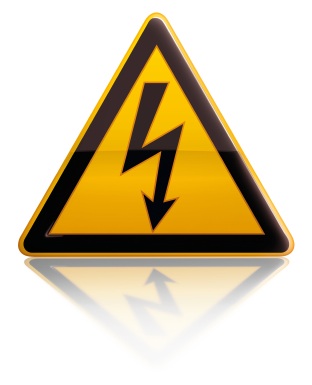
According to statistics compiled by CapSchell Inc, a Chicago-based research and consulting firm that specializes in preventing workplace injuries and deaths, there are five to ten arc-flash explosions that occur in electric equipment every day, resulting in medical treatment.
An arc flash is a breakdown of the air resulting in an arc which can occur where there is sufficient voltage in an electrical system and a path to ground, neutral or another phase. An arc flash with a high level of current, in the range of 1,000 amps or more, can cause substantial damage, fire or injury. The massive energy released in an arcing fault can instantly vaporize metal in the path of the arc, blasting molten metal and expanding plasma outward with extreme force. The result of the violent event can cause destruction of equipment, fire and injury, not only to the worker but also to nearby workers.
With the arc-flash hazard, a product of fault current and time, the engineering approach to minimizing the hazard is to affect the contributing factors. The major factors determining the level of the arc-flash hazard are the amount of arcing current, the time that it flows and the distance of the worker from the arc itself. The first two of these three factors can easily be minimized by the design of the electrical system.
Current-limiting devices
Current-limiting fuses and circuit breakers are often used in the design of electrical distribution systems to protect electrical equipment under high available short-circuit conditions (NEC 110.10). They are able to protect the equipment from the significant thermal damage and magnetic forces associated with high short-circuit currents by actually reducing the current that flows and the time that it flows. Within their current-limiting range, they keep the current from reaching its peak during the first half cycle. And because they can react so quickly, the current is driven to zero in as little as a quarter cycle, or even less.
This great reduction in damaging current and time not only protects equipment from significant short-circuit currents, but naturally also helps protect workers that might be exposed to horrendous arc-flash energies. The difference between a 30,000-ampere arcing fault that lasts for 30 cycles, and a let-through arcing current of 1,000 amperes that lasts for a quarter cycle can be the difference between a worker driving home after work and a ride to the morgue.
In practice, the majority of electrical faults experienced in industrial low-voltage systems are phase-to-ground faults. For solidly grounded wye systems, the IEEE Red Book (Std 141-1993, Section 7.2.4) states that, “A safety hazard exists for solidly grounded systems from the severe flash, arc burning and blast hazard from any phase-to-ground fault.”
The same standard recommends a solution to resolve this issue. Section 7.2.2 of the IEEE Red Book states that when using high resistance grounding, “There is no arc flash hazard, as there is with solidly grounded systems, since the fault current is limited to approximately 5 A.” The Red Book is referring here to phase-to-ground faults.
While high resistance grounding prevents the propagation of many ground faults into full-fledged three-phase arcing faults, high resistance grounding has no affect on the magnitude of a phase-to-phase or three-phase arcing fault once the fault is initiated.
While high resistance grounding as a technology was originally applied to industries as diverse as food processing, mining, petrochemical, and even commercial installations such as airports and data centers to enhance the reliability and uptime of power distribution equipment, it is also proven effective in significantly reducing the frequency and severity of arc-flash accidents. With between 90 per cent and 98 per cent of electrical faults being phase-to-ground faults, limiting the fault current to between 5 amps and 10 amps provides insufficient fault energy for the arc to re-strike. It also self-extinguishes and the hazard frequency is reduced.
Designing safety
Nowadays, high resistance grounding is being used to replace solidly grounded systems for the safety reason noted above, and there are design considerations that must be addressed. Fortunately, modern technology helps incorporate these considerations, making the design process straightforward.
The original high resistance grounding system developed in the 1950s and 1960s worked as intended, but wasn’t able to solve potential safety issues, such as a second ground fault, leaving the ground on the system too long, communications,
additional tools to locate a ground fault and monitoring of the neutral path.
When modern relays are integrated into the high resistance grounding package, these design considerations are easily resolved. The addition of zero-sequence current transformers on each feeder in the main switchgear and a dedicated ground detection system are all that is required.
These can be integrated into new switchgear or retrofitted into existing gear. When a ground fault occurs, the ground relay indicates faulted phase and feeder. This keeps maintenance personnel away from the main switchgear when looking for the ground fault, often allowing him or her to wear lower rated PPE protection. The reason is that personnel will begin looking for the ground fault downstream of main switchgear, where the arc-flash hazard is based on the feeder overcurrent protection device (where arc-flash energies are often lower) and not the main overcurrent protection (where arc-flash energies are often higher).
In addition, the relay has built-in communications to alert personnel if they are not on-site during ground fault. The data logging system will keep track of ground faults until maintenance personnel have a chance to locate the ground fault. This may help associate the ground fault with a faulted piece of equipment by coordinating time/day of ground fault when equipment is running.
There is a concern that the first ground will be left on the system and ignored. Since the zero-sequence current transformers identify the faulted feeder, the relay has the ability to begin a timer (user programmable, usually in hours) when the ground fault first occurs. Unless the ground fault is removed or the timer is reset, the faulted feeder is shunt-tripped offline. The purpose is to continually remind maintenance personnel to either remove the ground fault or to reset the timer every so many hours.
In the event that a second ground fault occurs prior to removing the first ground fault, a phase-to-ground-to-phase or phase-to-phase fault can occur. When this occurs on original high resistance grounded systems, it would cause both feeder circuit breakers and possibly the main circuit breaker to trip. However, the modern relay can be programmed to prevent this and only shunt-trip the lesser priority feeder, leaving the more important feeder online.
A major safety concern is the loss of neutral path, i.e. broken wire from source neutral to resistor or between resistor and ground, or even a bad or loose connection. The result is changing from a high resistive grounded system to either an ungrounded or solidly grounded system without anyone knowing it! This would cause severe safety hazards.
With modern technology, the neutral path from neutral to ground (including resistor) can be continuously monitored for integrity. If an open or short circuit occurs, the relay will alarm.
High resistance grounding systems do not protect against the less frequent but still dangerous phase-to-phase or three-phase arcing faults. However, the combined use of high resistance grounding for protection from ground faults and its ability to prohibit the escalation of the fault, and current-limiting fuses or current-limiting circuit breakers for phase-to-phase and three-phase arcing faults is an effective engineering approach to minimizing the arc-flash hazard.
Andrew Cochran is the president of Mississauga, Ont.-based i-Gard Corporation, a developer and manufacturer of power equipment protection systems. You can reach Andrew at [email protected]