Walter Surface Technologiespie3dian3 new Surfox weld electro-cleaning system helps create a...
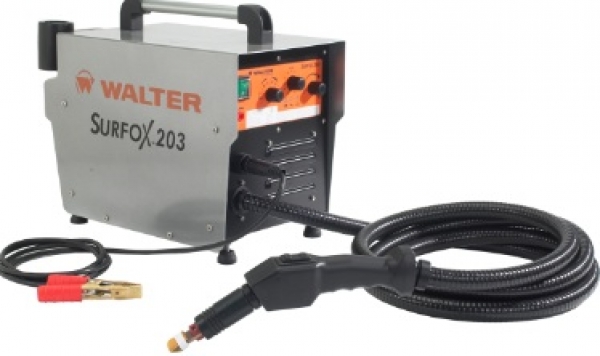
Walter Surface Technologies' new Surfox weld electro-cleaning system helps create a cleaner, healthier and safer industrial work environment. Welding stainless steel often leaves heat discolouration (blueing) on the finished surface, and metal fabricators are facing increased demand for stainless steel that has a clean, fully passivated surface for a wide range of industries, such as food and beverage, pharmaceutical, architectural and transportation. To satisfy customer demand, metal workers must remove these discolourations, but traditional cleaning methods that use pickling paste or grinding machines have high environmental impact and labour costs. Walter’s Surfox system cleans stainless steel without toxic pickling pastes, saves time for workers, and is easy to use, the company said. In a typical application using the Surfox system, the worker fills the cleaning unit with an electrolyte cleaning solution. When switched on, the unit pumps the solution through an application pad, which simultaneously cleans and passivates the part. After the electro-cleaning process, the worker applies a neutralizing fluid to remove acid deposits. The improved Surfox system features a new application pad, which is four times more conductive than the previous one, and can clean surfaces at rates of three to six feet per minute. The controlled dispersion of the cleaning fluid also prevents waste. The result is a flawless finish on stainless steel — with Surfox, even a mirror-like finish on chrome is possible, the company said. Surfox system is NSF-certified for use in the food industry, accepted for use in food plants in Canada and ASTM-A967 / ASTM-A380 certified for chemical passivation on stainless steel.
www.walter.com
www.walter.com