Ignoring cultural differences, thinking of safety as a cost among oversights
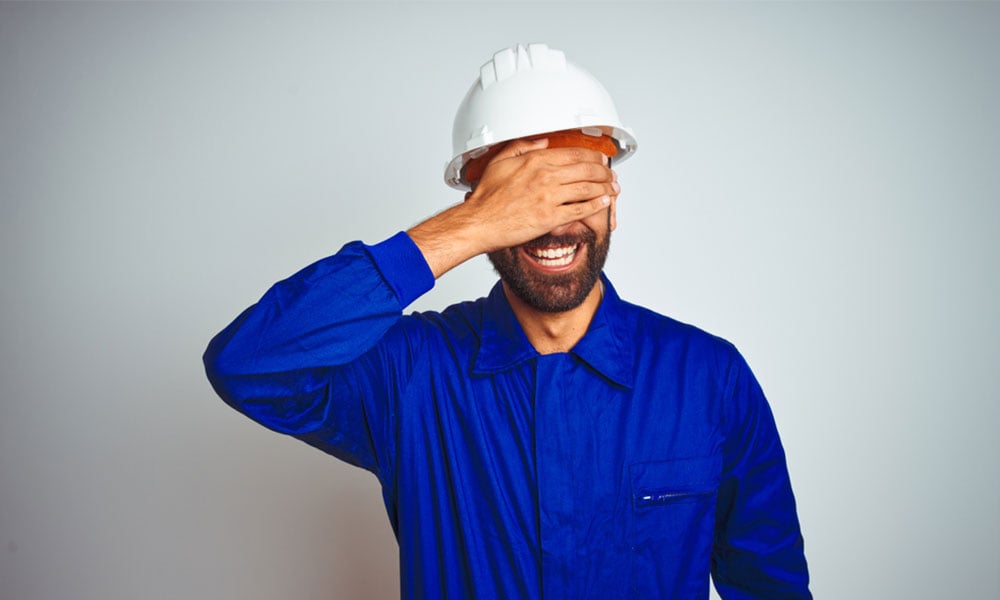
I’ve spent nearly my entire life in the business of making gloves to protect workers’ hands. In the course of my work, I’ve seen the disastrous effects of workplace injuries, and I’ve seen fingers, hands, and even lives saved with the proper safety precautions.
When workers put their bodies and lives in harm’s way for your company, it’s your moral and legal responsibility to keep them safe. By avoiding these 10 common mistakes, you can do just that, preventing accidents before they occur.
1. Thinking safety is a line responsibility instead of a top management responsibility
Way too often, the people in the tops of office towers think of safety as some kind of regulatory checkbox or housekeeping item — something you delegate down to lower-level supervisors or the workers themselves.
But here’s the deal: without safety leadership coming from the very top, no company will ever develop a genuine culture of safety. Without a culture of safety, you will never see safety thinking at every level of a company, or a true spirit of team safety, or consistently good decisions made right down to the level of the guy or gal operating the pneumatic drill.
2. Looking at safety as an additional cost
Plenty of companies put up signs that say “safety first” at their plants, but for many, their actions don’t align with their words.
Once you start “budgeting for safety” and thinking of it as a “cost” in your ledger, you have already lost sight of safety first.
Safety should not be a budget item. According to Paul O’Neill, former CEO of Alcoa, “Safety should never be a priority. It should be a precondition. Like, before you can get up and walk around, you have to breathe. Safety should be like breathing. It should be a precondition for organizational behaviour.”
3. Thinking some accidents are inevitable
You must always work from an assumption that you can get your company to zero injuries. The minute you admit that some rate of injury is inevitable, you’re subscribing to fatalism and relinquishing responsibility for safety.
If you say, “Nothing could have been done to prevent that,” you’re crippling future preventive measures. If you say, “Humans are imperfect, so bad stuff will happen,” you’re ensuring the next round of bad stuff.
If you’re a safety manager, supervisor, or anyone in authority, you must always, in all circumstances, say that the only acceptable number of injuries is zero. Full stop.
4. Using misguided safety incentives
In an effort to improve their safety records, some companies offer misguided incentives, like rewarding any work crew that goes three months injury-free.
To the ignorant, this may seem like a logical and positive step, but it’s a bad idea.
Research has proven that such incentives lead to the covering-up of injuries, rather than the reduction of injuries. Managers and even workers will simply stop reporting incidents so as not to break their streak and win a prize.
For useful incentives, instead reward positive efforts to create safe conditions, like rewarding workers for wearing personal protective equipment (PPE).
5. Saying you can’t fix stupid
Again and again, I have heard the refrain, “You can’t fix stupid.” As if, no matter what safety precautions are taken, people are ultimately responsible for their own safety, and if they do stupid things, they’ll get stupid injuries.
This is a dangerous, even an unforgivable attitude. It means you are assuming that some injuries are inevitable, and you are ignoring the chain of responsibility which leads to all injuries, which are never just one person’s fault.
Injuries don’t happen because people are stupid; they happen because of a lack of training, improper PPE, or a poor safety culture.
6. Forgetting your workers speak different languages
I can’t tell you how often I’ve been in factories or out on construction sites where most of the workers speak little or no English, but all the safety signs and all the safety training are only in English.
A manager once actually told me, “Well, if they want to work here, they need to learn English eventually,” as if until they learned better English, they were somehow expendable.
Safety is non-negotiable, regardless of the language one speaks. If you have multilingual workers, you must put in the time, effort, education, and additional money required to ensure their safety.
7. Ignoring cultural issues
In the most dangerous professions, a high proportion of the workers are often from other countries. This leads to dangerous mismatches of culture.
People from other countries often have very different cultures when it comes to health and safety. Immigrants may forego proper PPE and fail to report injuries because they underestimate the severity of injuries, want to appear tough, or are worried about losing their job.
It’s your responsibility to protect people. That means understanding cultural differences and making all your workers comfortable reporting injuries, unsafe conditions, and unease about the safety of certain tasks.
8. Bad PPE buying and storing habits
No one should be allowed to select PPE who does not have direct experience with the work. Otherwise, improper PPE will be bought. Either it will not provide adequate protection, or it will provide too much protection, at the expense of being too bulky or uncomfortable to actually use.
Storage of PPE is also important. Many companies take special care of their expensive PPE by locking it carefully away on the far side of the plant. But if PPE is not easily accessible and convenient for workers, they won’t use it. Good PPE is valuable, but only if it’s used.
9. Settling for lousy training and dull trainers
The state of safety training in the industry is surprisingly abysmal. Often it’s just a checkbox for management, without any real thought going into the process. As a result, much training fails to produce any results, and the trainers don’t seem to realize why it has failed. “These workers are just dumb,” they say. “They don’t listen.”
But guess what? If workers aren’t listening to your training, it’s your failure, not theirs. Most likely, your training is too generic or boring. It’s your responsibility to make the training engaging.
10. Keeping useless stats
Probably you keep statistics on your annual rates of injury. On average you had, say 12 per month this year, and 14 per month last year.
Congratulations, you improved a little over last year. But excuse me for asking: How does knowing that actually help you make people safer?
For injury stats to be useful, they need to be very detailed. You need to know what specific injuries are happening, what machines are involved, what PPE is being used, and more. Having that kind of information will allow you to identify patterns and take action to prevent future injuries.
This article was adapted from the book Rethinking Hand Safety, written by Joe Geng.