Supervisors need to be held accountable for erosion of standards
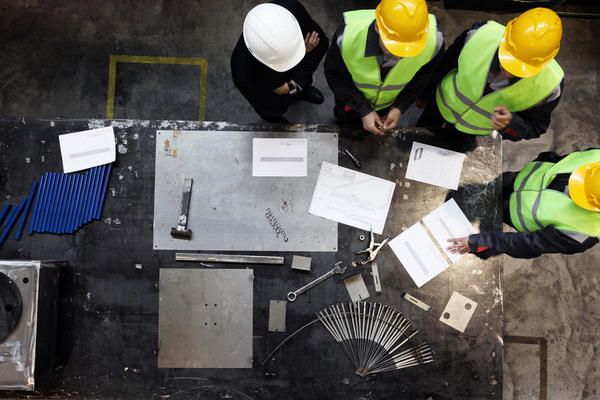
Every supervisor and manager will be faced with the challenge of how to respond when a worker engages in at-risk or unsafe behaviour. Do they provide coaching? Discipline? Or something entirely different? How they respond will be a critical factor in establishing the safety culture.
There are two key aspects to this challenge: understanding why the worker did what she did and ensuring the at-risk or undesired behaviour does not continue.
At-risk, unsafe or undesirable behaviours fall into a spectrum of categories defined as errors, violations and erosion of standards.
Error refers to the honest mistake, the human factors trap or the situation where the worker did not have the skill or knowledge to do the assigned task. For example, an incident could result when an untrained worker has been assigned a task with no instruction on how to do it and no guidance on what tools or equipment to use. The responsibility and accountability for this at-risk behaviour (and the incident that may result from the behaviour) lies with the supervisor. Yes, supervisors are accountable for the worker’s at-risk behaviour because the supervisor is the one who is responsible for providing the work direction, the training, the tools and the guidance. This is difficult for some supervisors to accept, but they must be held accountable for ensuring their workers are provided with the information, tools, training and support they need to do their jobs safely.
The term “violation” is used a lot in safety — overused and misused in many cases. Violations are those deliberate and wanton unsafe acts of a worker who has the knowledge, the equipment and the support to do the job safely — but chooses not to. For example, a work site has a clear rule in place that all workers must use fall protection when working above 3 metres. The training and equipment have been provided and the anchor points defined. The individual worker must be held accountable for not adhering to the standard. Most organizations have a discipline policy in place for dealing with these situations.
Here is the dilemma: Between 15 and 20 per cent of at-risk behaviours that result in incidents fall into the “error” category and three to five per cent can be defined as a “violation.” That leaves as much as 75 per cent unaccounted for, which falls into the “erosion of standards” category.
Erosion of standards are those situations where a standard does exist and workers are aware of it, but it is not always — or maybe never — followed. This occurs when a standard is not consistently enforced, it’s not possible to always follow the standard, the standard cannot be executed as written, the workplace norm is to not follow the standard, the supervisor has witnessed the unsafe behaviour and not addressed it or the standard is not viewed as being relevant or important.
“Erosion” is an apt term in that the situation has arisen over time with just a little variation from the standard at first, then a wider spread and more frequent variance and then finally, a situation where one may ask, “How did we get into this position?” We end up in a position where more than one worker, possibly the entire work team, is not following the standard. This is where the struggle begins for most supervisors. They need to be held accountable for the erosion of standards in their workplace and they need to address it, but the traditional approaches for managing performance issues may not be appropriate.
In this situation, it will be ineffective to use the approaches for addressing error, such as training, as the workers are already trained. It will be inappropriate to discipline just the one worker who had the incident when everyone else also engaged in the unsafe behaviour. A supervisor may now feel overwhelmed with this dilemma — he is being held accountable for the actions of his work team but doesn’t have a process for dealing with erosion of standards.
Fortunately, there is a simple process that can help a supervisor deal with these performance issues that could be the source of 75 per cent of unsafe behaviours. A discussion planner is a simple six-step process that can help a supervisor lead a discussion with her entire work team to address a specific standard that is of concern.
• Define the issue. The supervisor states the facts of what he has seen. For example, “We have been monitoring the vehicle traffic on our work site and the average speed is 50 kilometres per hour (kph). Our standard is 30 kph.”
• Demonstrate the importance. The supervisor needs to show the relevance of the standard. For example, “We have a 30 kph limit to ensure the safety of the pedestrians on our site.”
• Set expectations. The supervisor sets explicit expectations for how the standard will apply: “The speed limit on the site is 30 kph. This applies to all vehicles and all mobile equipment including trucks, forklifts, loaders and ATVs”
• Outline the action plan. Define exactly how the standard will apply and be enforced: “The speed signs have been posted throughout that state 30 kph maximum speed. Speed will be monitored with random checks using a radar gun.”
• State the consequences. Now that the standard is clear, the supervisor can state clear consequences: “Drivers will receive a warning on the first occasion where they have exceeded the speed limit. A second exceedance will result in the loss of driving privileges on site.”
• Restate the importance: The supervisor makes it personal and states why it is important to him and why it should be important to the work group.