Oil and gas services company wins 2017 Young Worker Safety Award as part of Canada's Safest Employers
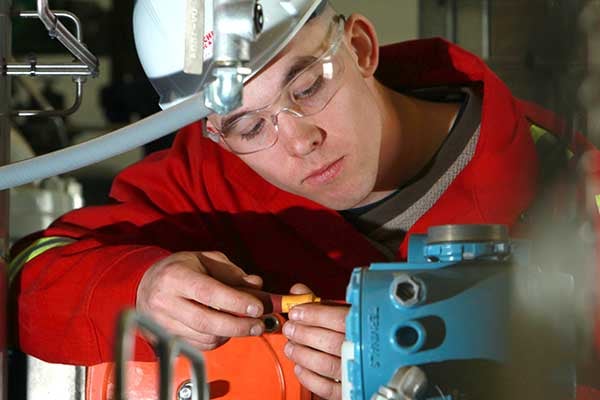
A main goal of the mentorship program at Techmation Electric & Controls is to impress upon young workers how critical their participation is to improving safety for themselves and others.
“We want to create an interdependent culture. Employees have a right to know what they’re doing and that it’s dangerous. We work in one of the most dangerous industries, oil and gas. But while they have the right to know what they’re doing, they also have the right to participate,” says Dan Hathaway, HSE manager at the electrical and instrumentation service provider in Airdrie, Alta.
“That’s what we’re trying to drive home: If we’re not doing something right, we want to know. And you must be ready to step up and help us figure it out.”
Nearly one-quarter of Techmation’s 855-employee workforce is under the age of 25. Every young worker is paired up with a qualified mentor for a period of time ranging from a few months to a year, depending on the tasks being performed. At the end, the mentor and mentee do a kind of exit interview in which the young worker is asked: Were there challenges? Did this procedure work? If not, how come? What are your suggestions to improve it? A summary of that discussion is sent to a supervisor for evaluation.
During his mentorship, James Borodawka, journeyman electrician and lead hand, who was 21 when he started at Techmation three years ago, learned to perform tasks on his own with confidence. He is now a qualified mentor.
“The program made me a better worker. They taught me well enough to know what I can and cannot do. It also taught me to become a mentor,” he says.
Borodawka says young workers are expected to participate in safety procedures to the same extent as experienced workers. All workers, for example, at the morning safety toolbox meeting, are asked to consider all possible risks involved in the task ahead. Each worker is also required to regularly write out a hazard identification card describing a hazard they have seen on the job site and tell how they mitigated it.
“Everyone must do it, whether they’re 18 and brand new or a 50-year-old journeyman,” adds Borodawka.
In May, Techmation introduced changes to its mentorship, or “green hand,” program. Until this year, all higher risk employees were identified with the same green hand sticker on their hard hat. Now, young workers have green stickers; new but experienced (short-service) employees have yellow stickers; and qualified mentors have blue stickers.
“That way, when you see someone with a young worker sticker on their hard hat, you should see someone with a qualified mentor sticker in pretty close proximity,” Hathaway says.
Techmation recently rolled out a learning management system to employees. One of its goals in adopting the new system was to create custom training packages for young workers, including training packages specific to first-year electricians.
When he came to work at Techmation, Borodawka already had three years of experience in his trade. In contrast to his previous job, he noticed right away a huge increase in attention to safety.
“When I came to Techmation, safety standards and procedures went through the roof,” he says. “Today... it keeps me coming back to work.”
This article originally appeared in the October/November 2017 issue of COS.