Company wins gold in public sector/non-profit category of Canada's Safest Employers awards
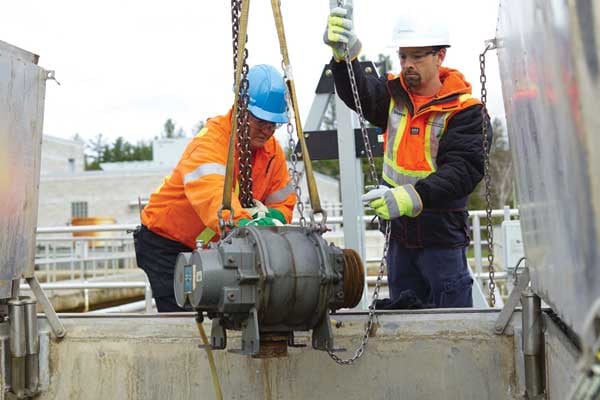
A few years ago, a senior operations manager at the Ontario Clean Water Agency (OCWA) was tired of hearing his staff say that eliminating certain work site hazards was not possible. In response, he launched the Achieving the Possible campaign for the northwest region and set out to shift the mindset of his staff.
“He said, ‘Nobody likes change, but we are going to make some changes and we are going to put our heads together and come up with how we can do things better, safer than how we have been doing them,’” says Randy Plener, director of occupational health and safety at OCWA in Toronto.
To spread the word about this new commitment to health and safety, the region hosted a safety barbecue for staff and their families as well as clients, contractors and community members. The event spread the word that OCWA is really making safety a priority and keeping safety top of mind each and every day.
“From a business perspective, OCWA benefited from this too because some of our non-clients heard about this, found out more and are now clients of ours,” Plener says. “Companies and organizations want to work with other companies that do things safely.”
After looking at things from this “possible” lens, the staff quickly realized they could achieve what they thought they couldn’t. They ended up improving safety for many different processes and tasks.
The agency has a very elaborate health and safety training matrix for its 820 employees located across 10 regions of the province. The first level is common training for all employees and includes a two-day safety overview course, Ministry of Labour mandatory training for workers and supervisors, an overview of the company’s health and safety portal and a module on how to complete effective incident reporting. Phase two is training based on the hazards and risks for specific jobs. The matrix identifies what training has to be done the first week, first month and so on. The training may include confined space, respiratory protection and chemical handling, for example.
Staff members at operational facilities must receive at least 12 hours of training each year, while corporate administrative staff members must log six hours. But these minimums are exceeded every year, says Plener. In 2018, staff in operational facilities averaged 23.29 hours per person. Training is a leading key performance indicator within OCWA and is tracked and formally reported monthly across the agency and at the board of directors’ meetings.
“That is something that, in an organization, really shows commitment because training takes time, but it also recognizes that training is really important — making sure that people are competent to do the tasks they are doing,” says Plener.
OCWA’s Speak Up for Safety is an engagement initiative that asks workers to answer the question, “How do you ensure that you and your colleagues work safely every day?” Each week, one answer is featured in the company newsletter.
“It’s very simple, but it gets workers to participate, to engage, tell us what they think and how they are doing the work safely,” Plener says.
In 2016, OCWA adopted a new safety management system, which has led to significant performance improvements. Lost-time incident rates have improved by 81 per cent and recordable incident rates have improved by 63 per cent. The new system has also allowed the agency to be more agile, quickly adapt to change and be less siloed.
“Whenever we’ve had a significant incident, our people have acted very quickly in order to make sure that those that need to be informed are informed and all the processes we have in place are followed, so that whether it happens in the north or east or wherever, everybody who needs to know knows very, very quickly,” Plener says. “That way, we are able to look at it and we can address any actions that need to be done, whether it’s local only or from the OCWA-wide standpoint.”
The executive management team at OCWA regularly conducts safety site tours. They listen to staff, ask them pointed questions about health and safety and solicit recommendations for what they can do to better support the workforce — and workers really appreciate these visits.
“You have the senior leadership going out into the operations to see what’s actually going on out there as opposed to just reading numbers or something that was sent into them, but primarily to really engage with workers and understand their thoughts on health and safety,” says Plener. “[Our staff] was really in awe that the CEO was taking time out of his busy schedule to go out and talk to them about safety.