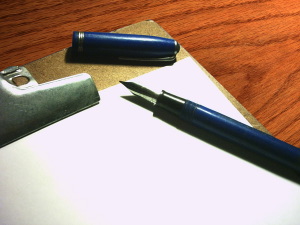
“You usually know, but they can come unannounced,” says Barton, who also runs Noremtech Inc., a radiation protection services consultancy.
Health and safety professionals across Ontario also need to be ready for inspections — especially since the province’s Ministry of Labour has been ramping up its inspection capabilities over the last few years.
What can you do to prepare? Sources offer three main tips:
• Get employees involved in the safety plan.
• Take a holistic approach.
• Read up to stay ahead.
Employee involvement
Nearly every biology, physics and life sciences program at Carleton uses radioactive liquids for things like labelling and tracing DNA material and proteins, Barton says. So as well as providing radiation safety training, filing annual regulatory reports and escorting CNSC inspectors when they arrive, he also gets employees involved in the safety program.
“In the last few years, I’ve developed an internal compliance checklist, which I get certain users to fill out and send to me every month,” Barton says. “They make sure they have the radiation sign on the door, that their inventory is up to date, and... [that they have] contamination monitoring results,” documenting post-experiment cleanup whereby the users verify that there are no radio isotopes left on work surfaces.
Barton says he first started using the compliance list a few years ago. “It’s just an extra check on them, to make sure they’re compliant.”
And he finds that it does make a difference. “If they haven’t used isotopes in a while, they forget the things that are required for compliance,” he says. “If they’re looking at that checklist every month, it helps.”
Health and safety experts across the province need as much help as they can get these days. Since 2007, Ontario’s Ministry of Labour has been adding more inspectors and targeting specific industries, all in the name of improving the province’s workplace safety record.
In the past few years, the ministry has more than doubled its inspector headcount from 200 to 400-plus, says Carol Sackville-Duyvelshoff, associate director of the occupational health and safety branch. Earlier this year, the ministry added yet another 41.
And in January, the province chose Tony Dean, professor in the School of Public Policy and Governance at the University of Toronto, to lead a panel of safety experts to research new approaches to improving workplace safety. The panel is expected to report to the Ministry of Labour in the fall.
Increased inspections helped reduce Ontario’s lost-time injury rate from 2.2 in 2004 to 1.7 in 2008, Sackville-Duyvelshoff says. So whereas 2.2 workers out of 100 used to be injured on the job, now just 1.7 workers suffer workplace injuries. “The downward trend is still continuing,” she says.
Since that initial inspection surge, the ministry has conducted safety blitzes focusing on particular sectors (construction, for instance) and specific risks, such as electric-shock hazards.
Take a holistic approach
But inspectors don’t wear blinders. If they see problems with other aspects of the workplace – fall-protection issues noticed during an electrical safety inspection, for example – they’ll make a note of it.
“The inspector will look at everything,” Sackville-Duyvelshoff says, advising organizations to keep an open mind and consider all of the safety implications.
In a recent electrical safety inspection blitz, the government found that the most prevalent compliance orders had nothing to do with electricity: fall protection, personal protection equipment, and general duty issues (ensuring employees comply with safety regulations) were the top three concerns, Sackville-Duyvelshoff says. Although she adds that usually the compliance orders do coincide with the focus of the inspection.
Still, it’s a good idea to keep an eye out for any and all safety issues. To do that, the ministry suggests that organizations should work with their workplace safety associations under the Workplace Safety and Insurance Board (WSIB) to conduct risk assessments, to help organizations get a grip on where the issues might be.
The ministry is also producing a series of videos to help organizations understand just what inspectors are looking for. At press time, the government had developed two videos: one on forklift safety, and another on auto repair shop safety. Access the instructional videos via this Web site: http://www.labour.gov.on.ca/english/resources/gallery.php.
Read up to stay ahead
But the ministry’s videos provide just part of the picture. Safety specialists also have to keep up with workplace regulations if they really want to stay ahead of the inspectors, says Mike Gzik, owner of Safety 1st, a health and safety consultancy in Brantford, Ont. offering safety training, mock inspections, audits, and policy development.
“They have to have a copy of the regulations that apply,” Gzik says, noting the basics. “It’s the law.”
Yet he also acknowledges just how difficult it can be to stay abreast of the rules. “Usually the biggest problem is companies have the right idea, but they don’t know where to start.”
Gzik suggests starting at the Ministry of Labour and the WSIB. Download the Ontario Occupational Health and Safety Act from this Web site: http://www.labour.gov.on.ca/english/hs/pubs/ohsa/index.php. Get a copy of the WSIB’s Workwell audit and perform an internal analysis: http://www.wsib.on.ca/wsib/wsibsite.nsf/LookupFiles/DownloadableFileWorkwellAudit/$File/WorkwellAudit.pdf.
Gzik also says it’s important to stay focused. Inspections sometimes cause health and safety professionals to get defensive. But that’s counterproductive. “If the inspector finds something... admit it, and develop a strategy.”
“Look at it as an opportunity for improvement,” he says — although that can be difficult. After all, it’s no cakewalk, hearing that the efforts you’ve already invested in health and safety may have fallen short in one way or another.
Barton says he has seen that from both sides of the fence. A former inspector at the Atomic Energy Control Board — the CNSC’s predecessor — he recalls having to perform the sorts of inspections that he now endures at Carleton.
From his point of view, things have changed.
“The inspectors are less worried about the big picture,” Barton says. “They’re more interested in finding small items to bring back to the supervisor to show how good they are at finding things.”
Nonetheless, Barton says he sees value in the inspections, whether they’re announced or not. Recalling his days as an inspector, he notes: “I noticed that when you did call ahead, you still found plenty of things wrong.”
---------------------
Stefan Dubowski is a freelance writer in Ottawa. You can reach him via e-mail at [email protected].