Early challenge, plus formative years at a local sawmill, fueled Chris Grajek’s career at Allteck Line Contractors
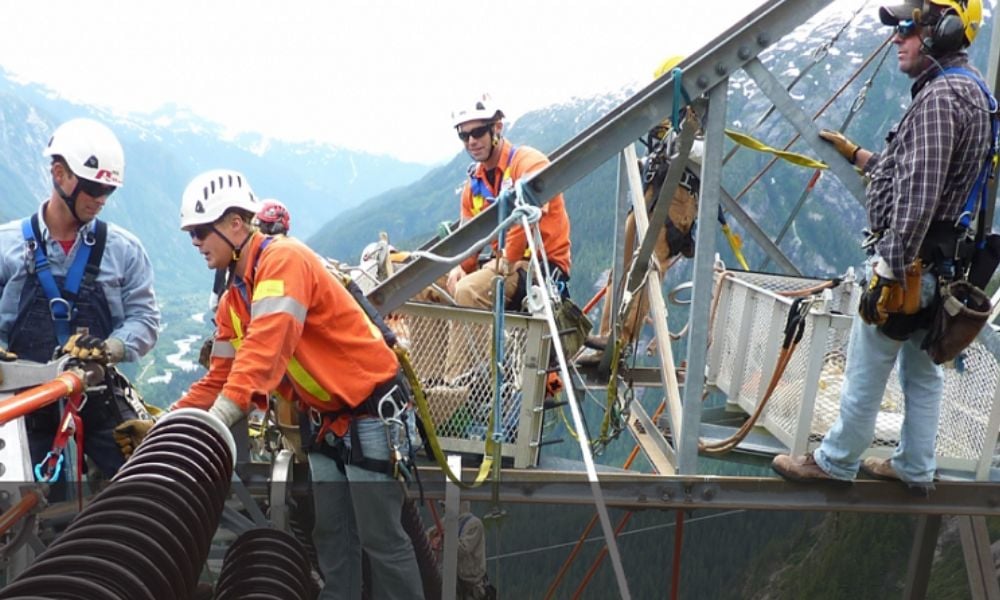
For Chris Grajek, it was his experience at a local sawmill that laid the foundations for his future career in health and safety.
“My father had been there for several years,” he says. “He was a millwright by trade. I got myself into [the] sawmill and started doing weekends – and the money was good. I got into production, working with heavy equipment, driving heavy equipment, operating machinery.”
Grajek spend several years doing that before finally going into maintenance. But it was his hands-on experience, coupled with his academic background in policy analysis, that positioned Grajek as a valuable asset - especially when the organization faced challenges with workers' compensation and general safety issues.
“I wanted to see the organization be successful and that was kind of when things started to happen and I got involved with safety and the work methods,” he tells COS.
Addressing the safety issues within the organization, Grajek and his colleagues faced a unique challenge – a percentage of the workforce was functionally illiterate. This prompted them to think outside the box, developing innovative solutions to make safety procedures more accessible.
“Maybe we can take pictures and maybe we can label things,” Grajek says. “We created posters of procedures with pictures, with diagrams, with labels. Because most people can read numbers and letters, they just couldn't associate with a page about something. And that was really the start of me getting into the safety profession.”
Grajek’s journey eventually led him to Allteck Line Contractors, which specializes in electric transmission and distribution services, where the diversity of projects and the opportunity to travel appealed to his adventurous nature.
“No one week was the same,” he tells COS. “There was no stopping me at that point.”
And in his current role, Grajek is confronted with the ongoing challenges of the industry, particularly the push for zero incidents.
“We're moving that emphasis and energy, not so much completely away from prevention… into those mitigating factors,” he says. “So, what are we going to do when you do make a mistake? When you come to work and you’re fatigued and times are tough and you need money - you're going to make mistakes. Or perhaps you didn't understand something – then what are we going to put into place that is going to allow the system to absorb those failures?”
Environment stewardship
Emphasizing the importance of realistic and collaborative solutions. Grajek, pictured above, also advocates for the integration of environmental stewardship and quality into the conversation on health and safety.
“If you're going to be an organization that puts safety and health as a priority, I think to exclude environment and to exclude quality out of that discussion just means you've siloed it,” he explains. “The health and safety becomes just this thing we have to do – it’s no longer part of the process. Where, for us, it’s all intertwined. They’re all blended into the work methods – there’s no differentiation. We don't even silo the financials between all three.
“Everything is a blended approach because if you need to do the work safely, you need to do it right. You need to have environmental stewardship for us.”
Underscoring this approach is Allteck’s involvement and relationship with the Indigenous communities – as well as the company’s commitment to building a better future together.
“First Nations is a huge involvement in what we do,” he says. “Community, sustainment, all those things. The philosophy for us when I started back in the day was we built gas lights – but it's not so much [that] anymore. We're here as solutions providers to build within our own company - to build the communities - and that mind shift has been big.”