Company wins gold in health care category of Canada's Safest Employers awards
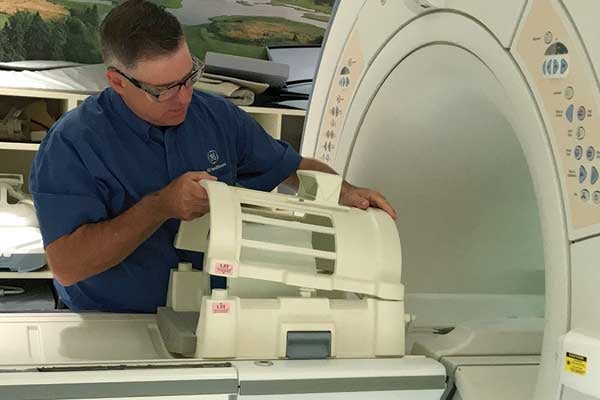
GE Healthcare has found ways to take safety to field workers all across the country. The Mississauga, Ont.-based company sells and services equipment to hospitals. About 200 of its 500 employees are field workers, working from their own homes and travelling alone to hospitals. The field workers who install and service equipment face electrical, radiation and chemical hazards.
“Making sure they have everything they need to work safely, getting the information and the tools to them, when they’re scattered all over the country is a challenge,” says Paul Desiri, director, environment, health and safety.
One way the company meets this challenge is by having local managers conduct regular safety inspections in person with field service representatives. The manager inspection checklist covers site safety, safety risk assessments review, training, personal protective equipment, emergency preparedness, vehicle inspection and chemical management and other safety areas.
“The managers are the ones who are out there; they are the eyes and ears of safety. So we train them to do the inspections and have them do them. It’s very effective that way,” he says, adding that this also creates an opportunity for a manager to discuss safety one-to-one with field workers.
Inspection results are categorized according to severity, and corrective actions are identified to address gaps. These gaps are entered in the online EHS management system, so they can be tracked to closure.
GE employees are encouraged to report all EHS concerns and suggestions. For serious issues, employees are required to take their concern immediately to their direct manager for quick resolution or to stop work.
A common root cause of incidents, Desiri says, is that a safety measure is missing. A worker may notice it but, wanting just to finish a job, says nothing.
“What we’re telling people is, if you see a safety measure is missing, call someone. We will be all over it until it’s resolved. But don’t go ahead.”
The company acknowledges workers who report safety omissions.
“We put it in front of the whole team and say, ‘Look what Joe reported.’ Just to highlight how important it is,” he says. “We’re seeing more of these reports, so it’s starting to take hold.”
During the past year, the safety team has also improved the way it delivers EHS resources to field workers by revamping the intranet site. After consulting with workers, GE Healthcare created a format that’s searchable, usable on smartphones and organized for workers’ needs.
GE Healthcare trains workers in different parts of the country to be “safety champions.” These champions, who have extra EHS training, act as the go-to person in their region. When remote workers have a safety issue, they go to their safety champion first, knowing that that co-worker has expertise both in the job and in safety.
Due to the amount of time field workers spend driving, the company focuses on driver training. Workers who drive must complete a safety risk assessment; higher-risk drivers take practical defensive driving courses. The safety team regularly communicates driving hazards and reminds workers of the importance of planning trips and stopping for breaks.
GE Healthcare encourages employees to participate in its EHS teams, which include teams for ergonomics, lockout tagout verification and automobile accidents. Last year, almost one-half of the field workforce joined a health and safety team or project.
“What makes EHS succeed is participation,” Desiri says. “When people are actively participating and contributing, the safety program will succeed.”