Company wins gold in health care category of Canada's Safest Employers awards
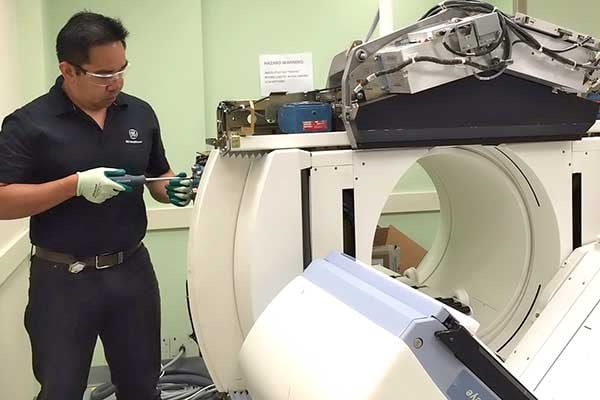
Installing and maintaining medical equipment can be hazardous to your health. Hospitals, in particular, pose unique challenges to GE Healthcare field service engineers, who can encounter radiation, blood-borne pathogens and electrical issues. Usually working alone, they are under constant pressure to keep in mind the customer and the patient who might be depending on the equipment for treatment — perhaps even a life-saving procedure. At the same time, they must look out for their own well-being.
If a situation threatens the health or safety of GE Healthcare’s field workers, hospital employees or patients, the company expects 100 per cent compliance with safety rules and regulations — and does not penalize employees for halting work to address the issue.
“We constantly emphasize the importance of working safely and never taking shortcuts that might harm someone,” says Paul Desiri, director of environment, health and safety at GE Healthcare in Mississauga, Ont. “We strongly encourage filing concern reports and give awards for submitting good ones.”
Desiri points out that the company’s commitment to simplifying the reporting process has made it easier to follow procedures and access critical information from anywhere. Digital tools and a cloud-based content collaboration platform put data at employees’ fingertips.
“Everyone carries an iPhone and just needs to click to get whatever they need from the system,” Desiri says.
One of GE Healthcare’s focuses this year has been to ingrain in employees a “stop-work culture” that begins with “think before you work.” This means that if something doesn’t look right, workers should pause to consider the consequences of resolving the problem on their own and, if necessary, reach out to the resources at their disposal. These include local champions who “own” 13 safety elements and 30 sub-elements, such as motor vehicle safety, lock-out/tag-out and ergonomics.
“The ergonomics champion, for example, is the go-to-person in the field for any concerns in that area,” says Rhonda Wnek, radiation safety leader, explaining that champions tend to be in the field. “So everyone owns safety, not just EHS people.”
Wnek reports that quarterly calls with all 570 employees are an effective tactic for keeping them engaged. In the calls, they learn about program changes, incidents and performance and are encouraged to ask questions and offer suggestions.
“We also look outside our own walls for best practices and lessons learned from other parts of our company or the industry,” says Wnek.
One of these is the “10 factors of risk tolerance” — the willingness of a worker or a group to take safety risks — that can have an impact on safety.
As the challenges to sustaining an excellent safety program increase, getting work done in the field has become more difficult. Among the biggest issues are ever-changing rules: by customers, GE itself and legislation. However, years of solid safety performance and a good supporting culture keeps things grounded. Since 2006, GE Healthcare has gone more than 12 million hours without a lost-time injury.
Desiri says the key to maintaining a top safety record is to never get complacent.
“You must constantly look for ways to improve and keep employees interested,” he says. “We continually tell them that just because nothing has happened in a long time doesn’t mean nothing will.”
This article originally appeared in the October/November 2017 issue of COS.