To understand and improve the way our organizations work, we need to start thinking “systems”
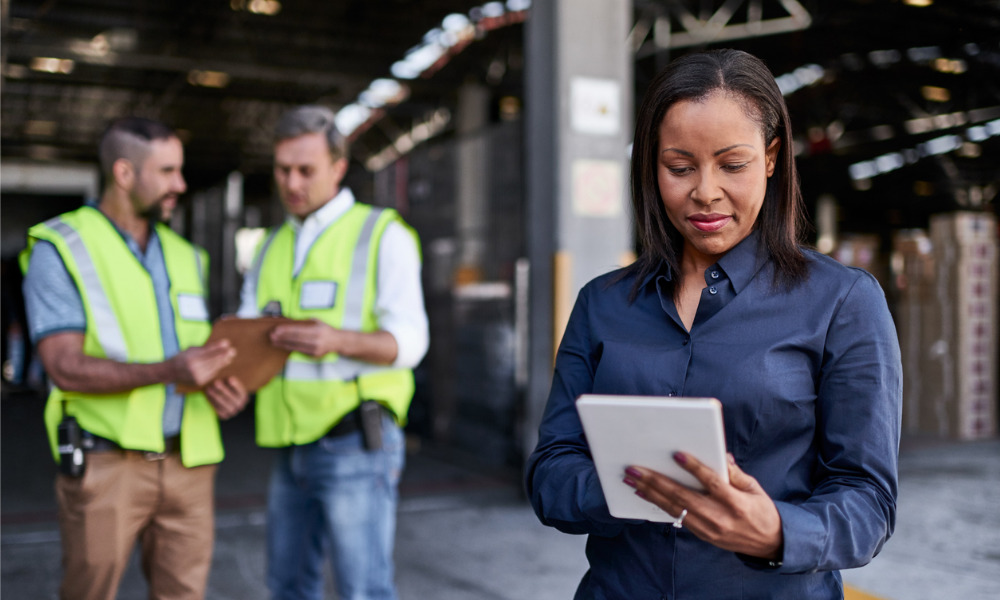
To understand and improve the way our organizations work, we need to start thinking “systems”. If we are ever to reduce risk, achieve zero fatalities, and zero disabling incidents the safety community as a whole, needs to move to systems thinking. We need to start learning about systems thinking and our universities need to start teaching it. Systems thinking means considering the interactions between all the parts of the system (human, legal, technical, information, economic and organizational) in light of organization’s goals.
Workplace safety and safe production operate as complicated systems, rather than simple cause-effect relationships. Understanding how these systems work and are interconnected is the key to understanding why minor faults in each can manifest themselves and result in major incidents that seem to keep happening. When a serious incident happens the corporate focus turns to the investigation to find out what happened with the view to making changes to prevent re-occurrence. Post-incident people tend to view their OHSMS and its dynamics as having little or no order but in reality there is a hugely complex underlying order. If we look beyond blaming the worker for doing something he wasn’t supposed to do, or failing to do something he was supposed to, we will get closer to finding the systems cause of the incident.
Most incident investigation processes focus on analysis, which is the dissection of complexity into smaller and more manageable components. Inevitably the corrective action indicated post-investigation is a review and update of the standard operating procedure (SOP) that was not followed or re-training of a group of employees who do the jobs and tasks described in the SOP. While this may be helpful in the short view of things, it falls short of systems thinking. The reality is that the whole system is dynamic and complex. What we need is not analysis but synthesis, which is about understanding the whole and the parts at the same time, along with the relationships and the dynamic connections between the parts. Synthesis is the ability to see connectedness. Problems never exist in isolation they are always surrounded by other problems. In using systems thinking to fix the problems identified as part of the incident investigation we will inevitably be solving other related problems we may not have even recognized.
Systems thinking involves considering all the systems that were deficient or faulty such that the incident was allowed to happen. These include the HR system used to hire employees, the onboarding and orientation system, the support and supervisory system, the employee competency development and assessment system, equipment selection and maintenance, supervisor and management training, safety leadership development, and others. Systems thinking is a way of helping a person to view all systems from a broad perspective and seeing the overall structures, patterns, and cycles in systems, rather than seeing only specific events.
The connectedness of the systems creates feedback loops, some of which are reinforcing, and some are balancing. Understanding feedback looks leads to gaining a better perspective on causality, how one thing results in another in a dynamic and constantly evolving system. Causality needs to be about being able to decipher the way things influence each other in a system. Taking a systems thinking approach will eventually lead to systems mapping where we map the elements of things within a system to determine how they interconnect, relate, and act in the complex and evolving system. Workplace incident are a result of defects in how the systems work. Understanding how systems work, and how to intervene in them, is key to producing the changes you seek. The goal here is to be able to develop real interventions, shifts in policy and procedure that will be dramatic in the change it brings.
By focusing on the entire system the safety professional can attempt to identify solutions, or leverage points, that address as many problems as possible in the system. The positive effect of this is that it will leverage improvements throughout the system. This priority on the entire system and its leverage points is called whole systems thinking.
Want to learn more about systems thinking? Google Donella Meadows, systems thinking
Glyn Jones is a partner at EHS Partnerships Ltd. in Calgary. He is a consulting occupational health and safety professional with 35 years of experience. He also provides program design and instructional support to the University of New Brunswick’s OHS and Leadership Development certificate programs. He can be reached at [email protected] or you can follow him on Twitter at glynjones_ehsp.