'Our goal is to phase out the dull, dirty, and dangerous jobs' says vice president
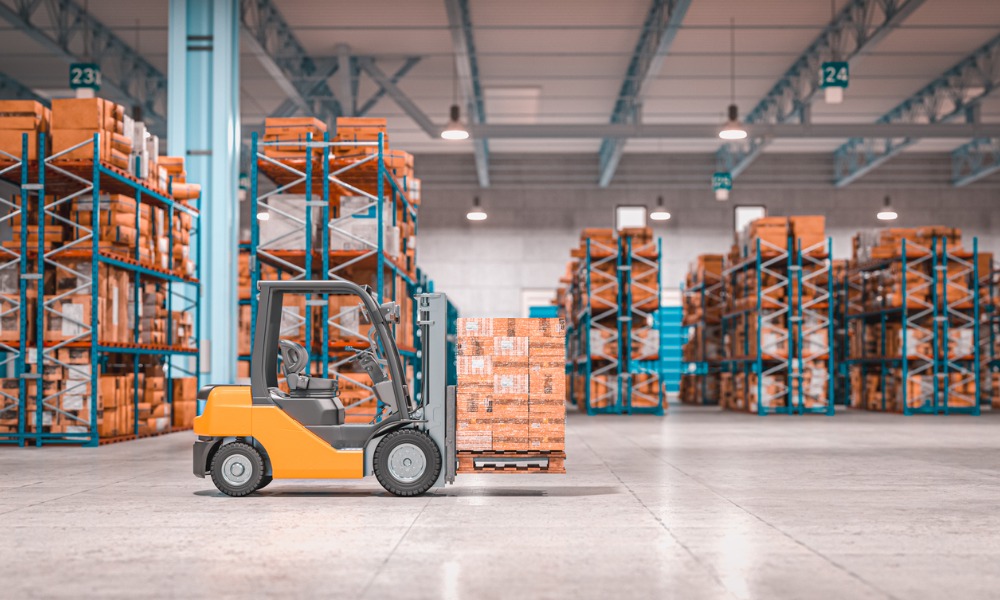
The manufacturing sector is undergoing a significant transformation, with advancements in technology playing a central role in improving workplace safety. As companies like CGC Inc. embrace new technologies, they’re not only addressing the industry's most dangerous tasks but also redefining safety protocols across their operations. "We’re in a period of transition," says Steve Forcier, vice president of manufacturing at CGC, a major player in the gypsum wallboard products industry. "Our goal is to phase out the dull, dirty, and dangerous jobs, replacing them with automation, remote control operations, and robotics."
At CGC, the emphasis is on eliminating repetitive, physically demanding tasks that often lead to injury or fatigue. Forcier explains how automation is being used to tackle these issues: "Repetitive tasks, like moving boxes from one area to another, lead to strain injuries. Now, we’re using robots to handle these jobs, reducing the risk of injury and keeping workers focused on more complex tasks." By automating mundane tasks, the company is also preventing workers from becoming complacent or distracted—factors that often lead to accidents.
One of the most exciting advancements has been in the use of remote-controlled equipment in CGC’s mining operations. "Traditionally, operators would be right next to the machinery, exposed to potential hazards. Now, we've removed the controls from the equipment, and operators use remote controls from a safe distance," says Forcier. This shift has significantly improved safety by distancing employees from dangerous conditions, allowing them to operate heavy machinery with the precision and familiarity of a video game.
The introduction of these technologies has led to significant safety improvements, but it’s also reshaping the workforce. Forcier acknowledges that concerns over automation potentially eliminating jobs are common. However, he stresses that automation is changing—not reducing—the workforce. "We need more people who understand electronics, programming, and scheduling. Automation doesn’t replace jobs; it creates new opportunities that require a different skill set," he explains.
The technological shift isn’t limited to equipment operations. Training methods are also evolving to keep up with these changes. CGC has integrated advanced simulations for onboarding new employees. "Instead of reading through pages of instructions, our workers now train in simulators. It’s more engaging and far more effective, especially when it comes to operating large, potentially hazardous machinery," says Forcier. These immersive training experiences ensure that workers are better prepared and more confident when they eventually step onto the production floor.
Forcier highlights that employee involvement is key to the success of these new initiatives. "We're involving our employees in the decision-making process because they know the dangers better than anyone," he says. The shift in culture—from simply following orders to being actively engaged in safety improvements—is crucial. Forcier emphasizes, "The workforce is different now. It deserves better. We ask for their ideas, listen, and implement solutions."
Looking ahead, Forcier believes that the companies resistant to these changes will struggle to survive. "The workforce is changing, and so are the demands. Companies that don’t prioritize these technological advancements and fail to diversify their talent pool will not succeed," he warns. Forcier urges companies to ensure that their leadership prioritizes these transitions, not just in terms of funding but also in cultural shifts. "Leadership needs to evolve. Supervisors are no longer the sole decision-makers; they need to be open to the input of their teams."
As CGC continues to adopt new safety measures, Forcier leaves a message for other health and safety professionals: "We need to focus on safety actions, not just safety results. Involving employees in the development of safety systems is crucial. The more engaged they are, the safer our workplaces will be." With the right balance of technology and employee engagement, CGC is setting the stage for a safer and more efficient future in manufacturing.