How to spot signs of disengagement among workers
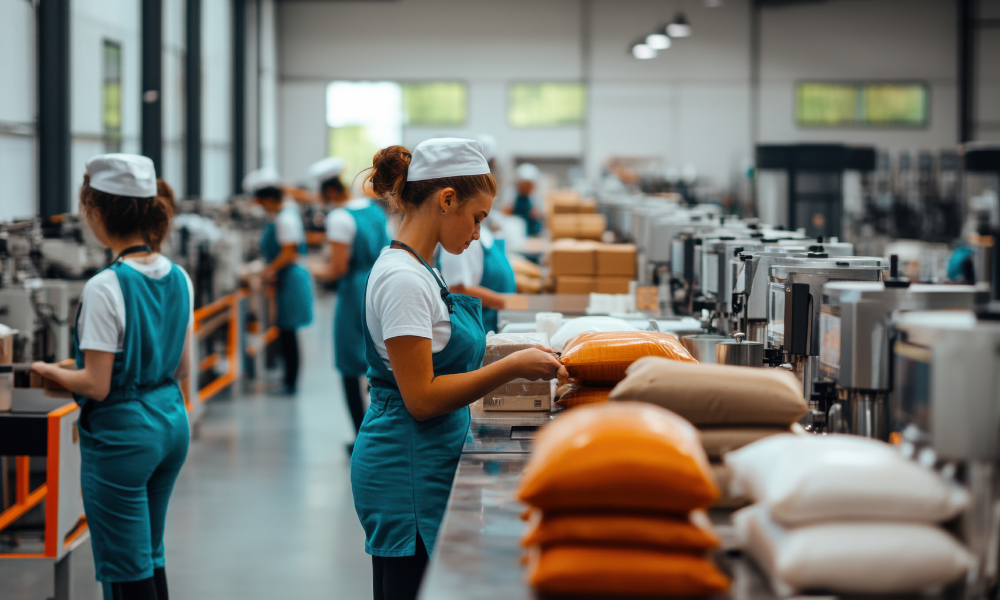
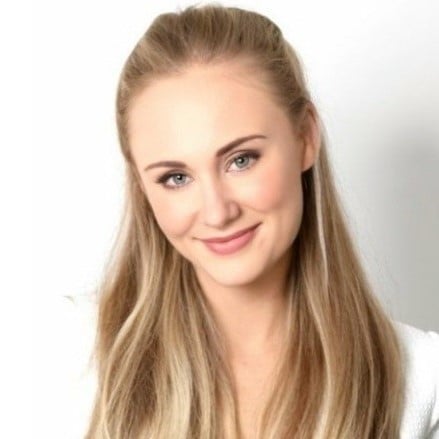
Manufacturing industries are the backbone of so many businesses, as they are responsible for creating and processing different products. Unfortunately, some companies may discover their employee engagement is not on par with what’s required. Utter disinterest can influence several factors like employee health and safety, as well as productivity and company success.
Spotting employee disengagement is a key practice that supervisors and leaders must know. While there’s no exact metric or telltale sign, there are multiple business aspects you can reevaluate and mitigate.
Review attendance
Presence is the first step toward productivity, but some manufacturing companies already lack it. About 42% of manufacturing businesses cite absenteeism and labour shortages as one of the biggest bottlenecks in production. Disengaged employees may call in sick or blatantly refuse to go to work. Others also take more frequent breaks or disregard their work hours.
Review the attendance process. You may have to track the hours that employees work. If workers are struggling with their schedules, it’s essential to understand the root of the problem and how you can help them attain a better attendance rate.
Seek initiative
Attitude is also vital when gauging employee engagement. Workers are supposed to be enthusiastic when contributing, so a lack of initiative can be concerning. It’s especially worrying when active team members avoid sharing ideas or collaborating.
Understanding what motivates your team can help you narrow down what would renew their interest in work. You can be proactive by building paths for career advancement and encouraging professional development. Other programs, such as monthly recognitions and feedback mechanisms, can also open up your communication lines to employees.
Track productivity and revenue
Disengagement can get in the way of maintaining workflow. People lose the drive to increase or maintain the quantity of their outputs. Even if they can increase those scores, it’s uncertain whether the quality is the same.
Productivity should bring in earnings, but a lack thereof would result in losses. Only 23% of the global workforce is engaged, which has caused about $8.9 trillion in gross domestic product (GDP) loss. What’s worse is that 15% are actively disengaged, which is why it’s key to work with employees.
Stay vigilant for equipment malfunctions
Monitoring the state of your manufacturing equipment also indicates employee disengagement. When employees aren't focused or active, they pay less attention to the apparatus or misuse them, which leads to malfunctions. These safety hazards risk worker health and safety.
Other repercussions include company revenue and operations. In 2023, an equipment failure at a Nova Scotia salmon farm left the company unable to supply its consumers until 2024. Ensure that the machines are correctly used and maintained by the people assigned.
Check work practice implementation
Employers are partially responsible for the safety of their workers. The Occupational Health and Safety Act requires them to provide training programs and equip them with the right gear to keep them safe. Implementation should go smoothly and have good employee engagement.
However, workers who are less interested may ignore most policies and avoid implementing them. Leaders must be vigilant in tracking work processes and monitoring everyone’s daily practices to uphold workplace safety.
Reigniting employee engagement
Businesses must avoid being complacent regarding employee engagement, as this oversight can create health risks and business complications. Practice early observation and intervention to keep the workplace conducive to employees.