Honeywell has announced a simple, cost-effective way for companies to improve...
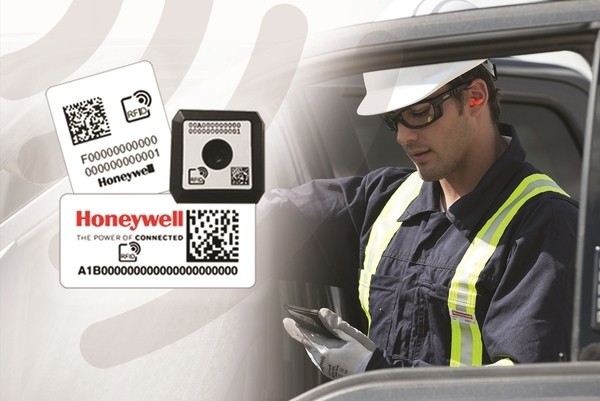
This new Connected Worker solution uses Honeywell’s ultra-high frequency radio identification (RFID) tags that can be attached to any safety equipment and are designed to withstand the tough conditions characteristic of many commercial work sites. The tags can be scanned directly into Honeywell Safety Suite software, which means equipment can be tracked for usage, maintenance and training, resulting in better, money-saving inventory management decisions and compliance reporting, the company says.
“Our newest Connected Worker offering allows customers to connect virtually any piece of personal protective equipment — hard hats, fall protection gear, gloves, ladders, fire extinguishers — and track the equipment with Honeywell’s cloud-based software,” said John Romano, vice-president and general manager of high risk safety for Honeywell. “This cost-effective tracking solution leverages Honeywell’s Safety Suite software to extend connectivity to a company’s entire ecosystem of safety equipment to drive more productivity for safety managers.”
Three types of tags are available to cover the broadest range of worker tools, safety devices and personal protective equipment: a tag that adheres to various flat, non-metallic surfaces; one that can be mounted to metallic surfaces; and a sealed, rigid RFID tag that can be attached even to devices with irregular or odd-sized surfaces.
When equipment is scanned into Honeywell Safety Suite, safety managers can track and manage their inventory of PPE, making sure it is tested on schedule or repaired or replaced as needed, reducing the frequency of equipment failure or non-compliance. The data pulled from the tag can be compiled automatically into reports, thus eliminating time-consuming manual audits and data logs. The ultra-high frequency RFID tags also enable longer-range scans, helping speed up and simplify scanning of multiple devices and workers.