SDS RiskAssist prove its domination of sector by being crowned a COS Readers’ Choice winner for the seventh successive year
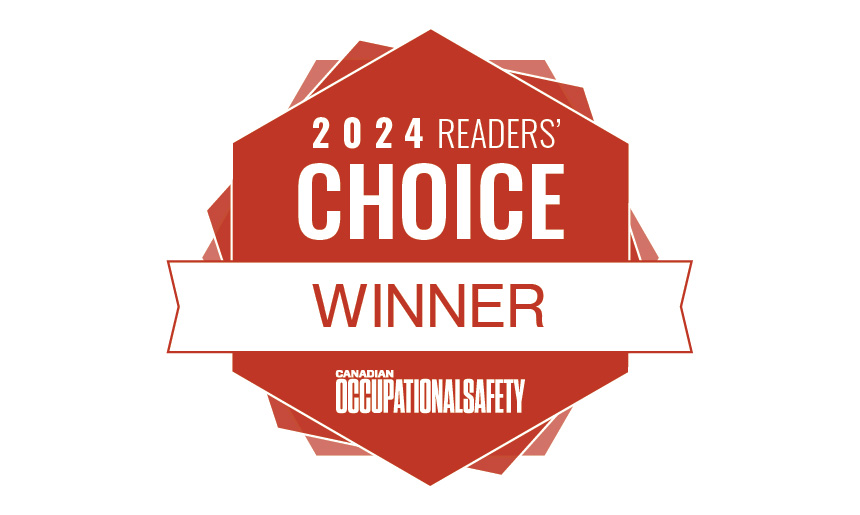
The Ontario-based firm is successfully carrying out its mission to ensure every Canadian worker handling chemicals understands the hazards and knows how to protect themselves.
The effort is driven and the brainchild of co-founder and CEO Lisa Hallsworth, who’s quest for a better and easier way to manage workplace chemicals began while working for some of Canada’s largest chemical companies.
It was evident to her just how high the stakes are when it comes to on-the-job chemical safety.
As an extension of this, Hallsworth witnessed first-hand how time-consuming and stressful it was for OHS leaders to meet WHMIS requirements, including ensuring safety data sheets are always up to date.
“We now know that occupational disease is the leading cause of workplace deaths, claiming at least four times more lives than traumatic accidents at work,” she says.
According to SDS RiskAssist data, a typical Canadian workplace uses about 100 chemical products and about 70% of these have WHMIS hazards that may affect the health and safety of employees, ranging from skin irritations, respiratory issues and even cancer.
Hallsworth and her team developed a software system to help ensure employees remain free of injury or illness. She explains, “Technology is the answer to manage WHMIS complexity and ensure everyone has the information they need for a safe, healthy, sustainable workplace.”
Digital assistant
SDS RiskAssist likens itself to a digital WHMIS compliance assistant for busy safety leaders and has become even more important in the workplace as the number of chemical products has increased.
Their software enables municipalities, manufacturers, colleges and universities, government labs, dental clinics and other clients to meet their WHMIS obligations with intuitive tools that:
- Instantly identify all chemical hazards on site at the click of a mouse
- Track chemical product inventory
- Ensure all workers have 24/7 access to up-to-date SDSs
- Provide job-specific training as required by WHMIS
“OHS leaders tell us that one WHMIS requirement in particular – keeping SDSs up to date – is their biggest pain point,” Hallsworth adds. “Keeping them up to date for even 50 chemical products is an incredibly difficult task without software. You need to regularly review each SDS, ensure it is the current version, cross-reference ingredient information with applicable regulations, summarize your priorities, and only then can you act on those priorities.”
And she continues, “Plus, there’s a lot of uncertainty about when to update an SDS, suppliers often change due to mergers and acquisitions, and it can be difficult tracking down SDSs from suppliers in other countries.”
Taking the pain out of SDS updates
SDS RiskAssist also offers a full-service option that eliminates the work of updating SDSs altogether.
“Two years ago we introduced a subscription model for full service SDS updating,” comments Hallsworth. “Paying a little extra to have our experts and technology do the updating just makes sense for many of our clients.”
The platform follows a rigorous process to review, verify and update each SDS in a collection, according to a schedule based on a number of factors and key data points.
The client is notified of any changes and encouraged to review workplace procedures for any SDS that has a change in hazards.
Hallsworth says, “SDS RiskAssist documents the verification process, creating an audit trail so our clients know exactly where they stand on SDS replacement at all times.”
This service is regarded as a “game changer” as it allows clients to focus on using the other SDS RiskAssist tools to build a robust health and safety culture, knowing that all their SDSs are current and WHMIS-compliant.
“It’s another example of how innovative technology can not only help ensure compliance but also enable OHS leaders to fulfill the actual intent of WHMIS: to create healthy workplaces,” Hallsworth shares.