The experts at Kee Safety outline fall prevention fundamentals to help safety managers achieve compliant worksite environments
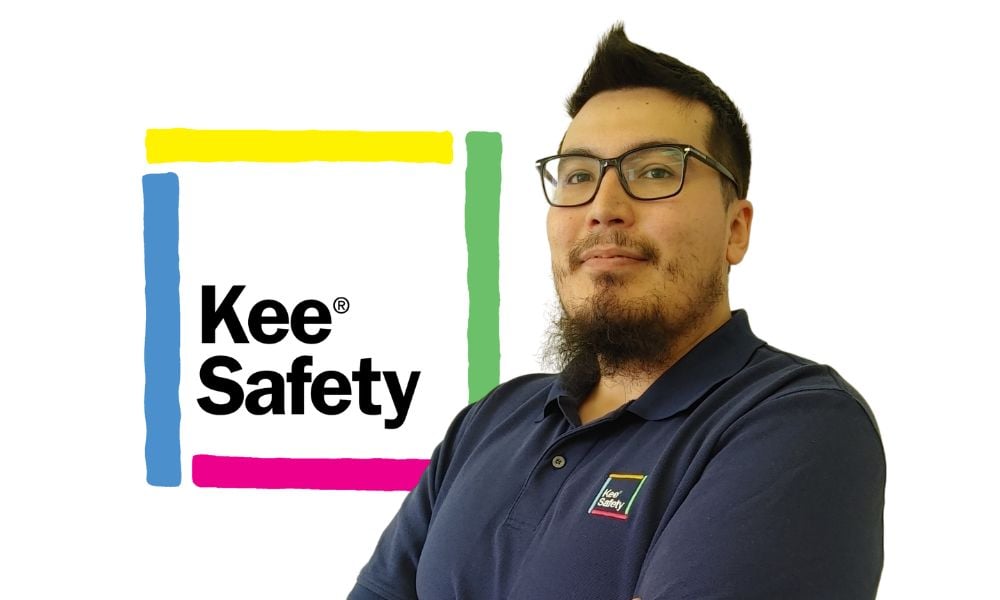
This article was produced in partnership with Kee Safety.
Falls are the leading cause of preventable injuries and preventable deaths by injury in Canada. According to data from the nation’s public health partner and information resource Parachute, falls accounted for $10.3 billion in costs to the Canadian economy in 2018.
“While falls are a common and preventable injury for the layperson, the potential for falls at worksite environments increases significantly,” says Nicholas Bixcul, strategic solutions manager, Kee Safety. “Our number one goal is to separate people from hazards, and we have a detailed hierarchy of fall protection protocols in place to solve for these challenges.”
The Association of Workers’ Compensation Boards of Canada report 43,435 claims associated with workplace falls were remitted in 2020. Sixty-two of these injuries resulted in death. In the same year, claims from manufacturing and construction industries amounted to 32,380 and 23,682 respectively, making them the country’s second and third highest ranking sectors for lost time due to these types of injuries.
Worksite regulations
Federal and provincial workplace regulations, codes, and acts must be followed by Canadian employers to mitigate injury and litigation. Sections 12.01 – 12.09 of Canadian Occupational Safety and Health Regulations SOR/86-304, for example, require fall protection systems be in place for work involving structures, vehicles, or ladders that are three meters (3m) off the ground, or higher. These laws also apply to equipment under 3m high if the surfaces onto which an individual could fall present greater risk of injury than a solid, flat surface.
It is the facility safety manager’s job to identify and address these potential hazards and implement appropriate safety solutions.
“In my experience, most people aren’t aware of OH & S requirements and other regulatory bodies in Canada because these organizations are notoriously unclear about what needs to be protected, when, and how,” says Bixcul. “When we partner with clients, we look at each specific task, and we like to speak with all stakeholders throughout the process so that all elements of the job are noted and addressed,” he explains.
Worksite safety concerns
Industrial work that includes rooftop access poses considerable risk if edges are unprotected; self-closing gates are not part of transition points between ladders and roofs; roof hatches are not protected by safety railings and self-closing gates; and/or skylights are not protected by railings and screens.
Piping, ductwork, and changes in roof and ground levels can present trip hazards if not protected and highlighted by “step over” platforms. To prevent falls from stairways, mezzanines, machinery, loading docks and ground level hazards, safety railing systems must be implemented.
Temporary jobs that involve machinery and equipment relocation, building expansions, or building installations require modular railing systems made of strong, durable pipe fittings that allow for flexible configurations.
“I find when speaking to safety managers many are aware of certain aspects of the codes but they’re not aware of the many different elements that can apply to a fall protection system,” says Bixcul. “We help companies see and understand all the different aspects involved in regulation compliance and in creating a safe working environment.”
Worksite safety solutions
Kee Safety is a leading fall protection company and a global supplier of safe access products, services, and training. The company engineers, manufactures, and installs fall protection equipment that is third-party tested and compliant with regulatory standards throughout North America and around the world. They work with clients across a range of sectors that include aviation, education, manufacturing, transportation, warehousing, construction, and more.
To help clients understand where fall hazards exist, Kee Safety offers comprehensive workplace hazard assessment surveys and customized compliance plans rooted in OH & S and Canadian Centre for Occupational Health and Safety (CCOHS) regulations. Surveys can be conducted at single sites, multi-facility sites, or by satellite imaging for contactless service.
During these assessments, safety specialists perform critical analyses of work environments. Clients then receive a complete review of their workplace layouts, detailed installation drawings, technical advice, and compliant safety plans that can include safety rails, roof guardrails, lifelines, roof anchors, and safe access platforms and walkways. Clients are also provided with expert guidance and direction from project concept to completion.
“At Kee Safety, our motto is “separating people from hazards.” This should be everyone’s mission because nobody wants a colleague to be injured on the job,” says Bixcul. “We take all the necessary steps to help our clients create the safest worksites possible.”