'In a profession dedicated to preventing harm to people, we are often loath to explain the hard truths such as there is no zero risk'
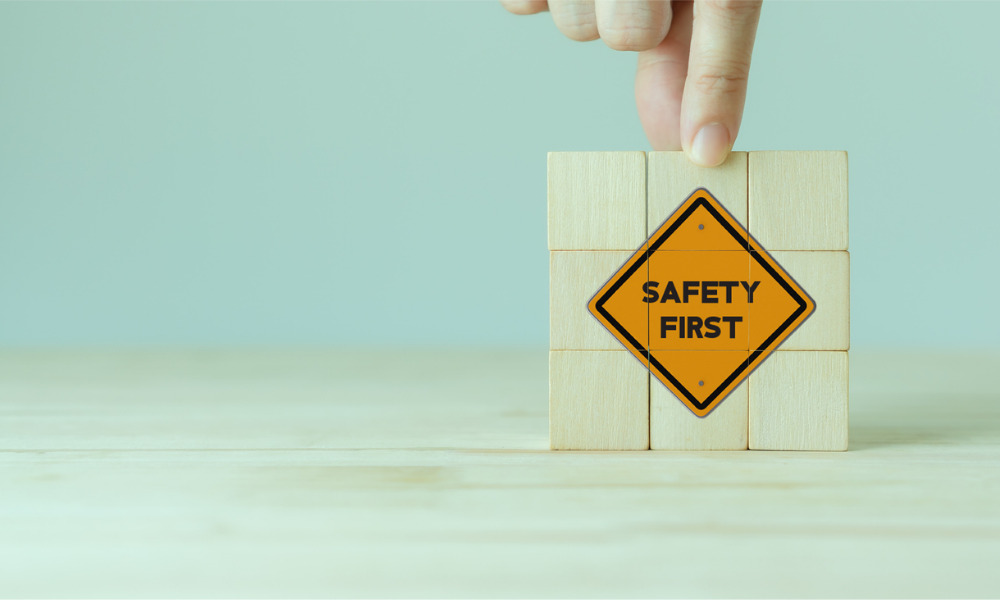
We have all heard the call to arms. Safety must be improved!
This typically happens after a string of incidents or a poor showing over the year or on a specific project. It is usually linked to injuries. Sometimes it is the number of vehicle or environmental incidents. It can even be near misses. However, it is usually the injury rate (TRIR).
Whatever the reason, senior management's call comes down that safety must be improved. It is here that things start to get a bit ironic.
In a profession dedicated to preventing harm to people, we are often loath to explain the hard truths such as there is no zero risk or the TRIR is statistically meaningless. How can we explain that we do not own the results? Who would care anyway when improvements have been ordered?
After several minutes of intensive analysis and self-survey, the decision is usually made to do more. More inspections, more observations, more training, and more meetings. We may even have a standdown – a great reset that will make everything better.
Now, doing more certainly looks good. Doing nothing is certainly not an option. More attention is paid to safety, which can drive improvements. However, this is not an article about the Hawthorne or observer effect. It is about the "more" we do to "improve" safety.
I have written previously about how doing more may not be the best idea. For example, retraining workers who have had an incident are repeating the same process that was not successful in the first place.
Get the basics right
People sometimes ask me what the key to great performance is. My answer is simple. Ensure you have the basics in place, and that they are working.
Not exciting or insightful, but very true.
People have been building safety programs for a hundred years and scratching their heads when things go awry. We have learned during that time. We have learned that the basics do work. We have also learned that a safety program or system is a sandcastle on a beach. It is constantly being eroded and needs maintenance.
Doing more inspections when the process is ineffective and will garner no actual results other than the blizzard of paper. Speaking of depriving woodland creatures of a habitat, there are also observations – another tool in the prevention toolbox.
What is the (improvement) goal?
Those who wave their hand and declare safety must improve usually have no idea what that looks like. Neither do the safety practitioners. Do we know what we are being asked to do?
Promising a lower incident of injury rate is a cop-out. The first step to solving any problem is understanding what the problem is. Doing more of what did not work to prevent the incidents in question is like increasing pumping in a sinking boat without knowing where the water is going.
Read next: Boat safety equipment for small commercial vessels: an essential checklist
Analysis
Analysis is not always a solo activity. Analysis is about making the holes in our Swiss cheese smaller or closing them entirely. The real trick is knowing what barrier (or piece of cheese) you are targeting. A system approach is needed.
In slightly more enlightened employers, an incident review committee meets once or twice a year to review incidents and ensure that the investigations were done properly. This group also looks at the causes and circumstances of the incidents, looking for links or commonalities.
This helps target efforts. Revisiting incidents can lead to some interesting and useful insights. The information is there. You simply have to dig it out.
Health and safety practitioners are always asking for reports. If you want real data, you actually have to go out and get it. If your inspection or observation process is not providing any useful data, then the process is not working all that well.
The basics do work, not perfectly though. They have their limits. The question is are they working now? Has your sandcastle eroded unnoticed? Is your system forgotten words on a page?
When targeting improvements, doing more is not the answer. Knowing what you are doing and why – understanding the goal, the plan, and the expected outcome is more powerful than piling up handouts and inspections.
Act with purpose
Flailing about with more meetings and inspections makes it look like something is happening. Doing something simply because it might yield results is a waste of resources.
A not-so-old saying is that a zero target with zero plan, multiplied by zero clue, equals zero results.
Using insights into the occurrences or incidents can improve safety if improvement means system resilience has improved and the effectiveness of the processes has been enhanced.
Manage the expectations
Improving safety does not mean that the workplace is perfectly risk-free. It never can be. The fact is that incidents will occur. Commonly a certain level of risk is accepted and tolerated by organizations. That can lead to incidents.
The health and safety system is there to prevent incidents. However, it is also there to mitigate the effect when they do happen. It can make a major injury a minor one, and catastrophic failure can become a short interruption. Health and safety practitioners provide the tools to work safely in a collaborative effort. Those tools should ideally, work.
Senior management expects thoughtful analysis and targeted action. Doing more and putting on a show that consumes resources and places a large focus on safety briefly can garner short-term results. But those results do not rely on what is being done – only on the focus.
Without a good understanding and plan, the risk is regression to the state that led to the call for improvement. It can also lead to doing more but not solving the existing problem(s).
More is not more
Doing more can seriously harm the credibility of the safety function. Particularly when the "new" initiatives are seen as short-lived and reactionary by the workforce. More of what allowed a failure is not an improvement – just more.