How a dedicated team achieved remarkable safety milestones
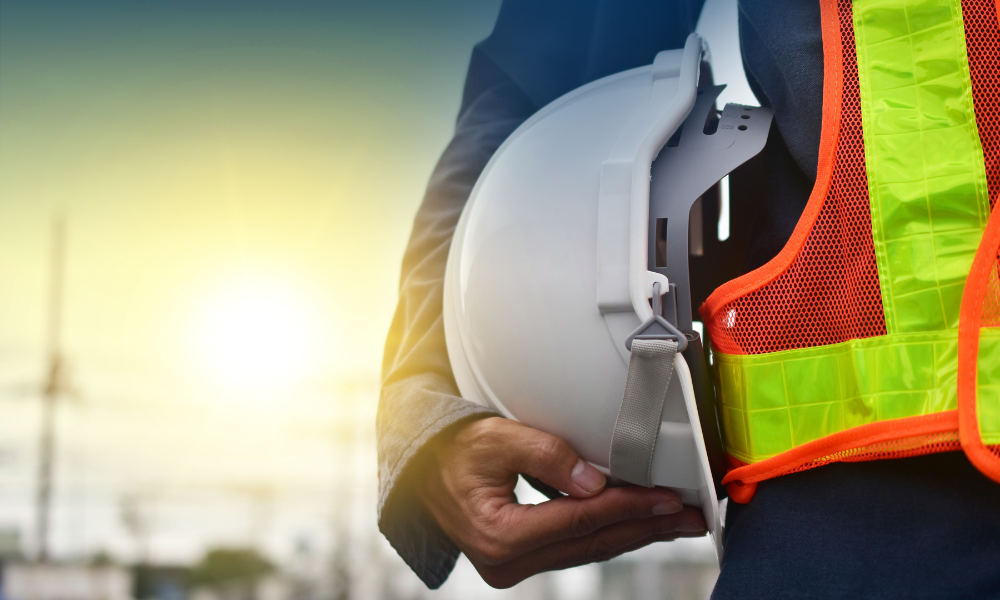
Carmichael Engineering, a Canadian leader in thermal system technologies, has long been known for its technical expertise and preventative maintenance solutions. In 2024, the company made headlines for a different reason: a remarkable reduction in workplace injuries.
Under the leadership of Sukhi Dhillon, Senior Director of Environment, Health, Safety, and Quality, Carmichael reduced its lost-time injury rate (LTIR) by 52 percent and its total recordable incident rate (TRIR) by 46 percent.
“These results didn’t happen by chance,” Dhillon explains. “They’re the outcome of a focused, collective effort that involved every level of the organization.”
When Sukhi Dhillon joined Carmichael in January 2023, she stepped into a role that offered something rare: the autonomy to design a safety program from the ground up. It was an opportunity to move beyond following established systems and instead create one that matched Carmichael’s needs and ambitions.
“This was the first time I was given full control to develop a department based on my own vision,” Dhillon says. That vision was clear: build a collaborative safety culture where accountability extends beyond the confines of a single department. With a workforce of over 800 employees operating out of 23 regional service centers, the challenge was as much about scaling safety initiatives as it was about creating effective ones.
Building a unified safety culture
Dhillon attributes the progress to a collective effort. “The leadership team made safety a priority, allocating the resources and funding necessary to build a capable team,” she explains. What began as a one-person department quickly grew into a team of seven, bolstered by a shared commitment from executives, middle management, and field staff alike.
The foundation of Carmichael’s safety strategy is its Internal Responsibility System, which embeds safety into every level of the company. Employees across roles from technicians in the field to executives in the boardroom—are expected to take ownership of safety outcomes. This approach, Dhillon says, fosters a unified effort to reduce injuries and maintain high standards.
One of the most impactful changes came in the form of standardizing personal protective equipment (PPE). The introduction of cut-resistant gloves and consistent safety protocols nearly eliminated hand injuries. The company also identified its highest-risk activities and developed seven lifesaving rules to address them. These changes were rolled out efficiently, ensuring that employees could quickly adapt without disrupting operations.
Weekly “toolbox talks” became another cornerstone of the program. These 15-minute sessions brought employees together across departments to discuss safety challenges and share insights. “The toolbox talks helped break down silos and foster better communication between teams,” Dhillon notes.
Leveraging technology to simplify safety
Technology played a critical role in Carmichael’s safety transformation. Rather than introducing entirely new systems, Dhillon’s team enhanced existing platforms. By integrating hazard reporting and job hazard assessments into the work order system, the company made it easier for employees to comply with safety protocols. This practical approach minimized resistance and improved adoption rates.
“There’s always some challenges to change,” Dhillon acknowledges. “But by improving familiar systems rather than forcing entirely new ones, we gained the buy-in we needed.”
The changes weren’t just procedural. They improved morale and created a stronger sense of collaboration across teams. Employees, from technicians to supervisors, became more engaged in safety conversations, reinforcing the idea that workplace safety is a shared responsibility.
Looking ahead: Setting the standard for safety
With a strong foundation in place, Carmichael is planning to introduce a new Learning Management System (LMS) in 2025. The LMS will streamline safety training, allowing the company to deliver tailored programs and track participation more effectively. Dhillon sees this as the next step in Carmichael’s safety evolution.
“Our priority is to close gaps in safety training and continue reducing injuries,” she says. “We want to set a benchmark not just for ourselves but for the entire industry.”
Carmichael’s progress underscores the importance of leadership commitment and cross-departmental collaboration. While the changes required effort at every level, the outcomes of measurable improvements in safety and morale speak for themselves.
Dhillon emphasizes that the credit doesn’t belong to her alone. “This isn’t about me—it’s about Carmichael. It’s about a company that recognized a problem and came together to solve it. It’s about a president who sees every employee as family and a team that believes nothing is impossible when we work together.”