Why firm is spearheading a shift in construction to Type 2 hardhats
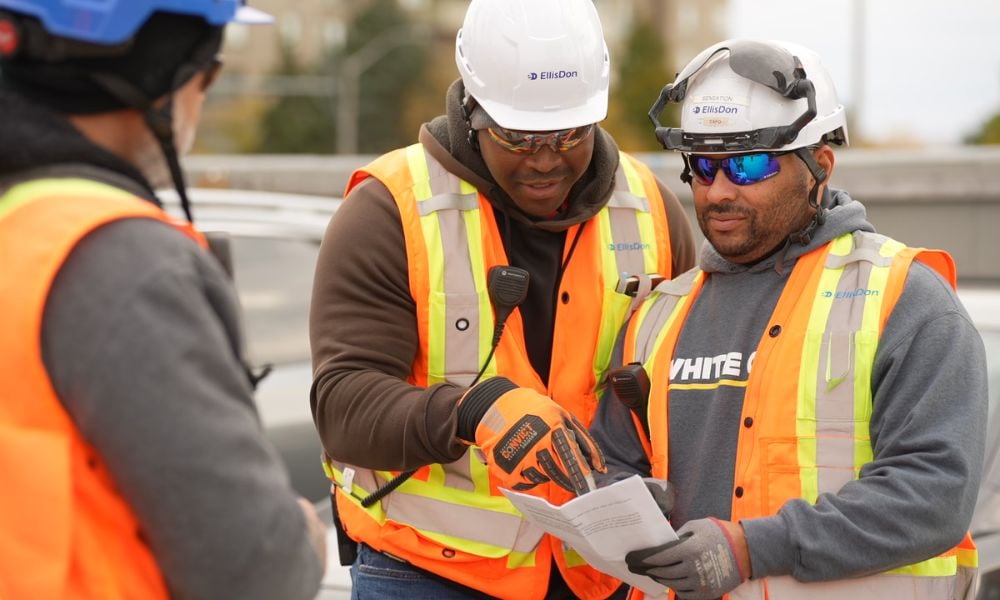
"If a worker is wearing a good quality hard hat and his hard hat hits the ground instead of his head, then the forces on his head will be a lot less than 1,500 joules," says John Martin, Eastern Director of Health, Safety and Environment at EllisDon. “Therefore, it’s highly unlikely that you’ll have a serious injury or fatality on your hands.”
That principle underpins EllisDon’s company-wide transition from Type 1 to Type 2 Class E hardhats with integrated chin straps—a move the construction giant undertakes ahead of any regulatory requirement. While current Ontario regulations mandate only Type 1 hardhats, EllisDon sees the shift to higher-performance helmets as essential to reducing serious injuries and fatalities.
Why EllisDon is leading a shift
EllisDon’s decision stems from findings by the Construction Safety Research Alliance (CSRA), based at the University of Colorado, which the company joined over a year ago. The alliance focuses on energy-based safety, evaluating the forces behind workplace injuries.
“What we've learned is that all injuries are a result of an undesired contact between an energy source and a person,” Martin explains. “At about 1,500 joules, you will most certainly suffer a serious injury or fatality.”
Because most falls or impacts do not occur vertically—rendering top-only protection insufficient—Type 2 helmets, which offer lateral protection from front, back, and side impacts, provide a crucial safety upgrade. The integrated chin strap ensures the helmet stays in place during falls or collisions.
How the Transition Unfolds
EllisDon begins by outfitting all employees with Type 2 helmets, selecting the Milwaukee Bolt system as their primary model, though they also acknowledge other manufacturers like STUDSON, 3M and Dynamic.
The initiative gains momentum without internal resistance. “We didn’t have to convince [leadership],” says Martin. “It was Kieran Hawe, our CEO, who said, ‘let’s go.’ He didn’t want to wait.”
Now, EllisDon turns its attention to subcontractors, many of whom are already voluntarily adopting the new standard. The company leverages its influence within the Canadian Construction Safety Council (CCSC)—a coalition of the 12 largest general contractors in Canada—to promote broader adoption. The CCSC is already working on harmonizing safety efforts across the country, including new standards for fall protection and cut-resistant gloves alongside head protection.
Balancing cost and ROI
Martin acknowledges the higher cost of Type 2 helmets compared to basic Type 1 models but sees it as a wise investment.
“From a return on investment standpoint, I think the savings in claims from head injuries far outweigh the cost of the hard hat,” he says. “But even more importantly, we’re protecting our workers. Without our workers, we have nothing.”
Martin encourages other health and safety leaders, especially at smaller firms, to focus on the real-life impact of the change rather than upfront costs.
“There have been incidents with our new helmets where workers have slipped, fallen, hit their head, and there’s been damage on the hard hat,” he says. “That damage would’ve been translated into damage of that individual’s skull. But because they had that hard hat on, they went home to their families that day.”
He also urges firms to partner with manufacturers who actively seek feedback to improve safety gear design. “They want to hear from the workers. What do you need? How can we build safety into our tools and PPE?”
A Broader Safety Culture
Martin sees EllisDon’s effort as part of a growing industry-wide movement. “It’s amazing how many people are involved in worker safety and working towards keeping workers safe, going home to their families every day,” he says.
Martin says EllisDon’s safety team has grown from just 10 people in 2001 to over 100 in Eastern Canada alone today, with a national HSE workforce of around 240.
As he prepares to speak at Steps for Life, a national event organized by Threads of Life in honour of injured workers and their families, Martin reflects on the broader mission: “There are a lot of people actively engaged in making workplaces safer. This isn’t just compliance—it’s about doing the right thing.”