Rick Hicks wants everyone to know 'what we do is so dangerous'
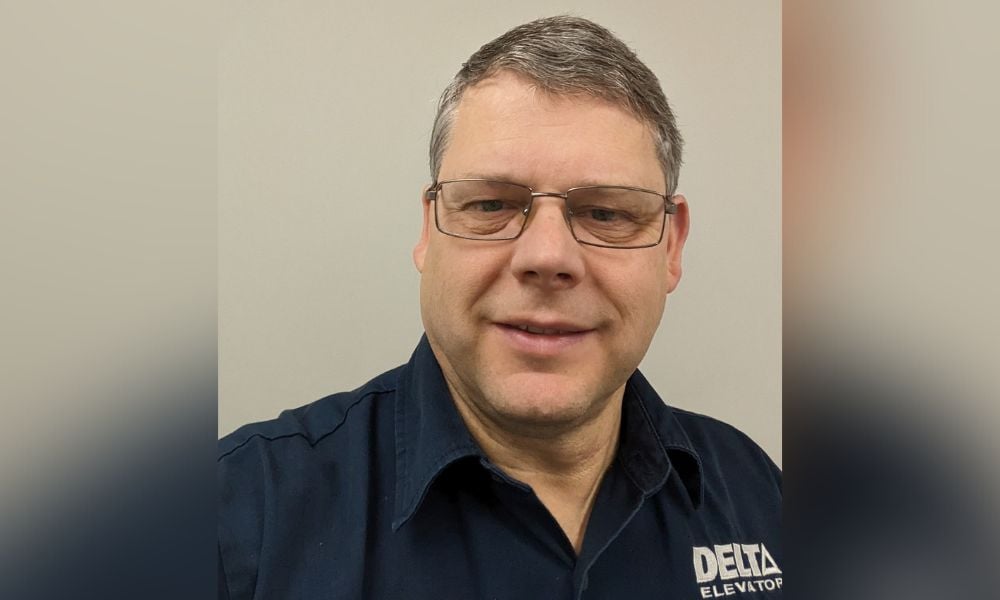
Rick Hicks remembers the first moment he thought to himself, “well I want to go home, everybody here needs to go home.” After spending nearly 30 years with Delta Elevator, the training and development supervisor is being honored with a safety award, and part of the reason he’s earned the recognition is because he never forgets how dangerous his job can be and he doesn’t let anyone else forget either.
Hicks recalls being on one of his first assignments when a colleague informed him someone was killed doing the same job he was doing. “He just walked up to me, and he said did you hear what happened? And exactly my job that I'm doing, someone is dead.” Hicks says moments like that throughout his career serve as reminders about the consequences of something going wrong.
Hicks is now a mentor to young workers. He assesses more than 50 apprentices and oversees their tracking of hours, education, as well as the training for all Elevating Devices Mechanic Trainee safety education, which is a Technical Standards and Safety Association (TSSA) certification. It’s his job to make sure future elevator mechanics don’t get hurt on the job.
Hicks has created hundreds of hours of curriculum and procedures to ensure up-to-date and effective training. He engages with people one-on-one in the field and he webcasts to more than 170 workers across the company’s five branches.
Hicks instills a key message in his trainees. “The person that's going to die most likely is going to be the person that's working on it.” Hicks acknowledges there is also a chance a person riding an elevator can be hurt too.
“The problem with what we do is we get used to the dangers,” says Hicks, who tries to keep himself and his trainees on their toes at all times, “people have to always remember that one misstep is the last step.”
It may sound grim, but elevator mechanics are often working at heights with sharp tools and around electrical hazards. Hicks says when he first got into the business, he didn’t totally understand the risks. He admits he was more focused on being seen as productive.
“I always went for a personal record. Got to be better, I got to be faster,” says Hicks, “and one of the things with that is if someone gets hurt, it slows everybody down.” That’s why Hicks teaches safety comes first. “You have to do it safe in order to do it fast.”
Part of his training involves reviewing pictures of accidents and near-misses. “One of the best ways to get the message across is to actually give them a visual along with the message.” But Hicks has never shown anyone an image of someone dying on the job. He does however tell them a story about a man who walked into a hoistway and died. The moment was captured on video, which was seen by the deceased man’s coworkers.
“And this is one of the pivotal moments that you see in their eyes, is when I tell them can you imagine looking around, and the person beside you, you get to watch a video of them dying.”
Hicks says stories like this can be effective training tools, especially in a small tight-knit industry. While the training appears intense, Hicks would argue it needs to be to “make sure they understand that what we do is so dangerous.”
It appears everyone is getting the message. The company has gone two million hours without a time-loss injury. “We're very proud of that one,” says Hicks, “we're aiming for three.”
And he has something else to be proud of now. He received the TSSA Individual Legacy Safety Award. “It just feels great,” says Hicks, who immediately shifts the spotlight to his team. “This is an entire company working together to make sure that we do things right.”
Because anything short of doing it right, can have tragic consequences.