch.
Now I’m sure you’re thinking about your workplace’s health and safety committee and wondering why this isn’t happening. Maybe you haven’t established expectations, provided the training, and demonstrated the support.
Health and Safety Committees get a bad rap as a necessary evil. What if they are a necessary part of the solution? Most organizations have low expectations of their Health and Safety Committees. I often wonder what would happen if we simply elevated the expectation and put a framework in place to help those committees be effective?
If you’re wondering if your committee or committees are effective, it’s easy to find out. Just ask what they’ve accomplished in the past year. Actually accomplished. Having the required number of meetings does not count.
Health and Safety Committees cannot solve everything or predict the future. However, I wonder why we often underutilize an almost custom-built mechanism to read weak signals in the organization. Academics have many theories, but sometimes the right solution for turning hindsight into foresight is staring you right in the face.