Global EHS director outlines wide-reaching firm's 'prevent reoccurance process'
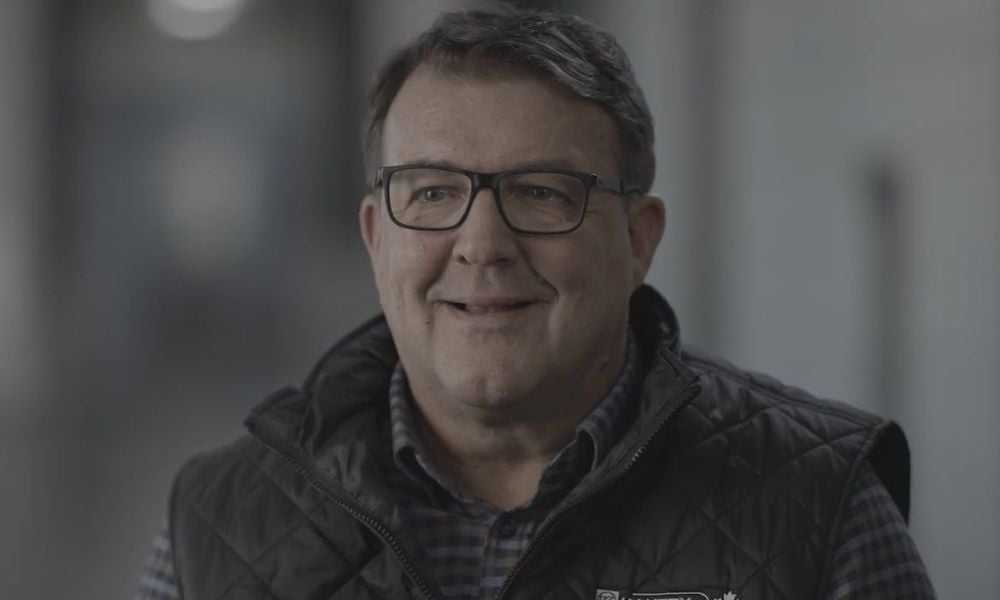
With 30 facilities across 13 countries, Kautex Textron is a Tier One automotive supplier with a large global footprint. And with over 5,000 employees working on four continents, workplace health and safety is of paramount importance.
Responsible for the wellbeing of these workers is Vince Vlaminck, Global EHS Director, who tells COS that the commonality between the layout of their factories helps manage compliance on a global scale.
“There are some small variations,” he says. “But for the most part, they're fairly homogeneous. We've taken the approach that the highest standards worldwide applies worldwide. So rather than a race to the bottom, we race to the top. If the highest standard comes from Europe or Mexico then that's the one that we apply worldwide.”
The process of managing these standards involves what Vlaminck refers to as their "prevent reoccurrence process." This system is pivotal in identifying injury trends and significant near misses, which are then categorized by topic and addressed accordingly.
"Within the functions working on possible maintenance topics or on operational topics...we identify common countermeasures and then roll those out around the world,” Vlaminck tells COS.
However, not every incident calls for an immediate, global response. As Vlaminck explains there’s a very balanced approach to incident management.
"You can't respond to every incident,” he says. “Or you're forever sending out to your 30 facilities a mixed bag of things that they have to respond to. We have an annual cycle - we save everything, categorize it and look for common things that we have to do across all cycles. Then we have quarterly meetings - we call them our safety review boards - and every facility has 10 to 15 minutes to report outward thereafter.”
These meetings not only foster healthy competition among the facilities but also enhance visibility and accountability.
“That’s been very effective for us - that overall oversight and cadence really helps us drive leadership across the globe.”
This passion for leadership development in safety is something that’s followed Vlaminck throughout his entire career. At Kautex Textron, Vlaminck says they’ve adopted a transformative approach to self-development – a strategy they call the “EHS functional workshop”.
"Our approach starts with a video that outlines key practices, followed by a playbook for a workshop tailored to each facility," he tells COS. “Every facility is responsible to host a workshop using the video as part of that core curriculum.”
The workshops are designed to foster local innovation while maintaining a consistent safety message across all locations. This method not only enhances team collaboration but also ensures that safety practices are adapted to the specific needs of each site.
"It really puts leadership at the point of impact with their team members and gives them a common cause to work on," adds Vlaminck.
And the participatory nature of these workshops results in greater employee buy-in and ownership of the safety protocols.
“Because the team members on the floor are involved, they have a much better chance of having sustained outcomes," he says. “[It’s about] building critical mass for culture across the organization.”
The collaborative approach to safety and wellbeing means that Vlaminck and his team have more time and support in rolling out new initiatives – including one recently which transformed safety protocols within their manufacturing. The program – known as the “two-zone” approach - targets materials management, with a specific emphasis on managing lift trucks within their manufacturing operations.
“We've really tried to eliminate lift trucks within our manufacturing area, or at least have them in that controlled zone on the perimeter of our manufacturing operation so that they're just dropping off pallets," Vlaminck explains.
And the “two-zone” approach also extends to their warehouse areas after Vlaminck’s team realized the need to minimize pedestrian traffic in order make the environment safer for lift truck operators.
"We've eliminated all unnecessary external traffic,” he added. “Now if you're entering the warehouse area, you have to announce yourself. It's been a journey that takes a while, but it's all been about reducing risk through that separation of power industrial trucks from our pedestrian/employee workforces.”