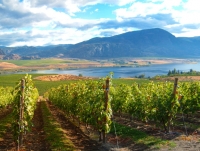
Looking back over the first decade of the new millennium, one thing that stands out is the increasing number of organizations that incorporated environmental initiatives into their traditional workplace health and safety departments and practices. If the last ten years are any indication, this is a trend we can expect to continue going forward.
While the alignment of environmental initiatives with health and safety practices has benefitted companies from a cost-efficiency standpoint, it has also helped health and safety managers understand the confluence these two initiatives share. To that end, many environment, health and safety professionals have found ways to incorporate the intersecting interests of environment and health and safety into mutually beneficial policies and procedures.
Jeremy Shorthouse is one such professional. As the national environmental, health and safety manager for winemaker Vincor Canada, as well as COS magazine's Safety Leader of the Year for 2010, Shorthouse knows that safety comes first. He's also aware, though, that sometimes you can protect both your workers and the environment all at the same time. He pointed to water specifically as one workplace issue that impacts both workplace safety and the environment.
"One critical crossover is definitely water," said Shorthouse. "Water is a part of our business just because of the fact that we're making wine. There are water additions and constant cleaning and so on, and that water obviously produces slippery floors. The more we can reuse our water the better, because it both saves water and keeps it off the floor. Reducing water usage means reducing slip hazards at our sites and in our cellars."
But the overlap doesn't end there. Chemicals are another big concern. Any chemical agent that can cause harm to the environment tends to have a similar effect on a human being, and vice versa. It's something that Shorthouse and Vincor take very seriously, both with regard to their workers and to the environment. As a company whose products are being consumed by the public, they have to.
"There are definitely chemicals used in our processes," said Shorthouse. "We use sulphur additions to do the wine. Realistically, there's not enough being used that we have to worry about the environment too much, but it does affect the environment of the employee. We have full-face respirators on our workers for that sort of thing."
"On the other side of that, a lot of times we're using very caustic chemicals for our cleaning purposes, which we have to make sure aren't leaked into the sewer system, where they might have an adverse effect. We ensure that our caustic materials are neutralized and have a positive pH level by adding additions. That way they can be taken by the city without causing any problems."
The adoption of interconnected environmental and health and safety departments continues to take place across the country as companies recognize the benefits of uniting these overlapping interests under a single banner. It's a marriage of mutual interests that Bob Whiting, a senior project manager with the Canadian Centre for Occupational Health & Safety (CCOHS), thinks is a good fit.
"I'd say it's the case that companies do a better job with safety and with environment when the two work together or are grouped together," said Whiting. "There are certainly lots of examples of that. You get better solutions to these sorts of problems when the environmental aspects and health and safety aspects are considered at the same time. With health and safety, I think it's mainly a question of thinking about how a company's work affects the environment, and figuring out how it can cause less of an impact."
Shorthouse feels that the workers themselves are also buying in and becoming more environmentally conscious, which means they are also beginning to understand the impact that environmental issues can have on worker safety.
"Our employees are becoming more focused on reducing and reusing energy and water, and helping out with these sorts of projects in whatever way they can. They're doing this for three reasons: 1) they know they're ultimately helping the bottom line; 2) they know it can help to reduce health and safety risks; and 3) they know we are doing better for the environment."
"I always tell the people in our organization: 'We are a part of the environment. That's where our product comes from: the Earth.'"
While the alignment of environmental initiatives with health and safety practices has benefitted companies from a cost-efficiency standpoint, it has also helped health and safety managers understand the confluence these two initiatives share. To that end, many environment, health and safety professionals have found ways to incorporate the intersecting interests of environment and health and safety into mutually beneficial policies and procedures.
Jeremy Shorthouse is one such professional. As the national environmental, health and safety manager for winemaker Vincor Canada, as well as COS magazine's Safety Leader of the Year for 2010, Shorthouse knows that safety comes first. He's also aware, though, that sometimes you can protect both your workers and the environment all at the same time. He pointed to water specifically as one workplace issue that impacts both workplace safety and the environment.
"One critical crossover is definitely water," said Shorthouse. "Water is a part of our business just because of the fact that we're making wine. There are water additions and constant cleaning and so on, and that water obviously produces slippery floors. The more we can reuse our water the better, because it both saves water and keeps it off the floor. Reducing water usage means reducing slip hazards at our sites and in our cellars."
But the overlap doesn't end there. Chemicals are another big concern. Any chemical agent that can cause harm to the environment tends to have a similar effect on a human being, and vice versa. It's something that Shorthouse and Vincor take very seriously, both with regard to their workers and to the environment. As a company whose products are being consumed by the public, they have to.
"There are definitely chemicals used in our processes," said Shorthouse. "We use sulphur additions to do the wine. Realistically, there's not enough being used that we have to worry about the environment too much, but it does affect the environment of the employee. We have full-face respirators on our workers for that sort of thing."
"On the other side of that, a lot of times we're using very caustic chemicals for our cleaning purposes, which we have to make sure aren't leaked into the sewer system, where they might have an adverse effect. We ensure that our caustic materials are neutralized and have a positive pH level by adding additions. That way they can be taken by the city without causing any problems."
The adoption of interconnected environmental and health and safety departments continues to take place across the country as companies recognize the benefits of uniting these overlapping interests under a single banner. It's a marriage of mutual interests that Bob Whiting, a senior project manager with the Canadian Centre for Occupational Health & Safety (CCOHS), thinks is a good fit.
"I'd say it's the case that companies do a better job with safety and with environment when the two work together or are grouped together," said Whiting. "There are certainly lots of examples of that. You get better solutions to these sorts of problems when the environmental aspects and health and safety aspects are considered at the same time. With health and safety, I think it's mainly a question of thinking about how a company's work affects the environment, and figuring out how it can cause less of an impact."
Shorthouse feels that the workers themselves are also buying in and becoming more environmentally conscious, which means they are also beginning to understand the impact that environmental issues can have on worker safety.
"Our employees are becoming more focused on reducing and reusing energy and water, and helping out with these sorts of projects in whatever way they can. They're doing this for three reasons: 1) they know they're ultimately helping the bottom line; 2) they know it can help to reduce health and safety risks; and 3) they know we are doing better for the environment."
"I always tell the people in our organization: 'We are a part of the environment. That's where our product comes from: the Earth.'"