Managers can make or break a safety culture
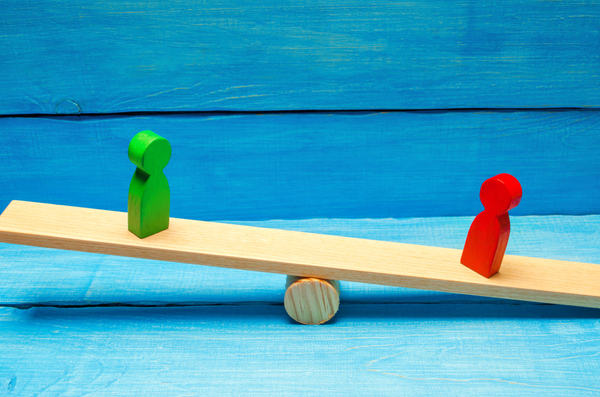
The safety culture of an organization is the outcome of the safety management systems, the people in the organization, the safety history, the stories, the corporate memory and, by far the greatest influencer, the actions, values and involvement of the managers. The things that managers do and say concerning safety can form the basis of a strong safety culture or can be the factor that will undermine it.
My safety career has exposed me to all kinds of managers. There were the best of managers and the worst of managers. I have seen managers of integrity, and those of dishonesty. There have been caring managers, and those with contempt for workers. There are managers who build strong safety cultures, and managers who have undermined the very foundation of the culture.
Let’s take these management traits that impact safety culture and consolidate them into two fictitious managers. We will call our ideal manager Paul, and the other, let’s make him John.
Paul understood safety management. He took the time to actually read the entire safety management system manual. He asked questions about anything in the manual that he didn’t understand. His hard copy manual had highlights and notes throughout. Paul appreciated that safety management was complex and he used his safety professionals as resources when dealing with issues to ensure he had a solid grasp of the science of safety.
John had trouble finding his copy of the safety manual during an audit. When we did find it, the revisions and accompanying change management documents were still in their original wrapping and were stuffed into the front cover, unopened.
“Safety is simple,” he protested. “You just put a procedure in place and you make people follow it.”
Paul framed his safety goals and targets in a vision statement. He stated that he didn’t want any of his people to be hurt and, no matter what the past safety performance had been, he sincerely believed they could always do better. When things did go wrong, he insisted on a thorough investigation to determine the causes and he was very aware that causes could be related to the management systems, the equipment and the people. He was also astutely aware that incidents had multiple causes and that he himself and the managers reporting to him may have control over some of those causes.
John’s safety goals and targets always looked like a computer-generated spreadsheet: A 52 per cent reduction in total recordable injuries (TRI) to achieve a rate of 2.00 and a lost-time injury (LTI) reduction of 74 per cent for a 1.00 rate. When the calculation of injury frequency was explained to John, he actually asked if there were ways we could increase the denominator (work hours) to reduce the injury rate. Yes, he did demand investigations of incidents but rather than the “Paul” approach of looking for the multiple causes with accompanying recommendations for improvement, the “John” approach was to find who was at fault (always the injured worker in his mind) and hold them accountable (punish them for ruining his safety record).
The Pauls in our organizations see the value in proactive reporting. They know that the near misses provide information about what is going on in the workplace and how they can be used to prevent more serious incidents. They know that proactive reporting can be an indication of worker involvement in safety and they encourage the reporting of all near misses.
Managers similar to John can undermine proactive reporting with reactions to near miss reports like, “That’s the stupidest thing I have ever seen and that guy should be fired.” Word gets around fast and proactive safety information can quickly disappear under a John-type response.
Paul cared for his people. He regularly put his work boots on and got out into the workplace to talk to the workers and to ask how things were going. He listened. He also made it clear to the workers what his standards were — and they were high when it came to safety. Paul had a sincere way of engaging workers and getting them to buy-in to the safety goals. He used “Thank you” and “I appreciate what you are doing here” as his recognition for a safe workplace.
John managed safety from the office. He much preferred looking at a spreadsheet than talking with workers. When he was forced to be in the workplace to meet his audit obligations, he would leave a trail of discouraged workers in his wake. He attempted to buy worker engagement into safety with elaborate incentive schemes and punishment regimes if they dared to have an incident. When John was cautioned that one of his especially harsh punishment plans would generate fear in the organization, he responded with an enthusiastic “I want to see what fear will do!”
The Paul way of understanding safety culture was to conduct a formal safety perception survey. A John prefers his own judgement of how things are going. Paul regularly meets with his safety professionals for updates, guidance and advice. John doesn’t know who his safety professionals are. Paul views safety as his responsibility. John says that’s what the safety people do. Paul spends up to 20 per cent of his time on safety. John only does what he has to for audit scores. Paul leads safety. John drags it down.
So, now that we know what the best of managers look like (Paul) and the characteristics of the worst (John), what do we do about it? If you have a Paul, congratulations, and continue to reinforce the things he does. If you have a John, remember the culture of your organization is shaped by the manager, so it’s unacceptable to simply accept it and do nothing. The challenge becomes: How do you move your John-type manager along that scale from worst to best? This won’t be easy and it won’t happen overnight. It will involve providing feedback to your John and, where possible, providing it formally through a perception survey. It will mean ongoing coaching to show your manager how his or her actions impact safety. If they choose not to change, you cannot afford to have the safety culture undermined by their actions and it may be time for the talk: “You don’t fit with what we are trying to achieve in safety and we will need to remove you from your position.”
It might be by far the best thing you have ever done to impact your safety culture.
This article originally appeared in the December/January 2019 issue of COS.