MLITSD is conducting proactive inspections in workplaces where workers may be exposed to hazardous materials
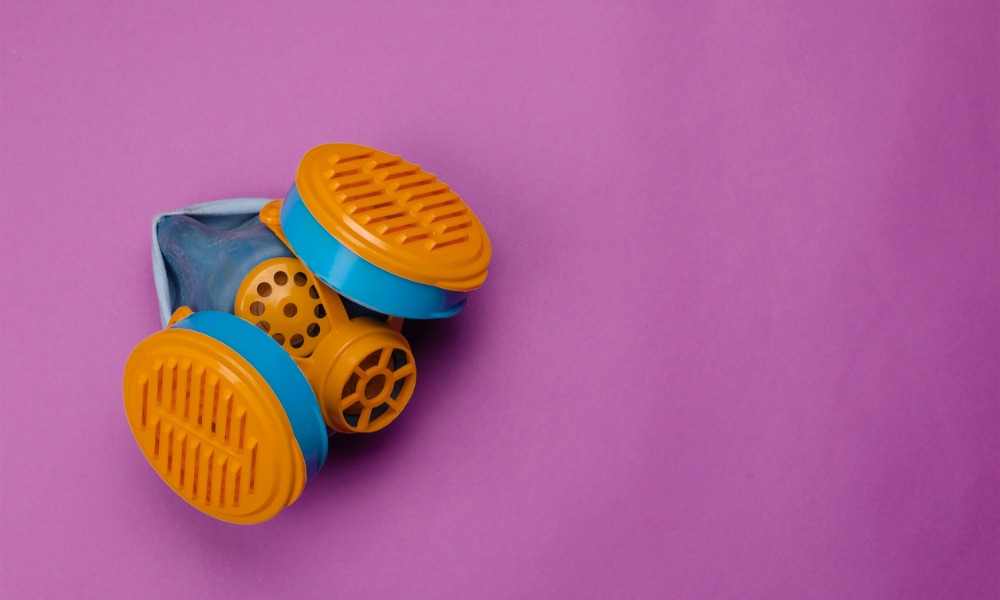
The Ministry of Labour, Immigration, Training and Skills Development (MLITSD) is in the midst of conducting two important occupational hygiene campaigns, with inspections underway and running until March 31, 2025.
So – what do employers need to know, and how should they be preparing?
The campaigns are designed to address the substantial risks associated with chemical exposure in the workplace. According to Toni Volpato, Specialized Consultant (Occupational Hygiene) at Workplace Safety & Prevention Services (WSPS), these are important measures to prevent occupational illness and even death.
“Shockingly, MLITSD reports list occupational diseases as the leading cause of worker deaths,” Volpato tells Canadian Occupational Safety. Every year, there are approximately four times more deaths from occupational disease than traumatic fatalities. (MLITSD Rationale for the Campaigns)
Exposure to hazardous chemical agents may result in a worker developing an occupational illness. Identifying, assessing and controlling these exposures will help lower the risk of workers developing an occupational disease.
“There’s a huge need to raise awareness and we need to do more to protect our workers.”
Campaign 1: Worker Exposures to Chemical Agents in the Workplace
The first campaign – Worker Exposure to Chemical Agents in the Workplace – has inspectors enforcing Regulation 833 regarding exposure to biological or chemical agents. In a nutshell, this means that inspectors will look at whether workers are being subjected to dangerous levels of hazardous substances.
During inspections, they will be assessing potential worker exposures, observing people at work, and considering what controls are in place. They’ll also review any existing exposure data that the employer may have.
If inspectors become concerned about over-exposure to hazardous agents, they may issue an order for an occupational hygiene air exposure assessment.
“This could involve capturing a representative sample of air in the workers’ breathing zone,” Volpato explains. “They’ll look at those results and compare them to the occupational exposure limits.”
Campaign 2: WHMIS training based on the amended Hazardous Products Regulations
The second campaign targets compliance with Regulation 860, which pertains to Workplace Hazardous Materials Information System (WHMIS) training.
This is particularly important given the 2022 amendments to the Hazardous Products Regulations (HPR), which gave suppliers until December 14, 2025, to update their safety data sheets (SDS) and labels. Employers must ensure they’re keeping pace with these changes.
Specifically, MLITSD hygienists will determine if retraining on WHMIS will be required depending on whether the hazardous products in the workplace have labels and safety data sheets that are compliant with the amended HPR.
“This is to ensure that everyone who comes into contact with the hazardous chemicals have the most up-to-date information on the hazards, and they know how to handle them safely,” Volpato explains.
“It’s going to be a relatively easy question for the inspectors. If they see the safety data sheets and labels have been updated to the new regulation standard, they’ll expect the employer to have done updated WHMIS training on the specific hazards of their chemicals, and how to handle them safely.”
How to prepare: The RACE model
Volpato highlights that the best way to prepare for an inspection is to have a comprehensive system in place to protect your workers. The RACE model – one of the most common processes adopted for dealing with workplace hazards – is a great starting point. It consists of four key steps: Recognize, Assess, Control and Evaluate.
Recognize – Start by reviewing your SDSs and labels. Is your SDS inventory complete and do you have a SDS for every hazardous chemical in your workplace? Do you have labels and SDSs that are compliant with the HPR?
Assess – Are you compliant with Ontario Regulation 833 and 860 (WHMIS)? Have you done an exposure assessment to determine if workers are over-exposed to hazardous chemicals in your workplace? "Often, you can’t know if people are over-exposed unless you have a qualified occupational hygienist come on-site to do an exposure assessment," Volpato points out. Have you completed WHMIS training, both generic and workplace specific to ensure everyone knows how to work safely with the hazardous products they handle or could be exposed to?
Control – Implement the hierarchy of controls to mitigate risks. This could include eliminating the hazardous chemical entirely, substituting it for something less hazardous, or introducing engineering controls like ventilation, developing safe operating procedures and training, and lastly personal protective equipment (PPE). “We always say that PPE is a last resort,” Volpato adds. “You don’t want to have to rely on people wearing PPE properly, which can also be uncomfortable for the workers. Employers are required to minimize the exposure first through elimination/substitution, engineering and administrative controls.”
Evaluate – After controls are in place, determine whether they’re effective. This might involve resampling the air and talking to workers to assess whether procedures are being followed and they’re working as intended.
Final thoughts
Ultimately, all these processes are focused on one objective – ensuring the health and safety of Ontario workers.
If inspectors become concerned about your workers’ exposure, they may write formal orders requiring you to take specific actions. If there is an immediate threat to health and safety, they may issue a stop-work order. The best way to avoid these scenarios is to be proactive about assessing and controlling your hazardous products.
“If you need assistance with any aspect of your hazardous chemical management system, reach out to an expert,” Volpato concludes.
“At WSPS we have many free resources, including a list of Frequently Asked Questions about the inspections, as well as qualified occupational hygienists across the province who can answer your questions and provide other services such as occupational hygiene airborne air exposure assessments, program development and training to support you.”
Find WSPS on social media:
LinkedIn: https://www.linkedin.com/company/workplace-safety-&-prevention-services/
X: https://twitter.com/WSPS_NEWS
Facebook: https://www.facebook.com/wsps.news