Arc flash is one of the leading causes of injuries and fatalities among electrical workers
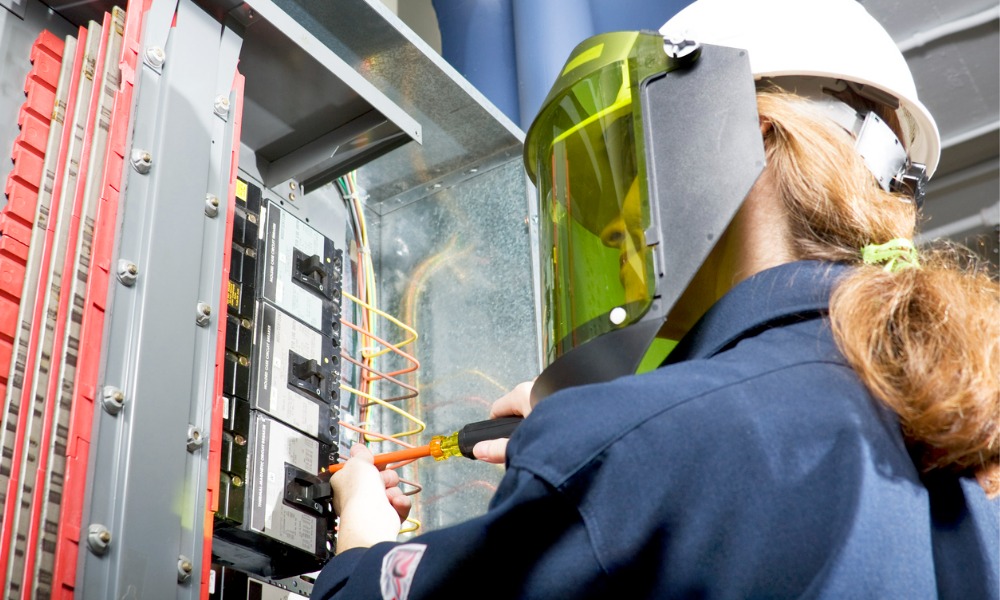
In 2019, O’Connor Electric of Kitchener, ON, was fined $55,000 after three workers received burns from an arc flash while working on an energized electrical system. For those in the electrical sector, this is not a one-off. Arc flash is one of the leading causes of injuries and fatalities among these workers.
Writing for COS, Vawn Himmelsbach said that though many of us are familiar with what an electric shock is, there is far less awareness around arc flash. She says that an arc flash can occur at any time, and can result in severe burns or even death.
So what exactly is an arc flash? “It’s a rapid expansion of air, four times the surface temperature of the sun,” said Mike Doherty of EUSA to COS. “If we’re sitting on the surface of the sun, can you feel the heat? Close your eyes and imagine it four times hotter.”
And though an arc flash happens extremely quickly (usually in one-sixteenth of a second, it can still ignite clothes and burn skin in that time. As opposed to an electric shock which is always as a result of direct contact, an arc flash doesn’t require contact. Himmelsbach said that “It’s a sudden release of electrical energy through the air – like a conducting plasma fireball – that can result in severe burns and even death.”
And burns aren’t the only issue. Himmelsbach says that infrared and UV from the flash can impact the issues, and the sound of an arc flash (the decibels are “way off the charts”) can deafen a worker. As well, when an arc flash explodes, workers can also be exposed to noxious gasses such as copper vapour.
So how can employers and safety practitioners keep workers safe from arc flash hazards?
Do a risk assessment. First of all, qualified engineers or technicians should perform a CSA Z462-compliant arc flash hazard analysis to determine to figure out potential arc flash incident energies and boundaries, shock hazard boundaries and what PPE is required.
Have the proper signage. Plant engineering and maintenance expert Robert Burgess wrote for COS that warning labels identifying potential hazards and required safety equipment should be affixed to all applicable equipment. In fact, the Canadian Electrical Code (CEC) mandates that “electrical equipment shall be field-marked to warn persons of potential electrical shock and arc flash hazards.”
Provide workers with the right PPE. “The first step is to review your electrical panels and components to calculate the risk and required level of worker protection,” said Steve Craig in a COS column. He says that typically workers should be wearing fire-retardant long-sleeved shirts and pants, or coveralls. Other required PPE would include a hard hat, hearing protection, an arc-rated face shield and a stocking hood or switching hood. Gloves would also be required.
Do regular maintenance. Burgess says that weaknesses and hazards can be detected through regular maintenance of equipment. He also says that “analysis of electrical insulating fluids, helps to reduce production downtime and associated costs, but most importantly, improves safety conditions for system operating personnel.”