Link proactive data to individual performance assessment
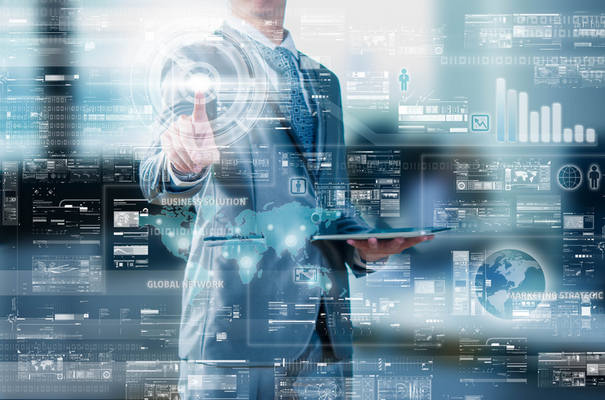
We are awash in data. We have so much data that we even call it “big data.” But which data should we use for decision-making in safety? Lagging performance indicators or leading performance indicators? Lagging performance indicators are a measure of what happened in the past, such as the fatality rate, lost-time injury rate, total recordable incident frequency and workers’ compensation claim rate. Leading performance indicators tell of a future where the safety performance that is desired can be achieved.
While lagging indicators do have value for highlighting opportunities for improvement, what is needed is a set of leading indicator measures — related to real safety performance — that result in change.
A program that includes appropriate leading indicators can steer performance of occupational health, safety and overall employee well-being. These measures should be simple, available, well-defined, relevant, meaningful, easy to collect, time sensitive and they should allow for data driven analyses, such as trend analysis for intra-departmental/location comparisons and inter-department/location comparisons.
Useful, proactive leading performance indicators can be obtained from simple activities, such as measuring completion of workplace inspections, near-miss investigations, hazard assessments and tailgate meetings.
As the safety culture grows and advances, additional indicators that may be used to measure safety culture development may include measuring the extent to which the health and safety policy has been effectively communicated, whether health and safety plans and goals have been established, the frequency of senior leadership communication with front-line employee teams and employees’ understanding and inclusion of health hazards and ergonomic hazards in their hazard assessment processes. We can do even better if we consider a few high powered leading indicators, such as the percentage of toolbox tasks that consider health and ergonomic hazards in the immediate workplace, the number of job observations completed and feedback presented to work teams, the number of senior leadership site visits and facilities tours to review and discuss safety performance as well as front-line employee education, training and involvement in workplace inspections and incident investigations.
Most importantly, safety professionals need to focus on leading indicators that can be correlated to the lagging indicator outcomes that we seek to achieve. If zero harm is our goal, then we need to determine what leading indicators are best correlated with this outcome. The challenge is there is a lag time between the implementation of the leading indicator activity and a change in behaviour and then performance such that the lagging indicator outcome is achieved. This takes time. This requires safety professionals create a list of significant leading indicators and sequentially implement them for a period of, say, a year or two and then assess the resulting lagging indicator outcomes. If we don’t see the improvement we were looking for, we need to go back to the drawing board and make the necessary enhancements to our program of intervention.
If you are a safety practitioner who is relatively new in the role and reporting into the corporate safety group or to an operations leader, you might like to focus on improving the quality of a couple of safety processes that are leading indicators for improvement. For example, you could review the new hire onboarding process to see if it includes introducing new employees to all hazards associated with their jobs. If this element needs to be improved, volunteer to support human resources (HR) in improving this aspect of onboarding.
Hazard recognition is key to front-line employees effectively assessing workplace hazards before work starts. This is a leading indicator for safety improvement. Review the current task hazard assessment or job safety analysis processes to assess the quality. If improvement can be made, volunteer to help during the scheduled review of these and take this opportunity to provide some specific technical input and support. If field-level hazard assessments are completed at the start of work, review the quality of the submissions for the past month. If the quality could be improved, volunteer to sit in on the pre-shift meetings when these are completed and help the work crew improve the quality. If need be, plan to do some of the hard work associated with making quality improvements.
If you are an experienced safety professional reporting to the senior leadership team, your focus needs to be on expanding the conversation about the use of leading indicators to drive safety improvement. The goal needs to be on linking safety leading indicators to individual performance assessment and if possible, link these outcomes to performance incentives, such as the annual bonus. Talk with the vice-president of operations or HR and see if you can participate in the annual corporate strategic planning process. This is the best opportunity to introduce leading indicators for safety performance onto the company’s key performance indicator dashboard. Suggest that they measure participation of all senior and mid-level managers in leading day-to-day safety functions, such as workplace inspections, toolbox meetings, incident investigations and job observations. If each employee has objectives linked to these activities, the outcomes you want to achieve will become much easier. When leading indicators are set as business goals, safety improvement is possible.
This article originally appeared in the June/July 2017 issue of COS.